The burning temperature of a furnace depends on the type of furnace, the fuel used, and the specific application. Furnaces can operate across a wide temperature range, typically from 200 °C to 1800 °C, depending on the fuel and process requirements. For instance, when dry fuel is burned, temperatures can range from 300 °C to 1800 °C, while burning coal-water slurry (CWS) results in a lower range of 200 °C to 1200 °C. Continuous furnaces, used for heat treatment processes like annealing or hardening, maintain consistent temperatures tailored to the material and process. Muffle furnaces, on the other hand, should operate 50 °C below their maximum rated temperature to ensure longevity and safety, with environmental factors like humidity and corrosive gases also influencing their operation.
Key Points Explained:
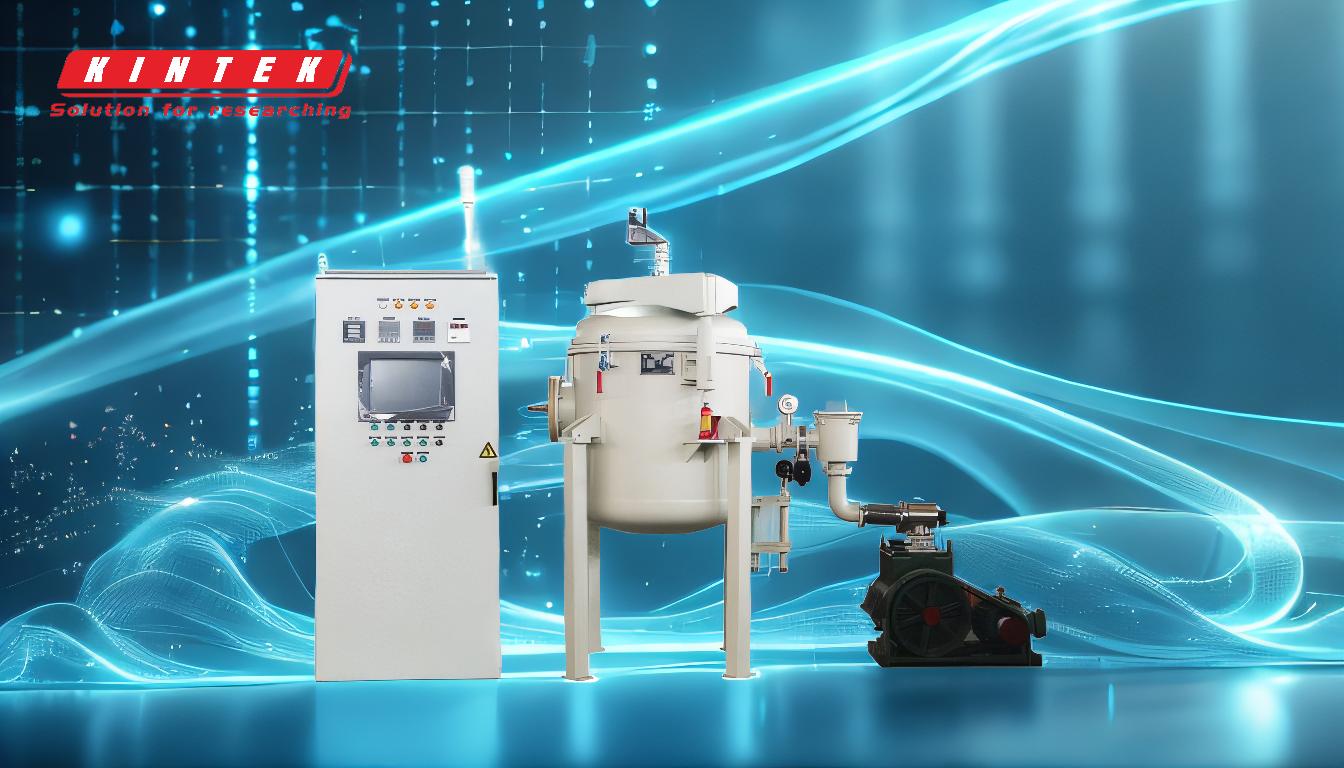
-
Temperature Range Based on Fuel Type:
- The burning temperature of a furnace varies significantly depending on the fuel used.
- Dry fuel combustion can achieve temperatures between 300 °C and 1800 °C.
- Coal-water slurry (CWS) combustion results in a lower temperature range of 200 °C to 1200 °C.
- This variation is due to differences in combustion efficiency, energy content, and heat transfer characteristics of the fuels.
-
Continuous Furnaces and Process-Specific Temperatures:
- Continuous furnaces are designed for specific heat treatment processes such as annealing, hardening, normalizing, or carburizing.
- These furnaces operate at consistent, process-specific temperatures to ensure uniform treatment of materials.
- The temperature is determined by the type of steel or material being processed and the desired heat treatment cycle.
-
Muffle Furnace Operating Guidelines:
- Muffle furnaces should operate 50 °C below their maximum rated temperature to extend the lifespan of the heating elements.
- They must be used in environments with relative humidity below 85% and free from conductive dust, explosive gases, or corrosive gases.
- When heating materials that release volatile gases (e.g., metals with grease), sealed containers or proper ventilation should be used to prevent damage to the heating elements.
-
Environmental and Operational Considerations:
- The operating temperature of a furnace is influenced by environmental factors such as humidity, dust, and the presence of corrosive or explosive gases.
- Proper maintenance and adherence to operational guidelines are critical to ensure safety, efficiency, and the longevity of the furnace.
By understanding these factors, a purchaser can select the appropriate furnace type and operating conditions for their specific needs, ensuring optimal performance and durability.
Summary Table:
Factor | Details |
---|---|
Fuel Type | Dry fuel: 300 °C–1800 °C; Coal-water slurry: 200 °C–1200 °C |
Continuous Furnaces | Operate at consistent, process-specific temperatures for heat treatment |
Muffle Furnaces | Operate 50 °C below max rated temperature; humidity <85%, no corrosive gases |
Environmental Factors | Humidity, dust, and corrosive gases affect furnace performance and safety |
Need help selecting the right furnace for your application? Contact our experts today for personalized advice!