A burnout cycle on a furnace refers to the process of heating an investment mold to eliminate wax or organic materials before casting metal. This process is critical in industries like dental and jewelry manufacturing, where precision and cleanliness are paramount. The burnout cycle typically involves controlled heating rates and specific temperature holds to ensure complete removal of the wax without damaging the mold. Modern burnout furnaces, such as those used in dental applications, often feature rapid heating rates, up to 100 degrees Celsius per minute, to enhance efficiency and reduce processing time. This cycle is essential for preparing molds for metal casting, ensuring high-quality final products.
Key Points Explained:
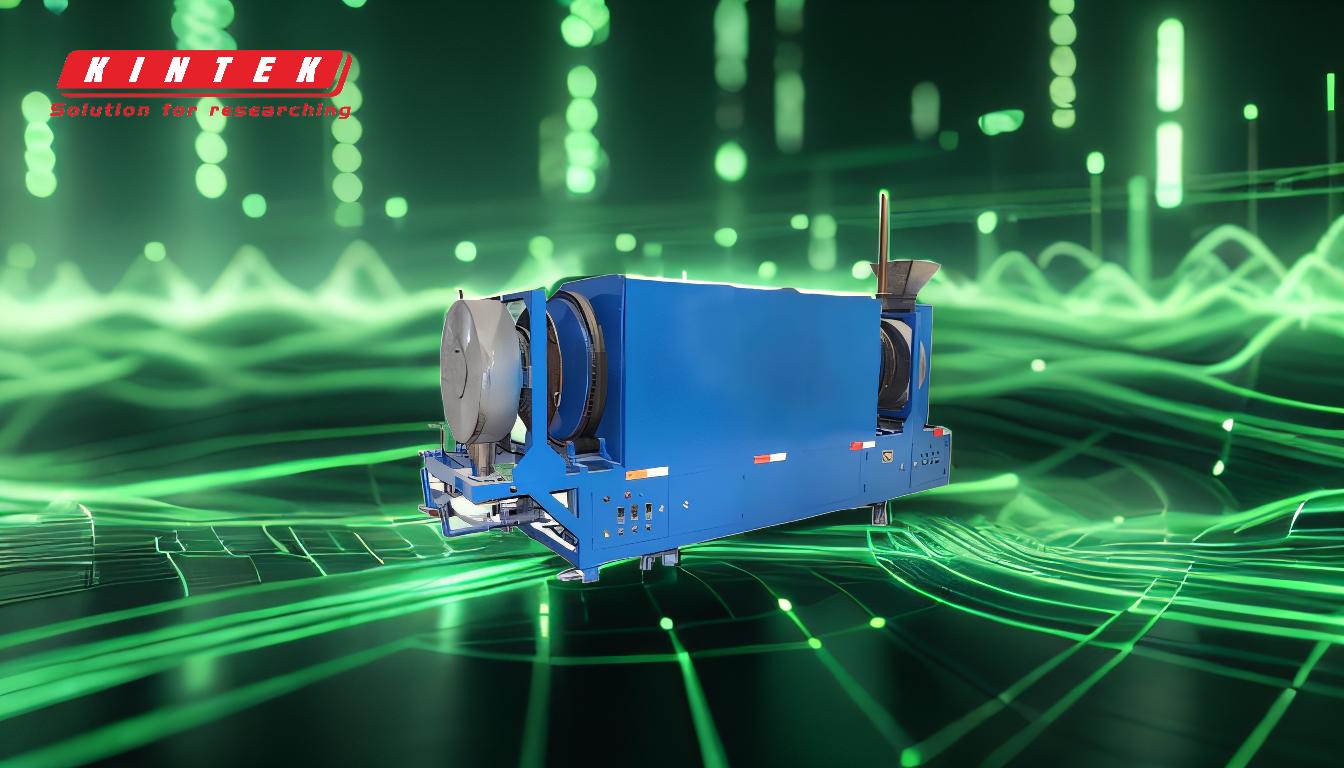
-
Purpose of the Burnout Cycle:
- The burnout cycle is designed to remove wax or organic materials from investment molds. This step is crucial in processes like metal casting, where any residual material could compromise the integrity of the final product.
- In dental applications, this process is used for metal-casting wax burnout, lithium disilicate press ingots casting wax burnout, and 3D metal printing heat treatment.
-
Stages of the Burnout Cycle:
- Initial Heating: The furnace gradually increases the temperature to soften and melt the wax. This stage prevents cracking or damage to the mold.
- Wax Elimination: As the temperature rises further, the wax evaporates or burns out completely. This stage often involves holding the temperature at specific points to ensure thorough removal.
- Final Heating: The furnace reaches its peak temperature to prepare the mold for metal casting. This step ensures the mold is clean and ready for the next stage of the process.
-
Equipment Features:
- Modern burnout furnaces are equipped with advanced features like rapid heating rates, up to 100 degrees Celsius per minute, which significantly reduce processing time.
- These furnaces often include precise temperature controls and programmable cycles to accommodate different materials and applications.
-
Applications:
- Dental Industry: Used for creating dental crowns, bridges, and other prosthetics. The burnout cycle ensures that wax patterns are completely removed before casting metal.
- Jewelry Industry: Essential for creating intricate jewelry pieces, where precision and cleanliness are critical.
- 3D Metal Printing: Used in heat treatment processes to prepare molds for metal printing.
-
Importance of Controlled Heating:
- Controlled heating rates and temperature holds are vital to prevent mold damage and ensure complete wax removal. Rapid heating can cause thermal shock, leading to cracks or defects in the mold.
- The ability to program specific heating profiles allows for customization based on the material and application, ensuring optimal results.
By understanding the burnout cycle and its stages, users can optimize their processes for better efficiency and higher-quality outcomes. Modern burnout furnaces, with their advanced features, play a crucial role in achieving these goals.
Summary Table:
Aspect | Details |
---|---|
Purpose | Removes wax or organic materials from investment molds for metal casting. |
Stages | 1. Initial Heating 2. Wax Elimination 3. Final Heating |
Equipment Features | Rapid heating (up to 100°C/min), precise controls, programmable cycles. |
Applications | Dental crowns, jewelry, 3D metal printing. |
Importance | Ensures mold cleanliness, prevents defects, and optimizes casting quality. |
Ready to enhance your metal casting process? Contact us today to learn more about burnout furnaces!