The cavity made from suitable refractory materials that can withstand high temperatures and into which molten metal can be poured is typically referred to as a crucible. Crucibles are essential in metallurgy, foundries, and laboratories for melting and holding molten metals. Among the various materials used for crucibles, zirconia crucibles are particularly notable for their exceptional thermal and chemical resistance, making them ideal for high-temperature applications. They are often used in environments where extreme durability and resistance to corrosion are required, such as in the handling of reactive metals or in high-temperature furnaces.
Key Points Explained:
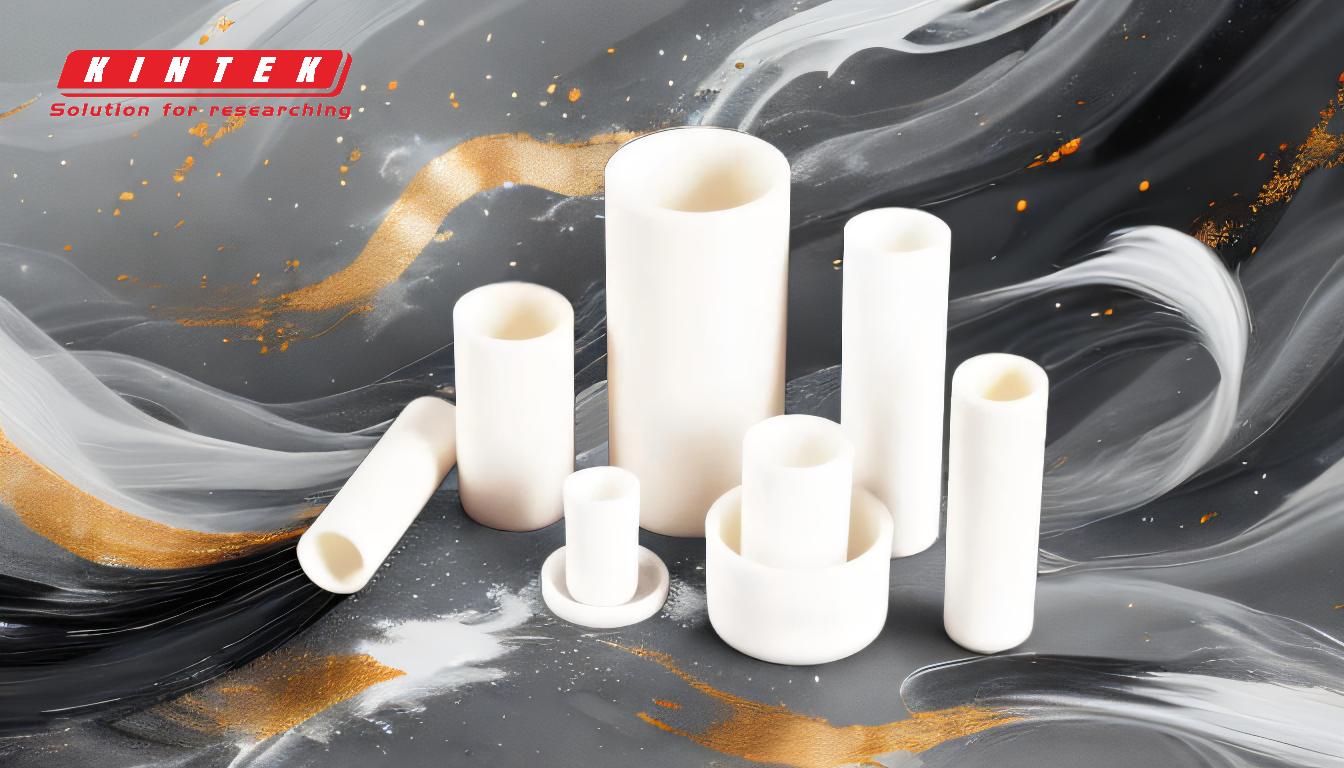
-
Definition and Purpose of a Crucible:
- A crucible is a container designed to withstand extremely high temperatures, used primarily for melting metals, alloys, and other materials. It acts as a cavity where materials are heated until they reach a molten state.
- Crucibles are critical in industries like metallurgy, foundries, and laboratories, where precise temperature control and material integrity are essential.
-
Refractory Materials for Crucibles:
- Refractory materials are chosen for their ability to resist high temperatures, thermal shock, and chemical corrosion. Common materials include graphite, silicon carbide, alumina, and zirconia.
- These materials are selected based on the specific application, temperature requirements, and the type of metal or material being melted.
-
Zirconia Crucibles:
- Zirconia crucibles are made from zirconium dioxide (ZrO₂), a material known for its exceptional thermal stability and resistance to chemical attack.
- They are particularly suitable for applications involving reactive metals, such as titanium and zirconium, or in environments with extreme temperatures, such as in a muffle furnace.
- Zirconia crucibles can withstand temperatures up to 2400°C, making them ideal for high-temperature processes.
-
Advantages of Zirconia Crucibles:
- High Thermal Resistance: Zirconia crucibles can endure extreme temperatures without degrading, ensuring long-term durability.
- Chemical Inertness: They are highly resistant to corrosion from molten metals and other reactive substances.
- Low Thermal Conductivity: This property minimizes heat loss and improves energy efficiency during melting processes.
- Mechanical Strength: Zirconia crucibles are robust and resistant to cracking under thermal stress.
-
Applications of Zirconia Crucibles:
- Metallurgy: Used for melting and casting high-purity metals and alloys, including those used in aerospace and medical industries.
- Laboratories: Ideal for high-temperature experiments and material testing.
- Foundries: Employed in the production of precision components and specialized alloys.
- High-Temperature Furnaces: Used in processes like sintering, annealing, and heat treatment.
-
Considerations for Choosing a Crucible:
- Temperature Requirements: Ensure the crucible material can withstand the maximum operating temperature.
- Chemical Compatibility: The crucible should resist corrosion from the molten material.
- Thermal Shock Resistance: The ability to withstand rapid temperature changes without cracking.
- Durability and Lifespan: Consider the expected usage and replacement frequency.
-
Maintenance and Handling of Zirconia Crucibles:
- Proper handling is crucial to prevent mechanical damage. Avoid dropping or striking the crucible.
- Clean the crucible regularly to remove residual materials that could affect performance.
- Store in a dry, contamination-free environment to maintain its integrity.
In summary, the cavity made from suitable refractory materials for high-temperature molten metal applications is a crucible, with zirconia crucibles being a top choice for their superior thermal and chemical resistance. These crucibles are indispensable in industries requiring precision, durability, and reliability in high-temperature processes.
Summary Table:
Key Feature | Description |
---|---|
Definition | A crucible is a high-temperature-resistant container for melting metals. |
Common Materials | Graphite, silicon carbide, alumina, zirconia. |
Zirconia Crucibles | Made from zirconium dioxide, resistant to 2400°C and chemical corrosion. |
Applications | Metallurgy, laboratories, foundries, high-temperature furnaces. |
Key Advantages | High thermal resistance, chemical inertness, low thermal conductivity. |
Need a durable crucible for your high-temperature processes? Contact us today to find the perfect solution!