Chemical vapor deposition (CVD) is a critical manufacturing process in microelectromechanical systems (MEMS) and other advanced technologies. It involves depositing thin films of material onto a substrate through chemical reactions in a controlled environment. The process occurs under vacuum conditions, where precursor gases are introduced, react on the substrate surface, and form a solid film. CVD is widely used in MEMS for creating precise, high-quality coatings that enhance performance, durability, and functionality. The process is highly controllable, enabling the production of uniform films with specific properties. However, it requires sophisticated equipment, operates at high temperatures, and can be time-consuming and costly, making it less suitable for large-scale production.
Key Points Explained:
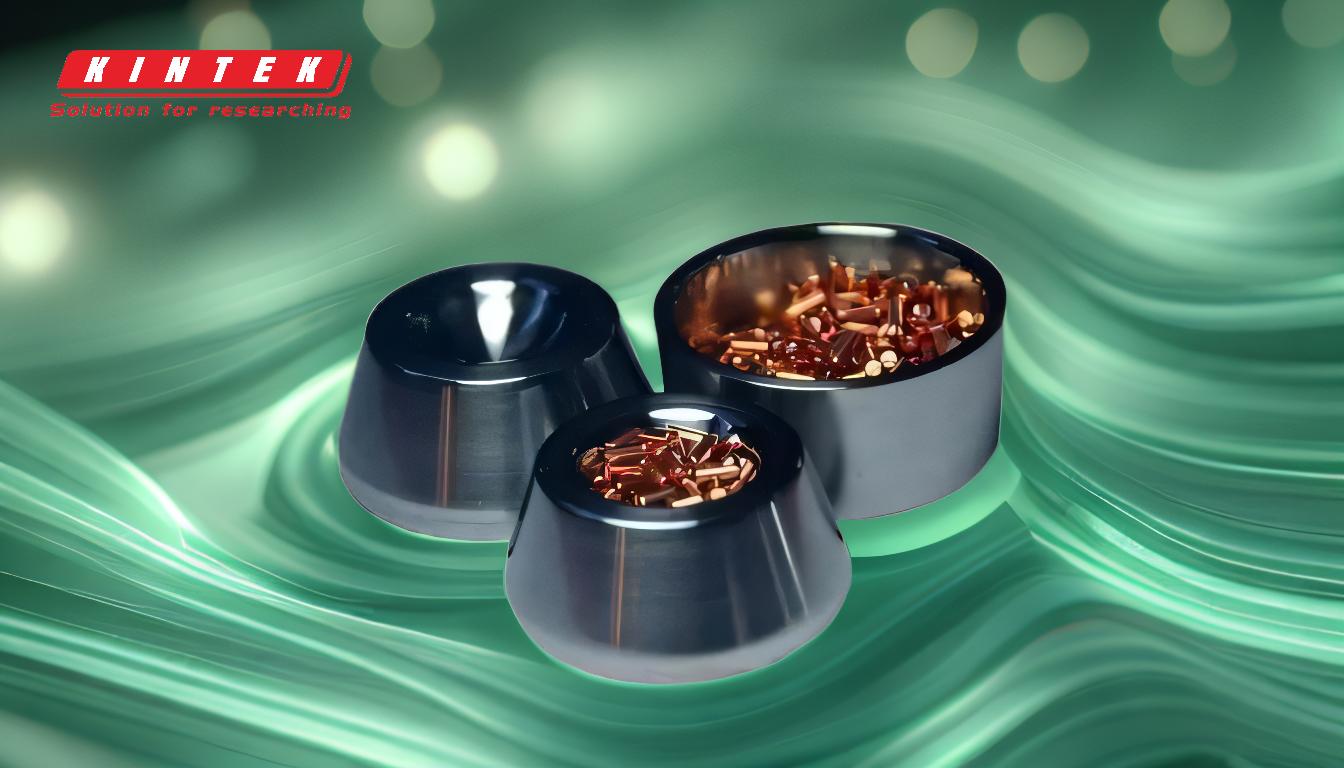
-
Definition and Purpose of CVD in MEMS:
- CVD is a vacuum-based manufacturing process used to deposit thin films of material onto a substrate.
- In MEMS, it is essential for creating precise coatings that improve device performance, such as enhancing conductivity, insulation, or mechanical strength.
-
Key Steps in the CVD Process:
- Transport of Precursor Gases: Precursor chemicals are introduced into the CVD reactor and transported to the substrate surface through fluid dynamics and diffusion.
- Adsorption on the Surface: The precursor molecules adhere to the substrate surface.
- Chemical Reaction: The adsorbed molecules undergo surface-catalyzed reactions, often facilitated by heat, to form a solid film.
- Nucleation and Growth: The reacted molecules form nuclei, which grow into a continuous thin film.
- Desorption of By-products: Gaseous by-products are desorbed from the surface and removed from the reactor to prevent contamination.
-
Environmental Conditions:
- CVD operates under vacuum or low-pressure conditions to ensure precise control over the deposition process.
- High temperatures (up to 1051°C or 1925°F) are often required to activate the chemical reactions.
-
Advantages of CVD in MEMS:
- High-Quality Films: Produces uniform, dense, and defect-free coatings.
- Precision: Enables precise control over film thickness and composition.
- Versatility: Can deposit a wide range of materials, including metals, semiconductors, and insulators.
- Environmental Friendliness: Some CVD processes, like the carbon coating example, are environmentally friendly and controllable.
-
Challenges and Limitations:
- High Costs: Requires sophisticated equipment and high-energy inputs, increasing production costs.
- Time-Consuming: Lower decomposition rates of precursors can lead to longer processing times.
- Scalability: Less suitable for large-scale production due to its complexity and cost.
- Material Limitations: Not all materials can be deposited using CVD, and some may require specialized precursors or conditions.
-
Applications in MEMS:
- Insulating Layers: CVD is used to deposit insulating materials like silicon dioxide (SiO₂) to isolate electrical components.
- Conductive Layers: Metals such as tungsten (W) or copper (Cu) are deposited to create interconnects and electrodes.
- Protective Coatings: CVD can create durable, wear-resistant coatings to protect MEMS devices from environmental damage.
- Functional Films: For example, carbon coatings on LiFePO₄ improve battery performance in MEMS-based energy storage systems.
-
Example of CVD in Action:
- A specific example involves the use of CVD to coat carbon on LiFePO₄. Solid glucose is heated in a quartz tube to 550°C, where it decomposes into vapor and condenses as small carbon clusters on the LiFePO₄ surface. This process enhances the material's rate capacity, cycling lifetime, and power density, demonstrating the utility of CVD in improving MEMS device performance.
-
Future Trends and Innovations:
- Low-Temperature CVD: Research is ongoing to develop CVD processes that operate at lower temperatures, reducing energy consumption and expanding the range of compatible substrates.
- Atomic Layer Deposition (ALD): A related technique that offers even greater precision by depositing materials one atomic layer at a time.
- Scalable CVD Systems: Efforts are being made to design CVD systems that are more cost-effective and suitable for large-scale production.
In summary, chemical vapor deposition is a foundational process in MEMS manufacturing, enabling the creation of high-performance thin films with precise control over their properties. While it offers significant advantages in terms of quality and versatility, challenges such as cost, time, and scalability must be addressed to fully realize its potential in large-scale applications.
Summary Table:
Aspect | Details |
---|---|
Purpose | Deposits thin films on substrates for MEMS performance enhancement. |
Key Steps | Transport, adsorption, reaction, nucleation, desorption. |
Environmental Conditions | Operates under vacuum, high temperatures (up to 1051°C). |
Advantages | High-quality, precise, versatile, environmentally friendly. |
Challenges | High costs, time-consuming, limited scalability, material restrictions. |
Applications | Insulating layers, conductive layers, protective coatings, functional films. |
Future Trends | Low-temperature CVD, ALD, scalable systems. |
Discover how CVD can elevate your MEMS manufacturing—contact our experts today!