An induction furnace is a specialized heating system used primarily for melting metals and creating precise alloys. Its operation is based on the principles of electromagnetic induction and the Joule effect, where an alternating current flowing through a coil generates a magnetic field. This field induces eddy currents in the conductive metal charge, producing heat through resistance. The furnace achieves high temperatures without direct contact between the heating element and the metal, ensuring efficient and clean melting. The process involves converting electrical energy into heat energy, making it ideal for applications requiring precise temperature control and rapid heating.
Key Points Explained:
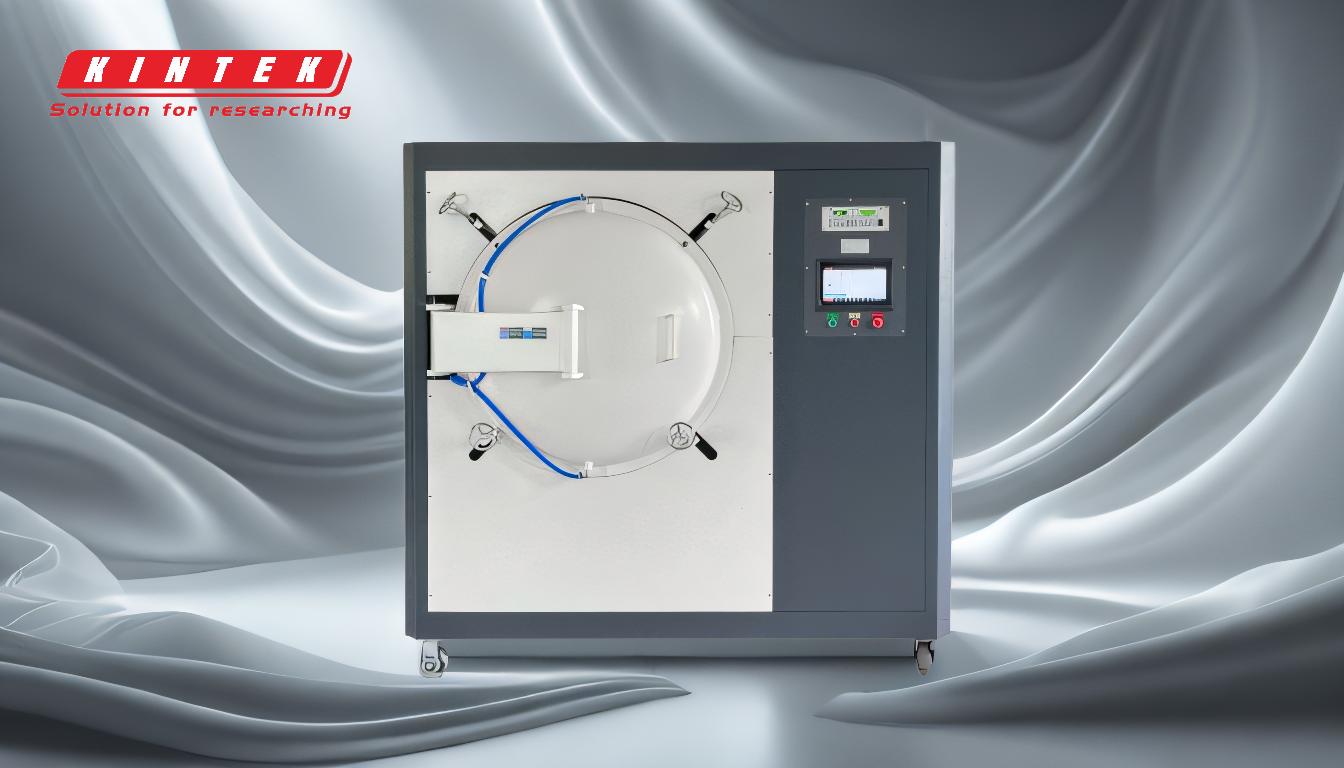
-
Principle of Induction Heating:
- Induction heating is a non-contact method that relies on electromagnetic induction and the Joule effect.
- An alternating current in a coil creates a magnetic field, which induces eddy currents in the conductive metal.
- The resistance of the metal to these eddy currents generates heat, melting the metal.
-
Components of an Induction Furnace:
- Induction Coil: A hollow copper coil surrounding the metal charge, carrying alternating current to generate the magnetic field.
- Power Supply Unit: Converts standard power frequency (50Hz) into medium frequency (300Hz to 1000Hz) for efficient heating.
- Capacitor and Inductor System: Works with the coil to create high-density magnetic lines, enhancing the induction process.
-
Working Mechanism:
- The power supply converts three-phase AC into DC, then into adjustable medium-frequency AC.
- This current flows through the capacitor and induction coil, generating a magnetic field.
- The magnetic field induces eddy currents in the metal, producing heat and melting it.
-
Advantages of Induction Furnaces:
- Efficiency: Heat is generated directly within the metal, minimizing energy loss.
- Precision: Allows for exact control over temperature and alloy composition.
- Cleanliness: No direct contact between the heating element and metal reduces contamination.
- Speed: Rapid heating and melting capabilities.
-
Applications:
- Ideal for melting metals like steel, iron, aluminum, and copper.
- Used in foundries for casting and alloy production.
- Suitable for applications requiring high purity and precise temperature control.
-
Cooling and Safety:
- The primary coils are water-cooled to prevent overheating.
- The furnace surfaces may become hot, but the heat is primarily generated within the metal charge.
By leveraging these principles and components, induction furnaces provide a reliable and efficient solution for industrial metal melting and alloy production.
Summary Table:
Key Aspect | Details |
---|---|
Principle | Electromagnetic induction and Joule effect generate heat in conductive metals. |
Components | Induction coil, power supply unit, capacitor, and inductor system. |
Working Mechanism | Converts AC to DC, then to medium-frequency AC to induce eddy currents. |
Advantages | High efficiency, precise temperature control, cleanliness, and rapid heating. |
Applications | Melting steel, iron, aluminum, and copper; foundry casting and alloy production. |
Cooling & Safety | Water-cooled coils prevent overheating; heat is primarily within the metal. |
Discover how an induction furnace can revolutionize your metal melting process—contact us today for expert advice!