Vacuum furnaces and atmosphere furnaces are both specialized heating devices used in industrial and laboratory settings, but they differ significantly in their operating environments, mechanisms, and applications. A vacuum furnace operates by removing air from the heating chamber to create a vacuum, which prevents oxidation and contamination during heating. In contrast, an atmosphere furnace introduces specific gases or gas mixtures to create a controlled environment, protecting materials from undesirable reactions like oxidation or decarburization. The choice between these furnaces depends on the specific requirements of the process, such as the need for a completely oxygen-free environment (vacuum furnace) or a controlled gas atmosphere (atmosphere furnace).
Key Points Explained:
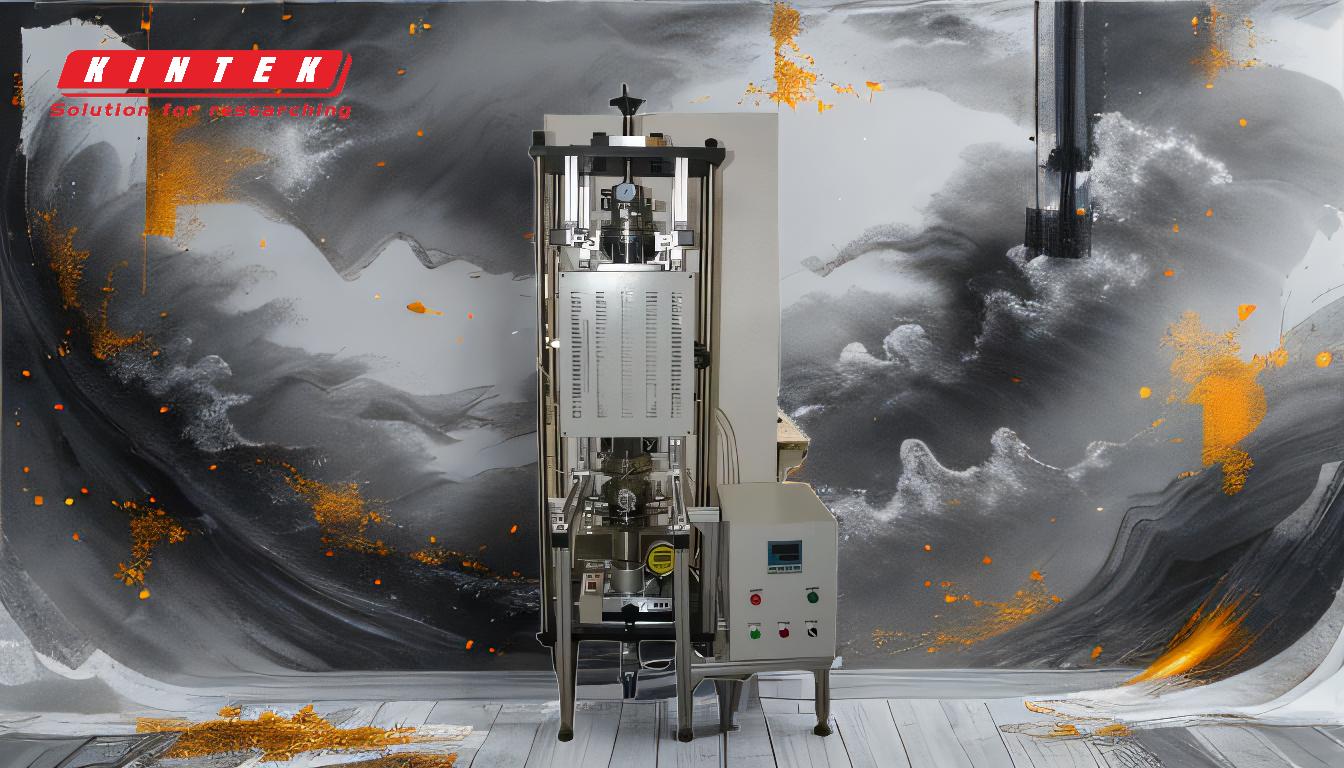
-
Operating Environment:
- Vacuum Furnace: Operates in a vacuum, meaning the heating chamber is devoid of air and other gases. This is achieved using vacuum pumps that remove air and create a sealed environment. The absence of oxygen prevents oxidation, making it ideal for processes requiring high purity, such as in aerospace or semiconductor manufacturing.
- Atmosphere Furnace: Operates in a controlled atmosphere, where specific gases (e.g., nitrogen, hydrogen, argon) are introduced to create a protective environment. This prevents oxidation, decarburization, or other reactions that could degrade the material being processed.
-
Mechanism of Operation:
- Vacuum Furnace: Uses an air purging pump to remove air and create a vacuum. The sealed chamber ensures no oxygen enters during the heating process. This is particularly useful for materials sensitive to oxidation or contamination.
- Atmosphere Furnace: Relies on gas injection systems to introduce and maintain a specific gas mixture. The atmosphere is carefully controlled to achieve the desired chemical reactions or to protect the material from unwanted reactions.
-
Applications:
- Vacuum Furnace: Commonly used in industries requiring high-purity materials, such as aerospace, medical devices, and electronics. It is also used for processes like brazing, sintering, and annealing where oxidation must be avoided.
- Atmosphere Furnace: Suitable for processes like carburizing, nitriding, and annealing, where a specific gas environment is needed to achieve the desired material properties. It is widely used in metalworking, ceramics, and glass industries.
-
Temperature Capabilities:
- Vacuum Furnace: Electric vacuum furnaces can operate at temperatures up to 2,400°F, making them suitable for high-temperature applications. Gas vacuum furnaces, introduced in the 1980s, are limited to about 1,950°F but offer lower operating costs and faster cycle times.
- Atmosphere Furnace: Temperature capabilities vary depending on the design and gas used, but they generally operate within a range suitable for processes like heat treatment, sintering, and brazing.
-
Advantages and Limitations:
- Vacuum Furnace: Offers superior protection against oxidation and contamination, making it ideal for high-purity applications. However, it can be more expensive to operate and maintain due to the need for vacuum pumps and seals.
- Atmosphere Furnace: Provides flexibility in creating specific gas environments, which is useful for a wide range of industrial processes. However, it may not be suitable for applications requiring a completely oxygen-free environment.
-
Cost and Maintenance:
- Vacuum Furnace: Generally has higher initial and operating costs due to the complexity of the vacuum system. Maintenance can also be more demanding, requiring regular checks on vacuum pumps and seals.
- Atmosphere Furnace: Typically has lower initial costs and operating expenses compared to vacuum furnaces. However, the cost of gases and the need for precise gas control systems can add to the overall expense.
In summary, the choice between a vacuum furnace and an atmosphere furnace depends on the specific requirements of the process, including the need for oxidation prevention, temperature range, and cost considerations. Both types of furnaces offer unique advantages and are essential tools in various industrial and laboratory applications.
Summary Table:
Aspect | Vacuum Furnace | Atmosphere Furnace |
---|---|---|
Operating Environment | Operates in a vacuum, preventing oxidation and contamination. | Uses specific gases to create a controlled, protective environment. |
Mechanism | Air purging pump removes air to create a vacuum. | Gas injection systems introduce and maintain a specific gas mixture. |
Applications | High-purity processes (e.g., aerospace, medical devices, electronics). | Processes requiring controlled gas environments (e.g., carburizing, nitriding). |
Temperature Range | Up to 2,400°F (electric) or 1,950°F (gas). | Varies based on design and gas used, suitable for heat treatment and sintering. |
Advantages | Superior oxidation prevention, ideal for high-purity applications. | Flexible gas environments, cost-effective for specific processes. |
Limitations | Higher initial and operating costs, complex maintenance. | Not suitable for completely oxygen-free environments. |
Need help choosing the right furnace for your application? Contact our experts today for personalized guidance!