Calcining and roasting are both thermal processes used in metallurgy and material processing, but they differ in their purpose, chemical reactions, and the types of ores they are applied to. Roasting involves heating sulfide ores below their melting point in the presence of air or oxygen, primarily to convert sulfides into oxides and remove volatile impurities. Calcination, on the other hand, focuses on the thermal decomposition of carbonate ores, driving out moisture and volatile substances like carbon dioxide. While roasting is commonly used for sulfide minerals, calcination is applied to carbonates and hydrated ores. The key distinction lies in the chemical changes: roasting involves oxidation, whereas calcination involves decomposition.
Key Points Explained:
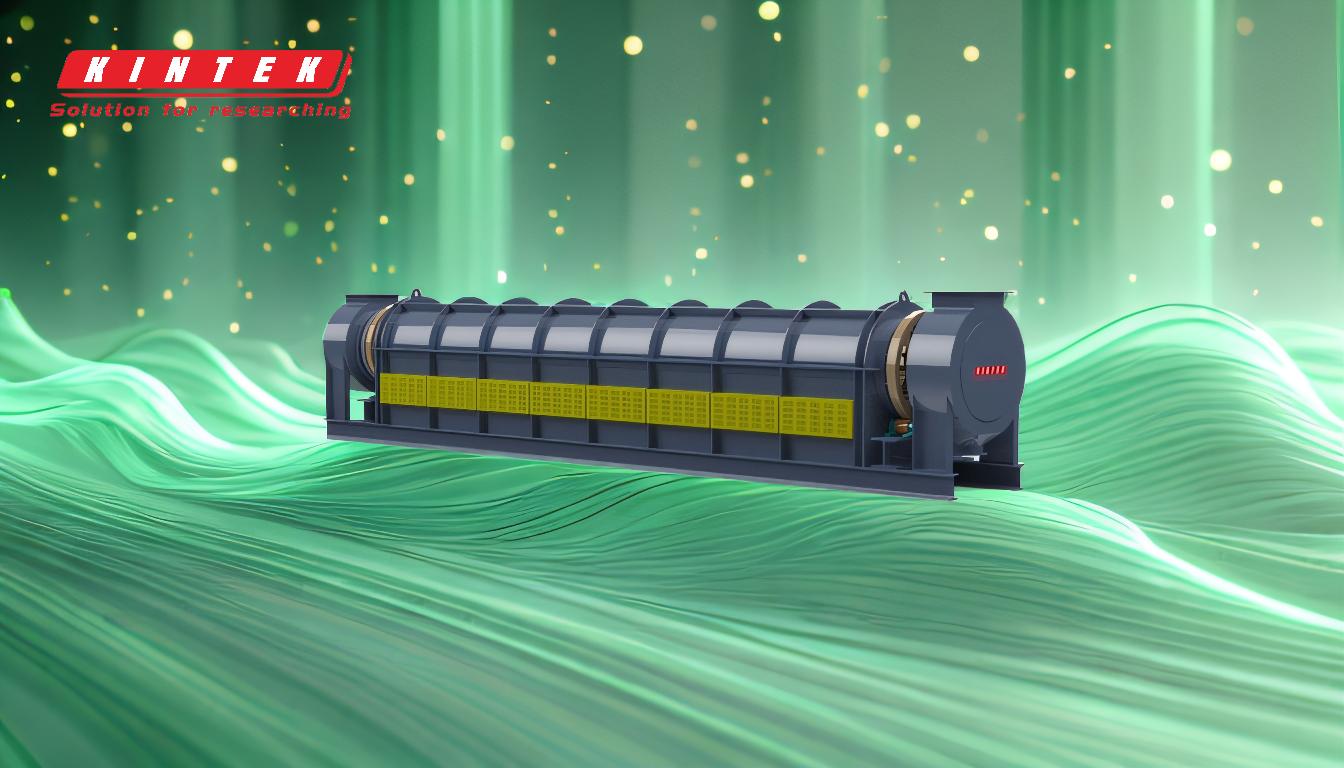
-
Definition and Purpose:
- Roasting: This process involves heating sulfide ores below their melting point in the presence of air or oxygen. Its primary purpose is to convert sulfide minerals into oxides and remove volatile impurities like sulfur dioxide.
- Calcination: This process involves heating carbonate or hydrated ores to high temperatures in the absence or limited supply of air. Its purpose is to drive out moisture, carbon dioxide, or other volatile substances, resulting in the decomposition of the ore.
-
Types of Ores Treated:
- Roasting: Primarily used for sulfide ores, such as zinc sulfide (ZnS) or lead sulfide (PbS). These ores are oxidized to form metal oxides and sulfur dioxide gas.
- Calcination: Applied to carbonate ores, such as limestone (CaCO₃) or hydrated ores like bauxite (Al₂O₃·2H₂O). The process decomposes these ores into simpler compounds.
-
Chemical Reactions:
-
Roasting: Involves oxidation reactions. For example, zinc sulfide (ZnS) is roasted to form zinc oxide (ZnO) and sulfur dioxide (SO₂):
2ZnS + 3O₂ → 2ZnO + 2SO₂
-
Calcination: Involves decomposition reactions. For example, limestone (CaCO₃) decomposes into calcium oxide (CaO) and carbon dioxide (CO₂):
CaCO₃ → CaO + CO₂
-
Roasting: Involves oxidation reactions. For example, zinc sulfide (ZnS) is roasted to form zinc oxide (ZnO) and sulfur dioxide (SO₂):
-
Temperature and Atmosphere:
- Roasting: Typically performed at temperatures below the melting point of the ore, often in the range of 500–700°C, in the presence of excess air or oxygen.
- Calcination: Conducted at higher temperatures, usually between 800–1200°C, in the absence or limited supply of air to prevent oxidation.
-
Products and Applications:
- Roasting: Produces metal oxides and gases like sulfur dioxide. The oxides are then further processed to extract metals. Roasting is widely used in the extraction of metals like zinc, copper, and lead.
- Calcination: Produces metal oxides or anhydrous compounds. The products are used in various industries, such as cement production (from limestone) or alumina extraction (from bauxite).
-
Environmental Impact:
- Roasting: Releases sulfur dioxide (SO₂), which can contribute to air pollution and acid rain if not properly managed. Modern roasting processes often include gas capture systems to mitigate environmental impact.
- Calcination: Releases carbon dioxide (CO₂), a greenhouse gas. However, the process is generally less polluting compared to roasting, as it does not produce harmful sulfur compounds.
-
Equipment Used:
- Roasting: Typically carried out in specialized furnaces like reverberatory furnaces, fluidized bed reactors, or multiple hearth roasters, which are designed to handle sulfide ores and manage gas emissions.
- Calcination: Often performed in rotary kilns or shaft kilns, which are designed to handle high temperatures and ensure uniform heating of carbonate or hydrated ores.
In summary, while both calcining and roasting are thermal processes used in ore processing, they differ significantly in their chemical mechanisms, the types of ores they treat, and their environmental and industrial applications. Understanding these differences is crucial for selecting the appropriate process for a given material and achieving desired outcomes in metallurgical and industrial operations.
Summary Table:
Aspect | Roasting | Calcination |
---|---|---|
Purpose | Converts sulfide ores into oxides; removes volatile impurities like SO₂. | Decomposes carbonate/hydrated ores; drives out moisture and CO₂. |
Ores Treated | Sulfide ores (e.g., ZnS, PbS). | Carbonate/hydrated ores (e.g., CaCO₃, Al₂O₃·2H₂O). |
Chemical Reaction | Oxidation (e.g., 2ZnS + 3O₂ → 2ZnO + 2SO₂). | Decomposition (e.g., CaCO₃ → CaO + CO₂). |
Temperature | 500–700°C in the presence of air/oxygen. | 800–1200°C in the absence/limited air supply. |
Applications | Metal extraction (e.g., zinc, copper, lead). | Cement production, alumina extraction. |
Environmental Impact | Releases SO₂, contributing to air pollution. | Releases CO₂, a greenhouse gas, but less harmful than SO₂. |
Equipment | Reverberatory furnaces, fluidized bed reactors. | Rotary kilns, shaft kilns. |
Need help choosing the right thermal process for your materials? Contact our experts today for tailored solutions!