CVD (Chemical Vapor Deposition) and PVD (Physical Vapor Deposition) are two widely used techniques for depositing thin films onto substrates, each with distinct processes, advantages, and limitations. CVD relies on chemical reactions between gaseous precursors and the substrate, enabling the deposition of uniform and dense coatings on complex geometries. It operates at higher temperatures and is ideal for applications requiring thick, high-quality films. PVD, on the other hand, involves the physical vaporization of solid materials in a vacuum, which then condense onto the substrate. It operates at lower temperatures and is better suited for depositing thin, smooth, and durable coatings. The choice between CVD and PVD depends on factors such as the desired film properties, substrate material, and application requirements.
Key Points Explained:
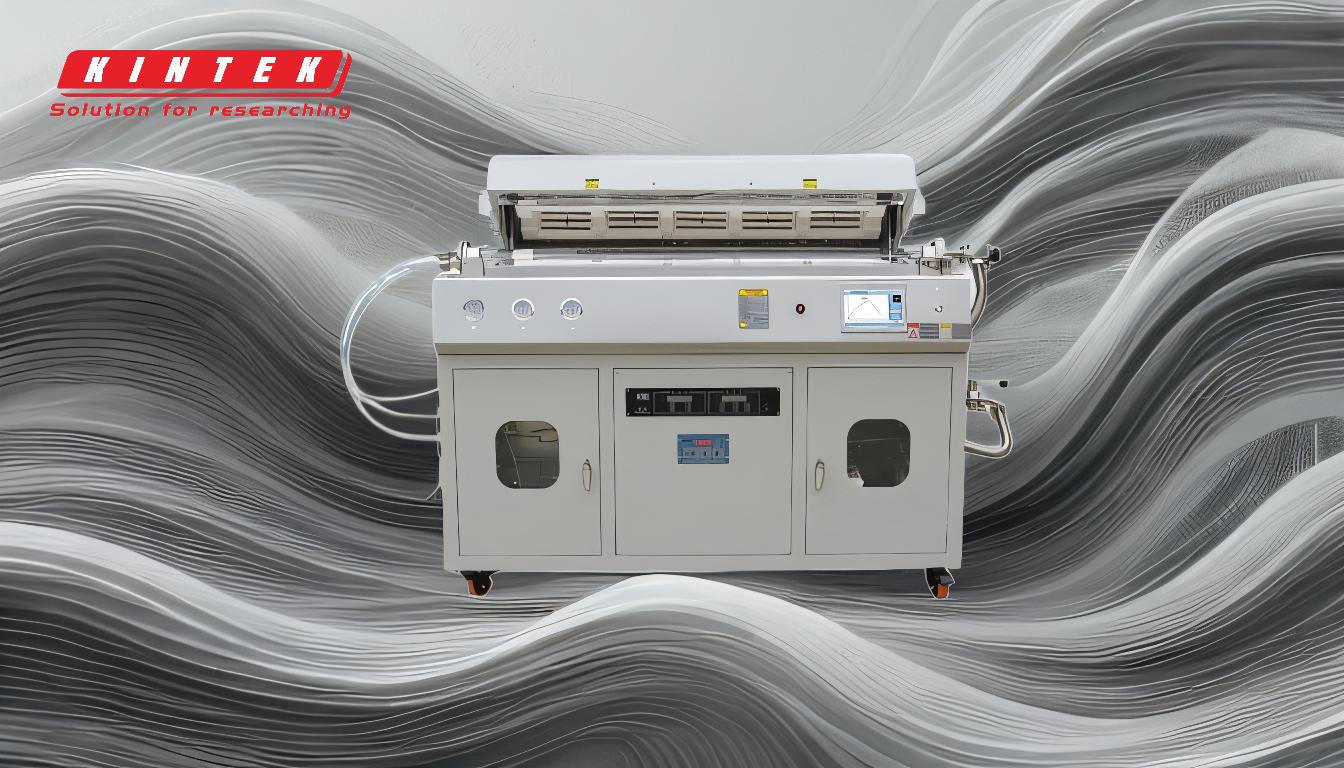
-
Working Mechanism:
- CVD: Involves chemical reactions between gaseous precursors and the substrate to form a solid coating. This process is multidirectional, allowing for uniform coverage of complex shapes and deep recesses.
- PVD: Relies on the physical vaporization of solid materials, which are then transported and condensed onto the substrate. This process is line-of-sight, meaning it deposits material directly onto exposed surfaces.
-
Operating Temperatures:
- CVD: Typically operates at higher temperatures (450°C to 1050°C), which can limit its use with temperature-sensitive substrates.
- PVD: Operates at lower temperatures (250°C to 450°C), making it suitable for substrates that cannot withstand high heat.
-
Coating Substance Nature:
- CVD: Primarily deposits ceramics and polymers, often resulting in dense and uniform coatings.
- PVD: Can deposit a broader range of materials, including metals, alloys, and ceramics, but the coatings are generally less dense and uniform compared to CVD.
-
Coating Coverage Area:
- CVD: Offers excellent throwing power, enabling the coating of complex geometries, holes, and deep recesses.
- PVD: Limited to line-of-sight deposition, making it less effective for coating intricate shapes or hidden areas.
-
Film Thickness and Smoothness:
- CVD: Produces thicker coatings that may be rougher due to the chemical reaction process.
- PVD: Produces thinner, smoother, and more durable coatings, ideal for applications requiring precision and surface finish.
-
Deposition Rates:
- CVD: Generally has higher deposition rates, making it more economical for producing thick coatings.
- PVD: Typically has lower deposition rates but offers faster application times for thin coatings.
-
Applications:
- CVD: Commonly used in industries requiring high-quality, uniform coatings, such as semiconductor manufacturing, optics, and wear-resistant applications.
- PVD: Preferred for applications requiring smooth, durable, and temperature-sensitive coatings, such as decorative finishes, cutting tools, and medical devices.
-
Material Utilization Efficiency:
- CVD: May produce corrosive gaseous byproducts and leave impurities in the film, reducing material efficiency.
- PVD: Does not produce corrosive byproducts and offers high material utilization efficiency, especially in techniques like EBPVD (Electron Beam Physical Vapor Deposition).
By understanding these key differences, equipment and consumable purchasers can make informed decisions based on the specific requirements of their applications, such as desired film properties, substrate compatibility, and operational constraints.
Summary Table:
Aspect | CVD | PVD |
---|---|---|
Working Mechanism | Chemical reactions between gaseous precursors and substrate | Physical vaporization of solid materials in a vacuum |
Operating Temperatures | Higher (450°C to 1050°C) | Lower (250°C to 450°C) |
Coating Substance Nature | Primarily ceramics and polymers; dense and uniform | Metals, alloys, ceramics; less dense and uniform |
Coating Coverage Area | Excellent for complex geometries and deep recesses | Limited to line-of-sight deposition |
Film Thickness/Smoothness | Thicker, rougher coatings | Thinner, smoother, and more durable coatings |
Deposition Rates | Higher rates for thick coatings | Lower rates but faster for thin coatings |
Applications | Semiconductor manufacturing, optics, wear-resistant applications | Decorative finishes, cutting tools, medical devices |
Material Efficiency | May produce corrosive byproducts; lower efficiency | No corrosive byproducts; high efficiency |
Need help choosing between CVD and PVD for your application? Contact our experts today!