Electroplating and Physical Vapor Deposition (PVD) are two distinct surface coating techniques used to enhance the properties of materials, such as corrosion resistance, hardness, and aesthetic appeal. Electroplating involves the electrochemical deposition of a metal layer onto a substrate using an electrolyte solution, while PVD uses physical processes like evaporation or sputtering to deposit thin films in a vacuum environment. PVD offers advantages such as higher corrosion resistance, better adhesion, and environmental safety, as it does not rely on toxic chemicals. Electroplating, on the other hand, is often more cost-effective and suitable for thicker coatings but may involve hazardous chemicals and produce less durable finishes.
Key Points Explained:
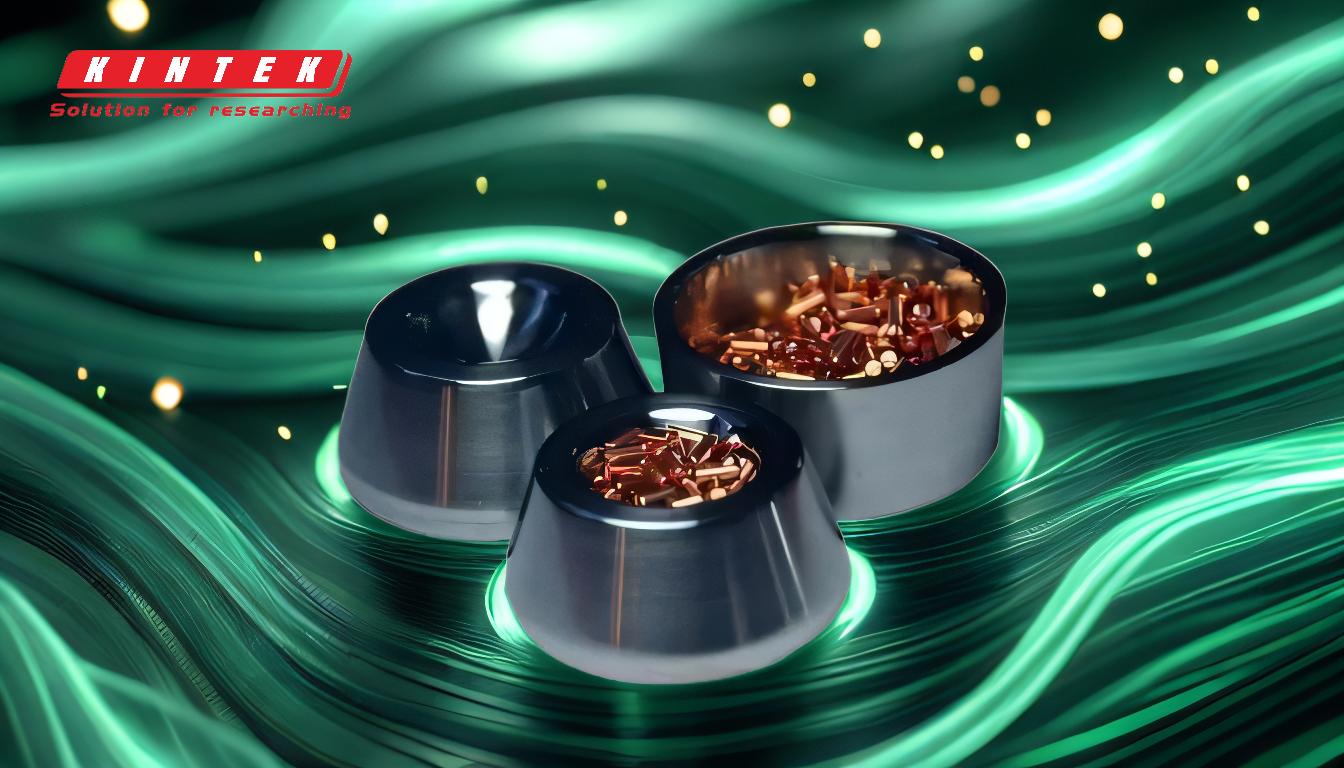
-
Process Mechanism:
- Electroplating: This is an electrochemical process where a metal ion solution (electrolyte) is used to deposit a metal layer onto a substrate. An electric current reduces the metal ions in the electrolyte, causing them to bond to the substrate.
- PVD: PVD is a physical process that involves vaporizing a solid material (target) in a vacuum chamber. The vaporized atoms or molecules then condense on the substrate to form a thin, uniform coating. Techniques like sputtering and evaporation are commonly used.
-
Coating Thickness and Uniformity:
- Electroplating: Typically produces thicker coatings, which can range from a few micrometers to several millimeters. However, achieving uniform thickness, especially on complex geometries, can be challenging.
- PVD: Creates much thinner coatings, often in the nanometer to micrometer range. PVD coatings are highly uniform and can conform to complex shapes due to the line-of-sight deposition process.
-
Adhesion and Durability:
- Electroplating: The adhesion of electroplated coatings depends on the surface preparation and the electrochemical conditions. While durable, these coatings may be prone to peeling or flaking under stress.
- PVD: Offers superior adhesion due to the atomic-level bonding between the coating and the substrate. PVD coatings are highly durable and resistant to wear, corrosion, and oxidation.
-
Environmental and Safety Considerations:
- Electroplating: Often involves the use of hazardous chemicals, such as cyanides and acids, which require careful handling and disposal. The process can generate toxic waste and pose environmental risks.
- PVD: Generally considered safer and more environmentally friendly, as it does not involve toxic chemicals. The process is conducted in a vacuum, minimizing exposure to hazardous substances.
-
Applications:
- Electroplating: Commonly used in industries requiring thick, decorative, or functional coatings, such as automotive (chrome plating), electronics (gold plating), and jewelry.
- PVD: Preferred for applications requiring high-performance coatings, such as cutting tools, medical devices, and aerospace components, where durability, corrosion resistance, and precision are critical.
-
Cost and Scalability:
- Electroplating: Generally more cost-effective for large-scale production and thicker coatings. It is widely used in mass production due to its relatively low cost and high throughput.
- PVD: More expensive due to the need for vacuum equipment and specialized processes. However, it is highly scalable for precision applications and offers long-term cost benefits due to the durability of the coatings.
-
Material Compatibility:
- Electroplating: Limited to metals that can be electrochemically deposited. Non-conductive substrates require conductive pretreatment.
- PVD: Can deposit a wide range of materials, including metals, ceramics, and composites, on both conductive and non-conductive substrates.
-
Surface Finish and Aesthetics:
- Electroplating: Provides a shiny, reflective finish, making it ideal for decorative applications. However, the finish may degrade over time due to environmental exposure.
- PVD: Offers a matte or satin finish, which can be tailored for specific aesthetic requirements. PVD coatings are more resistant to fading and tarnishing.
By understanding these key differences, purchasers can make informed decisions based on the specific requirements of their application, such as durability, environmental impact, and cost considerations.
Summary Table:
Aspect | Electroplating | PVD |
---|---|---|
Process Mechanism | Electrochemical deposition using an electrolyte solution. | Physical vaporization in a vacuum environment. |
Coating Thickness | Thicker coatings (micrometers to millimeters). | Thinner coatings (nanometers to micrometers). |
Adhesion & Durability | Durable but may peel or flake under stress. | Superior adhesion, highly durable, and resistant to wear and corrosion. |
Environmental Impact | Uses hazardous chemicals; generates toxic waste. | Environmentally friendly; no toxic chemicals used. |
Applications | Automotive, electronics, jewelry (thick, decorative coatings). | Cutting tools, medical devices, aerospace (high-performance coatings). |
Cost | Cost-effective for large-scale production. | Higher initial cost but long-term durability benefits. |
Material Compatibility | Limited to metals; non-conductive substrates require pretreatment. | Compatible with metals, ceramics, and composites. |
Surface Finish | Shiny, reflective finish; may degrade over time. | Matte or satin finish; resistant to fading and tarnishing. |
Still unsure which coating technique is right for your project? Contact our experts today for personalized advice!