Hardening, quenching, and tempering are heat treatment processes used to enhance the mechanical properties of metals, particularly steels. Hardening involves heating the metal to a high temperature (above 900°C) and then rapidly cooling it, typically through quenching, to increase strength and wear resistance. Quenching is the rapid cooling process itself, often done using oil or water. Tempering follows hardening and involves reheating the metal to a lower temperature and then cooling it slowly. This process reduces brittleness, introduces ductility, and balances hardness with toughness. These processes are critical in industries requiring high-performance materials, such as steel manufacturing, automotive, and aerospace.
Key Points Explained:
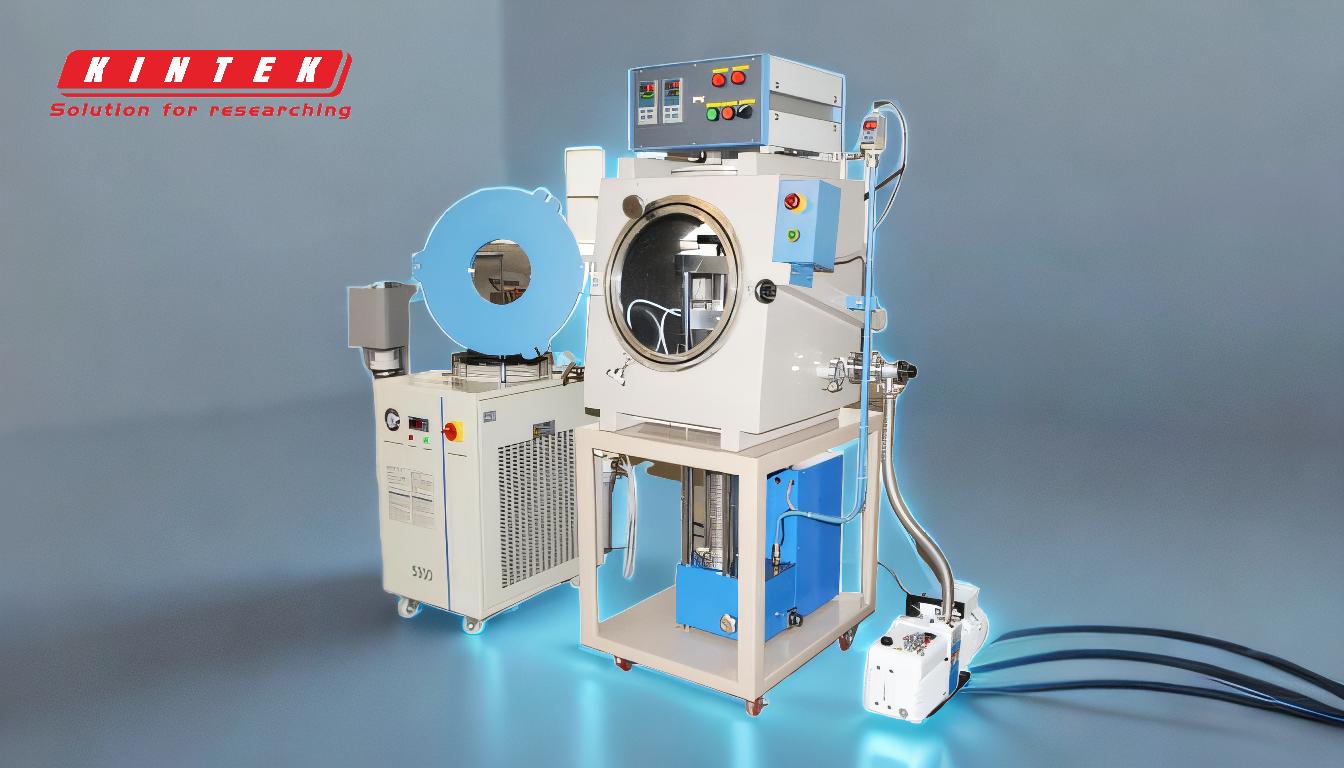
-
Hardening:
- Process: Heating the metal to a temperature above its critical transformation range (typically 900°C–1000°C) and then rapidly cooling it.
- Purpose: Increases the material's strength and wear resistance by forming a hard, brittle martensitic structure.
- Applications: Used in components like gears, shafts, and tools that require high hardness and resistance to wear.
-
Quenching:
- Process: Rapid cooling of the heated metal, often using mediums like oil, water, or air.
- Purpose: Locks the metal in a hard, martensitic state achieved during hardening.
- Challenges: Can introduce internal stresses and brittleness, which are addressed in the tempering process.
-
Tempering:
- Process: Reheating the hardened metal to a temperature below its critical transformation range (typically 150°C–650°C) and then cooling it slowly.
- Purpose: Reduces brittleness, improves toughness, and balances hardness with ductility.
- Outcome: Results in a material that is strong yet less prone to cracking under stress.
-
Comparison of Hardening and Tempering:
- Hardening: Focuses on achieving maximum hardness and wear resistance but often results in a brittle material.
- Tempering: Balances hardness with toughness, making the material more durable and less likely to fail under pressure.
-
Industrial Applications:
- Steel Pipe Manufacturing: Hardening and tempering are used to produce pipes that can withstand high pressure and wear.
- Automotive and Aerospace: Critical components like gears, crankshafts, and landing gear are treated to ensure strength and durability.
-
Heating Methods:
- Electric Resistance Furnaces: Commonly used for uniform heating during hardening and tempering.
- Induction Heating: Effective for surface hardening, where only the outer layer of the material needs to be hardened.
- Laser and Plasma Heating: Limited to specialized applications due to their precision and cost.
By understanding the differences and complementary roles of hardening, quenching, and tempering, manufacturers can tailor the properties of metals to meet specific performance requirements, ensuring reliability and longevity in demanding applications.
Summary Table:
Process | Temperature Range | Purpose | Outcome |
---|---|---|---|
Hardening | 900°C–1000°C | Increases strength and wear resistance by forming a hard, brittle structure | High hardness but increased brittleness |
Quenching | Rapid cooling | Locks the metal in a hard, martensitic state | Introduces internal stresses and brittleness |
Tempering | 150°C–650°C | Reduces brittleness, improves toughness, and balances hardness with ductility | Strong, durable material less prone to cracking under stress |
Need tailored heat treatment solutions for your materials? Contact our experts today to get started!