Induction brazing and furnace brazing are two widely used methods for joining materials, each with distinct advantages and disadvantages. Induction brazing uses electromagnetic induction to generate heat directly within the workpiece, making it highly localized and energy-efficient. It is ideal for small to medium-sized components and offers rapid heating cycles. Furnace brazing, on the other hand, involves heating the entire assembly in a controlled environment, making it suitable for mass production and complex assemblies. It provides uniform heating, minimal distortion, and the ability to join dissimilar materials. The choice between the two depends on factors such as production volume, component size, material compatibility, and desired joint quality.
Key Points Explained:
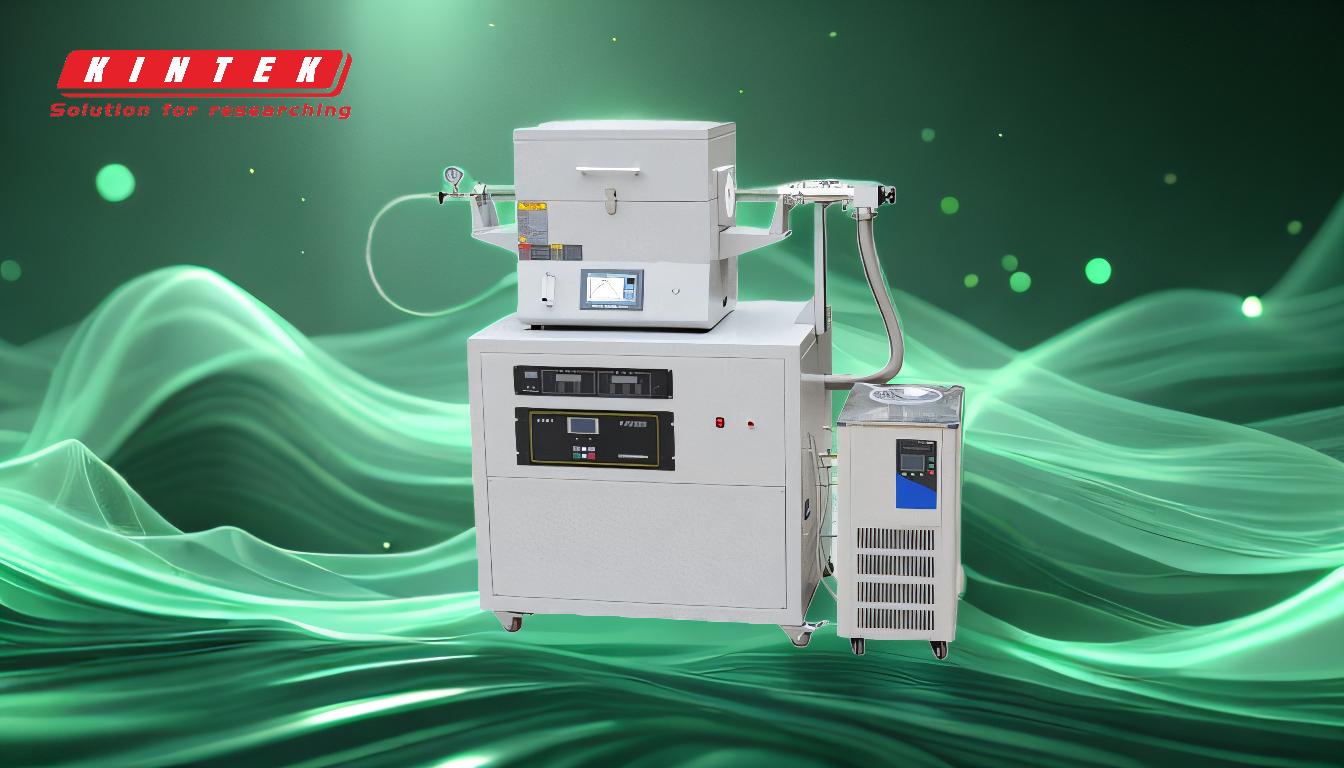
-
Heat Generation and Localization:
- Induction Brazing: Heat is generated directly within the workpiece using electromagnetic induction. This method is highly localized, allowing for precise heating of specific areas without affecting the entire component. It is particularly useful for small to medium-sized parts and applications requiring rapid heating cycles.
- Furnace Brazing: Heat is applied uniformly to the entire assembly in a controlled environment, such as a vacuum or inert gas atmosphere. This ensures consistent temperature distribution, making it ideal for complex assemblies and mass production.
-
Material Compatibility:
- Induction Brazing: Best suited for materials that can be efficiently heated by induction, such as metals with good electrical conductivity. It is less effective for materials with low conductivity or complex geometries.
- Furnace Brazing: Capable of joining dissimilar materials, including metals with different melting points. The controlled environment minimizes oxidation and contamination, making it suitable for high-precision assemblies.
-
Production Volume and Automation:
- Induction Brazing: Ideal for low to medium production volumes due to its localized heating and rapid cycles. It can be automated but is generally more suited for smaller-scale operations.
- Furnace Brazing: Well-suited for mass production and can be easily automated. The ability to process multiple components simultaneously makes it cost-effective for high-volume manufacturing.
-
Joint Quality and Mechanical Properties:
- Induction Brazing: Produces strong, clean joints with minimal oxidation. However, the localized heating may result in uneven stress distribution, potentially affecting joint integrity in some cases.
- Furnace Brazing: Offers high-quality joints with minimal voids and excellent mechanical properties. The uniform heating and controlled environment reduce residual stress and distortion, ensuring consistent joint quality.
-
Environmental and Operational Considerations:
- Induction Brazing: Energy-efficient and environmentally friendly due to localized heating and minimal waste generation. However, it may require skilled operators to achieve optimal results.
- Furnace Brazing: Produces clean parts without the need for secondary finishing. The process is environmentally friendly, with minimal waste generation and no need for flux, which eliminates potential contamination.
-
Cost and Lead Time:
- Induction Brazing: Generally more cost-effective for small-scale production due to lower energy consumption and faster heating cycles. However, it may require higher initial investment in equipment and skilled labor.
- Furnace Brazing: Offers better cost-effectiveness for high-volume production due to lower operator skill requirements and faster lead times. The ability to combine heat treatments with brazing further reduces overall production costs.
-
Applications and Suitability:
- Induction Brazing: Suitable for applications requiring precise, localized heating, such as in the automotive, aerospace, and electronics industries. It is also ideal for components with complex geometries that are difficult to heat uniformly.
- Furnace Brazing: Ideal for high-precision assemblies, complex components, and mass production. It is widely used in industries such as automotive, aerospace, and medical devices, where consistent joint quality and minimal distortion are critical.
In summary, the choice between induction brazing and furnace brazing depends on the specific requirements of the application, including production volume, component size, material compatibility, and desired joint quality. Induction brazing offers localized, rapid heating suitable for small to medium-sized components, while furnace brazing provides uniform heating and is ideal for mass production and complex assemblies. For more information on related equipment, you can explore the igbt induction furnace.
Summary Table:
Aspect | Induction Brazing | Furnace Brazing |
---|---|---|
Heat Generation | Localized heating via electromagnetic induction | Uniform heating in a controlled environment |
Material Compatibility | Best for conductive metals; less effective for low conductivity or complex geometries | Suitable for dissimilar materials and high-precision assemblies |
Production Volume | Ideal for low to medium volumes | Best for mass production and automation |
Joint Quality | Strong, clean joints with minimal oxidation | High-quality joints with minimal voids and excellent mechanical properties |
Environmental Impact | Energy-efficient with minimal waste | Environmentally friendly with no need for flux or secondary finishing |
Cost | Cost-effective for small-scale production | Economical for high-volume production |
Applications | Automotive, aerospace, electronics | Automotive, aerospace, medical devices |
Need help choosing the right brazing method for your project? Contact our experts today for personalized advice!