Rolling and bending are two distinct metal forming processes used in manufacturing, each with its own techniques, applications, and outcomes. Rolling involves passing metal through rollers to reduce thickness or alter its shape, while bending focuses on deforming metal along a specific axis to create angles or curves. Understanding the differences between these processes is crucial for selecting the appropriate method for a given application, as they vary in terms of equipment, precision, and material suitability.
Key Points Explained:
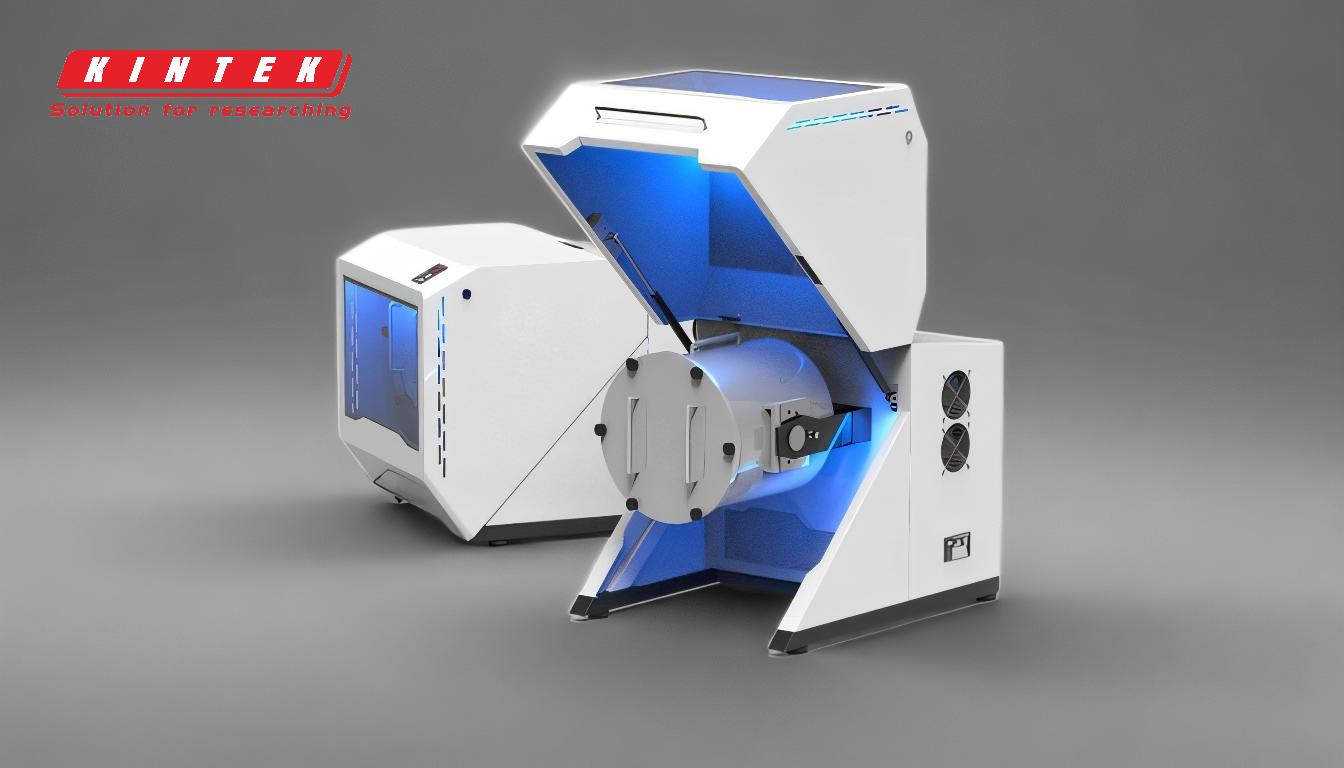
-
Definition and Process:
- Rolling: Rolling is a metalworking process where metal is passed through one or more pairs of rollers to reduce thickness, create uniform cross-sections, or produce specific shapes like sheets, plates, or structural beams. It can be performed at high temperatures (hot rolling) or at room temperature (cold rolling), depending on the material and desired outcome.
- Bending: Bending involves applying force to a metal workpiece to deform it along a specific axis, creating angles or curves. This is typically done using press brakes, roll benders, or other specialized tools. Bending is often used to create components like brackets, frames, or enclosures.
-
Equipment Used:
- Rolling: Rolling requires heavy machinery such as rolling mills, which consist of large, powered rollers. These machines are designed to handle significant forces and are often used in large-scale industrial settings.
- Bending: Bending is typically performed using press brakes, which use a punch and die to apply force, or roll benders, which use three rollers to gradually curve the metal. These tools are more compact and versatile compared to rolling mills.
-
Applications:
- Rolling: Rolling is commonly used in industries like construction, automotive, and aerospace to produce materials such as sheets, plates, and structural components. It is ideal for creating uniform thickness and large-scale production.
- Bending: Bending is often used in fabrication shops to create custom shapes and components. It is particularly useful for producing parts with specific angles or curves, such as brackets, frames, or decorative elements.
-
Material Suitability:
- Rolling: Rolling is suitable for a wide range of metals, including steel, aluminum, and copper. It is particularly effective for materials that need to be shaped into thin, uniform sheets or long structural profiles.
- Bending: Bending works well with ductile materials like mild steel, aluminum, and brass. However, it may not be suitable for brittle materials, as they can crack or fracture during the bending process.
-
Precision and Complexity:
- Rolling: Rolling is a high-precision process that can achieve tight tolerances, especially in cold rolling. It is ideal for producing large quantities of uniform products but is less suited for complex shapes.
- Bending: Bending allows for greater flexibility in creating complex shapes and custom designs. It is more adaptable to small-scale or custom fabrication projects.
-
Advantages and Limitations:
- Rolling: Rolling is highly efficient for mass production and can produce materials with consistent thickness and surface finish. However, it requires significant capital investment in equipment and is less flexible for small-scale or custom projects.
- Bending: Bending is versatile and cost-effective for small-scale or custom fabrication. It allows for precise control over angles and curves but may require secondary operations like trimming or finishing.
By understanding these differences, manufacturers can choose the most appropriate process for their specific needs, ensuring optimal results in terms of cost, efficiency, and product quality.
Summary Table:
Aspect | Rolling | Bending |
---|---|---|
Process | Metal passed through rollers to reduce thickness or alter shape. | Metal deformed along a specific axis to create angles or curves. |
Equipment | Rolling mills with large, powered rollers. | Press brakes or roll benders. |
Applications | Construction, automotive, aerospace (sheets, plates, structural components). | Fabrication shops (brackets, frames, decorative elements). |
Material Suitability | Steel, aluminum, copper (thin, uniform sheets or profiles). | Mild steel, aluminum, brass (ductile materials). |
Precision | High precision, tight tolerances, especially in cold rolling. | Flexible for complex shapes and custom designs. |
Advantages | Efficient for mass production, consistent thickness and finish. | Versatile and cost-effective for small-scale or custom fabrication. |
Limitations | High capital investment, less flexible for small-scale projects. | May require secondary operations like trimming or finishing. |
Need help choosing the right metal forming process? Contact our experts today for tailored solutions!