Sintering and annealing are both thermal processes used in materials science, but they serve distinct purposes and are applied under different conditions. Sintering involves heating metal particles below their melting point, often with added pressure, to bond them into a solid mass, enhancing strength and structural integrity. Annealing, on the other hand, is a heat treatment process used to relieve internal stresses in materials like metals or ceramics by heating them above their recrystallization temperature and then cooling them slowly. This process improves ductility and reduces hardness, making the material more workable. While sintering focuses on bonding particles, annealing aims to alter the material's internal structure to improve its properties.
Key Points Explained:
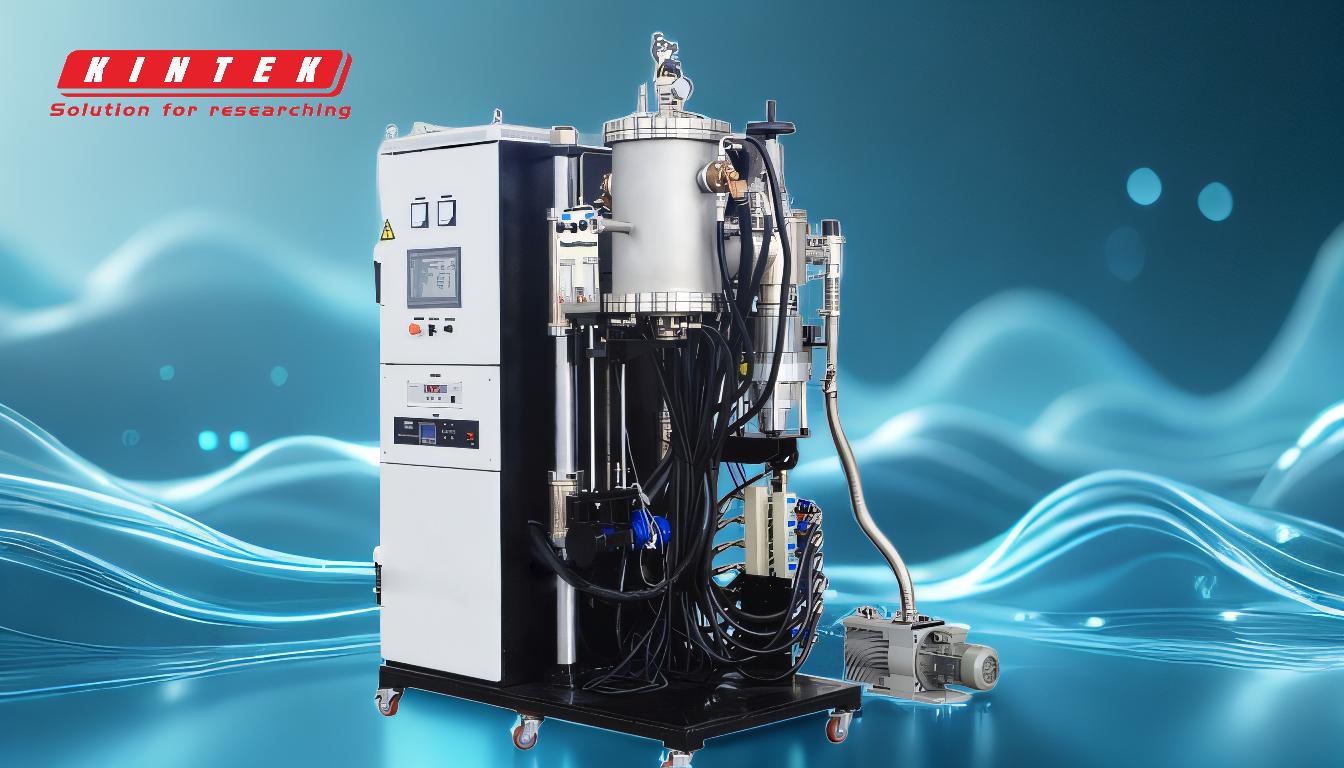
-
Purpose and Outcome:
- Sintering: The primary goal is to agglomerate metal particles into a cohesive solid structure without melting them. This process increases the material's strength and structural integrity.
- Annealing: The main objective is to relieve internal stresses within a material, such as metals or ceramics, by heating it above its recrystallization temperature and then cooling it slowly. This process enhances ductility and reduces hardness.
-
Temperature and Pressure:
- Sintering: Typically occurs at temperatures below the melting point of the material, often with the application of pressure. This allows for the bonding of particles without liquefaction, making it energy-efficient and suitable for materials with high melting points.
- Annealing: Requires heating the material above its recrystallization temperature but does not necessarily involve pressure. The key is maintaining the temperature for a specific duration before controlled cooling.
-
Mechanism:
- Sintering: Relies on the diffusion of atoms across particle boundaries, leading to the formation of necks between particles and eventual densification. This process can be aided by pressure, especially in powder metallurgy.
- Annealing: Involves the rearrangement of the material's internal structure, allowing dislocations to move and grains to grow, which reduces internal stresses and improves mechanical properties.
-
Applications:
- Sintering: Commonly used in powder metallurgy to produce complex shapes and components with high precision and minimal waste. It is also used in ceramics and certain types of metal fabrication.
- Annealing: Widely applied in metalworking and glass manufacturing to improve machinability, reduce brittleness, and prepare materials for further processing, such as cold working or machining.
-
Energy Efficiency and Control:
- Sintering: More energy-efficient than melting, as it operates at lower temperatures and can be precisely controlled to achieve consistent results. It is particularly advantageous for materials with high melting points.
- Annealing: While it requires heating to higher temperatures than sintering, the controlled cooling process is crucial for achieving the desired material properties, such as increased ductility and reduced internal stresses.
-
Material State:
- Sintering: Involves the bonding of solid particles without transitioning to a liquid state, preserving the material's original properties while enhancing its structural integrity.
- Annealing: Focuses on altering the material's internal structure through phase changes, such as recrystallization, to improve its mechanical properties without necessarily changing its physical form.
In summary, sintering and annealing are complementary processes in materials science, each with specific applications and outcomes. Sintering is ideal for creating strong, cohesive structures from powdered materials, while annealing is essential for improving the workability and reducing the brittleness of metals and ceramics. Understanding the differences between these processes is crucial for selecting the appropriate treatment for a given material and application.
Summary Table:
Aspect | Sintering | Annealing |
---|---|---|
Purpose | Bonds metal particles into a solid mass, enhancing strength and integrity. | Relieves internal stresses, improves ductility, and reduces hardness. |
Temperature | Below melting point, often with pressure. | Above recrystallization temperature, no pressure required. |
Mechanism | Diffusion of atoms across particle boundaries, forming necks and densification. | Rearrangement of internal structure, reducing stresses and improving properties. |
Applications | Powder metallurgy, ceramics, and metal fabrication. | Metalworking, glass manufacturing, and material preparation. |
Energy Efficiency | More energy-efficient due to lower temperatures and precise control. | Requires higher temperatures but controlled cooling is critical. |
Material State | Bonds solid particles without liquefaction. | Alters internal structure through phase changes like recrystallization. |
Need help choosing the right thermal process for your materials? Contact our experts today!