Tempering and quenching are two distinct heat treatment processes used to alter the mechanical properties of metals, particularly steel. Quenching involves rapidly cooling a metal from a high temperature to achieve high hardness and strength, but it often results in brittleness. Tempering, on the other hand, is a subsequent process where the quenched metal is reheated to a lower temperature and then cooled slowly to reduce brittleness and improve toughness and ductility. While quenching maximizes hardness, tempering balances hardness with toughness, making the material more suitable for practical applications.
Key Points Explained:
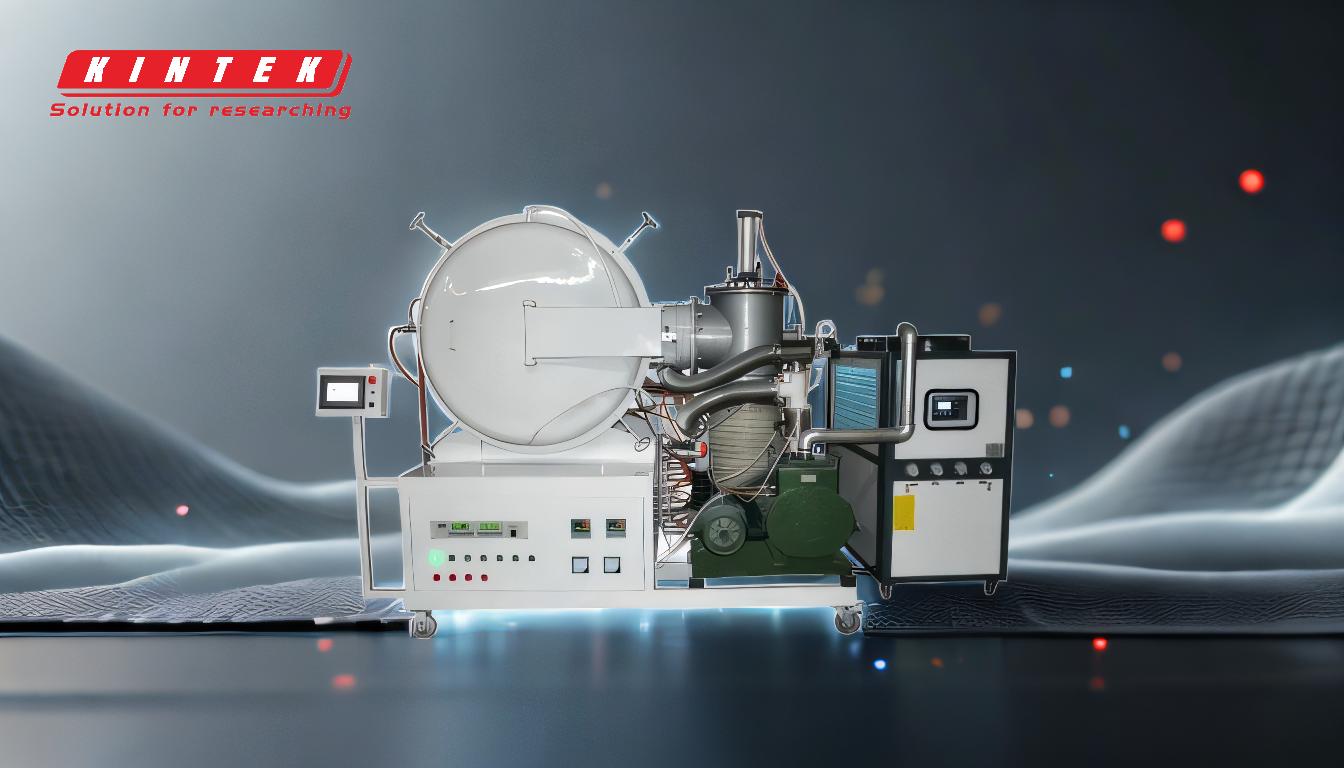
-
Purpose and Outcome of Quenching:
- Quenching is primarily used to increase the hardness and strength of metals, especially steel. This is achieved by heating the metal to a high temperature (above its critical temperature) and then cooling it rapidly, typically in water, oil, or air.
- The rapid cooling locks the metal's microstructure into a harder state, such as martensite in steel, which is very hard but also brittle.
- Quenching is often the first step in a two-step heat treatment process, followed by tempering.
-
Purpose and Outcome of Tempering:
- Tempering is performed after quenching to reduce the brittleness caused by the rapid cooling. It involves reheating the quenched metal to a temperature below its critical point and then cooling it slowly.
- This process allows some of the hardness to be sacrificed in exchange for increased toughness and ductility, making the metal less prone to cracking or breaking under stress.
- The exact temperature and duration of tempering depend on the desired balance between hardness and toughness for the specific application.
-
Microstructural Changes:
- During quenching, the rapid cooling prevents the formation of softer phases like pearlite, leading to a hard but brittle martensitic structure.
- Tempering modifies this martensitic structure by allowing some of the carbon atoms to diffuse out, forming smaller, more stable carbide particles. This reduces internal stresses and improves the metal's overall toughness.
-
Applications:
- Quenching is commonly used in applications where high hardness is critical, such as in cutting tools, gears, and bearings.
- Tempering is essential in applications where a balance of hardness and toughness is required, such as in structural components, springs, and automotive parts.
-
Process Sequence:
- The typical sequence is: heating (austenitizing) → quenching → tempering. This sequence ensures that the metal achieves the desired mechanical properties for its intended use.
-
Temperature and Cooling Rates:
- Quenching involves very high cooling rates, often achieved by immersing the hot metal in a quenching medium like water or oil.
- Tempering involves controlled heating to specific temperatures (usually between 150°C to 650°C for steel) and slower cooling rates, often in air.
-
Material Considerations:
- Not all metals can be quenched and tempered. The process is most effective for steels and certain alloys that can form martensite.
- The specific type of steel (e.g., carbon steel, alloy steel) will influence the exact quenching and tempering parameters.
By understanding the differences between tempering and quenching, engineers and metallurgists can tailor the heat treatment process to achieve the optimal combination of hardness, toughness, and ductility for a given application.
Summary Table:
Aspect | Quenching | Tempering |
---|---|---|
Purpose | Increases hardness and strength | Reduces brittleness, improves toughness and ductility |
Process | Rapid cooling from high temperature (water, oil, or air) | Reheating to lower temperature, followed by slow cooling |
Outcome | Hard but brittle material (e.g., martensite) | Balanced hardness and toughness |
Applications | Cutting tools, gears, bearings | Structural components, springs, automotive parts |
Temperature Range | Above critical temperature, rapid cooling | 150°C to 650°C (for steel), controlled heating |
Material Suitability | Effective for steels and alloys that form martensite | Suitable for steels requiring balanced properties |
Need expert advice on heat treatment processes? Contact us today to optimize your metal properties!