Vacuum hardening and normal hardening are both heat treatment processes used to increase the hardness and strength of metals, but they differ significantly in their methods, environments, and outcomes. Vacuum hardening involves heating the metal in a vacuum chamber to eliminate oxygen, preventing oxidation and ensuring a clean, bright surface. It is more expensive but offers better temperature control, higher purity, and the ability to treat a wider range of metals. Normal hardening, on the other hand, heats the metal directly in a gaseous atmosphere, which can lead to surface oxidation and impurities. While it is less costly, it may not achieve the same level of hardness or surface quality as vacuum hardening. The choice between the two depends on the material, desired properties, and budget.
Key Points Explained:
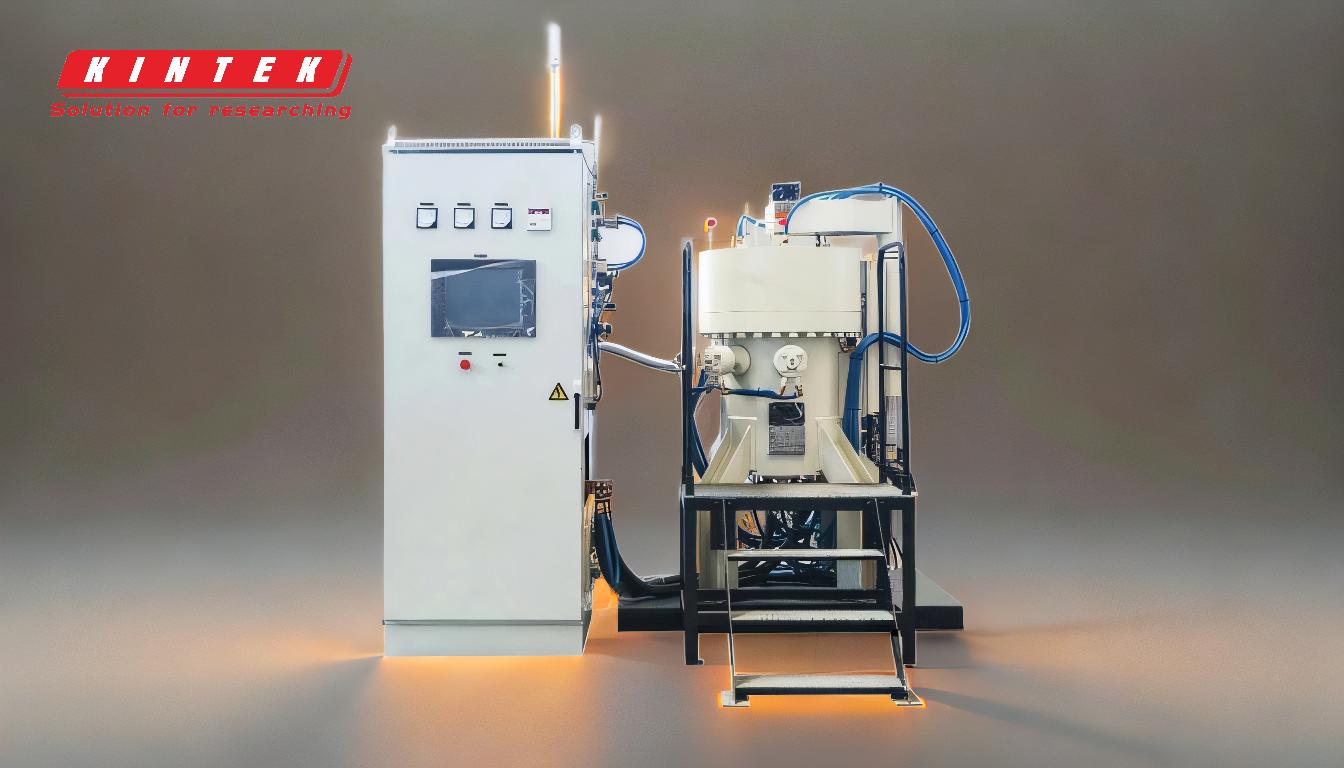
-
Environment During Heating:
- Vacuum Hardening: The metal is heated in a vacuum chamber, which removes air and creates an oxygen-free environment. This prevents oxidation and ensures a clean, bright surface.
- Normal Hardening: The metal is heated directly in a gaseous atmosphere, which can lead to oxidation and surface impurities.
-
Cost:
- Vacuum Hardening: More expensive due to the specialized equipment and vacuum technology required.
- Normal Hardening: Less expensive as it uses conventional heating methods and equipment.
-
Types of Metals:
- Vacuum Hardening: Can be used on a wider range of metals, including those that are more sensitive to oxidation.
- Normal Hardening: Typically used for metals that are less sensitive to oxidation and do not require the high purity achieved through vacuum hardening.
-
Hardness and Surface Quality:
- Vacuum Hardening: Achieves higher hardness levels and better surface quality due to the absence of oxidation and impurities. The hardness achieved depends on the metal type and the duration in the vacuum chamber.
- Normal Hardening: May not achieve the same level of hardness or surface quality, especially for metals prone to oxidation.
-
Temperature Control and Consistency:
- Vacuum Hardening: Offers better temperature control and consistency, leading to more uniform results.
- Normal Hardening: May have less precise temperature control, potentially leading to inconsistencies in the hardening process.
-
Energy Consumption:
- Vacuum Hardening: Reduces energy consumption due to improved insulation in vacuum furnace systems.
- Normal Hardening: Typically consumes more energy as it relies on conventional heating methods.
-
Quenching Methods:
- Vacuum Hardening: Quenching methods vary depending on the material, with gas quenching using nitrogen being the most common.
- Normal Hardening: Typically involves quenching in oil, water, or other liquids, which can vary in effectiveness depending on the material.
-
Applications:
- Vacuum Hardening: Ideal for applications requiring high purity, fine surface finish, and superior mechanical properties.
- Normal Hardening: Suitable for less demanding applications where cost is a primary concern and high surface quality is not critical.
In summary, vacuum hardening is a more advanced and costly process that offers significant advantages in terms of surface quality, hardness, and material versatility. Normal hardening, while less expensive, may not provide the same level of performance, especially for metals that are sensitive to oxidation or require high purity. The choice between the two methods should be based on the specific requirements of the application, including material type, desired properties, and budget constraints.
Summary Table:
Aspect | Vacuum Hardening | Normal Hardening |
---|---|---|
Environment | Oxygen-free vacuum chamber prevents oxidation and ensures a clean surface. | Gaseous atmosphere may cause oxidation and surface impurities. |
Cost | More expensive due to specialized equipment and vacuum technology. | Less expensive, using conventional heating methods. |
Metal Types | Suitable for a wider range of metals, including oxidation-sensitive ones. | Best for metals less sensitive to oxidation. |
Hardness & Surface | Higher hardness and better surface quality due to no oxidation. | May not achieve the same hardness or surface quality. |
Temperature Control | Better control and consistency for uniform results. | Less precise control, leading to potential inconsistencies. |
Energy Consumption | Reduced energy use due to improved insulation. | Typically consumes more energy. |
Quenching Methods | Gas quenching (e.g., nitrogen) is common. | Quenching in oil, water, or other liquids. |
Applications | Ideal for high-purity, fine surface finish, and superior mechanical properties. | Suitable for cost-sensitive applications where high surface quality isn't critical. |
Need help choosing the right hardening process for your metals? Contact our experts today!