Electric arc furnaces (EAFs) are widely used in steel production due to their ability to recycle scrap metal and achieve precise temperature and composition control. However, they come with several disadvantages, including uneven heat distribution, high operating costs, potential release of harmful gases, and significant energy consumption. These factors can lead to increased operational challenges and expenses, making it essential for users to carefully evaluate their suitability for specific applications.
Key Points Explained:
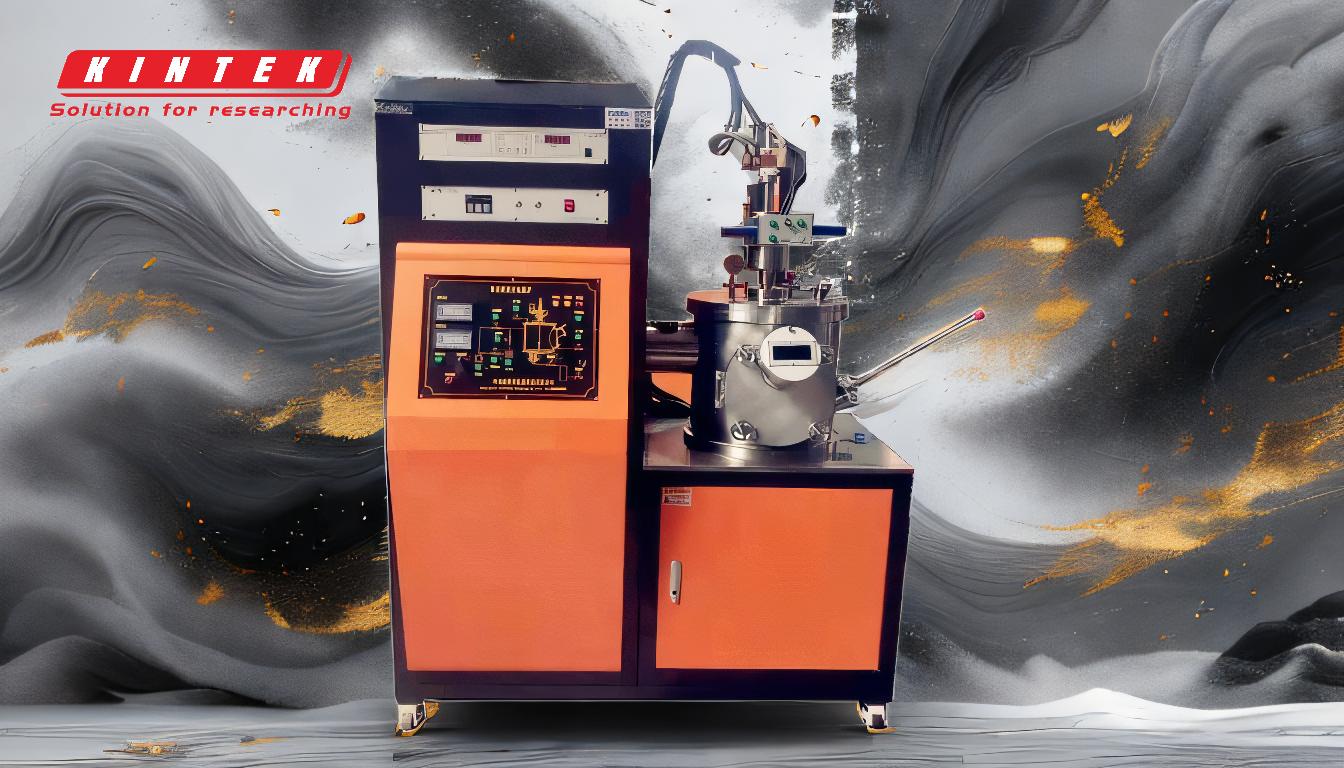
-
Uneven Heat Distribution
- The electric arc in the furnace can cause uneven heat distribution, which may lead to inconsistent melting and refining of the metal. This can result in variations in the quality of the final product.
- Uneven heating also requires additional energy to compensate for temperature differences, reducing overall efficiency.
-
Release of Harmful Gases
- The arc can react with furnace gases and vapors, releasing large amounts of hydrogen and nitrogen. These gases can negatively affect the quality of the steel and may require additional measures to mitigate their impact.
- The release of harmful gases also poses environmental and safety concerns, necessitating proper ventilation and gas management systems.
-
High Operating Costs
- Electric arc furnaces rely heavily on electricity, which is often more expensive than other energy sources like gas or oil. This makes the operational costs of EAFs significantly higher.
- The high cost of electricity can be a major disadvantage, especially in regions where energy prices are volatile or elevated.
-
Energy Consumption and Strain on Electrical Systems
- EAFs consume a significant amount of power, which can strain local electrical grids and infrastructure. This may require upgrades to power systems to accommodate the furnace's energy demands.
- Careful management of energy consumption is necessary to maintain efficiency, adding to the operational complexity.
-
Need for Professional Repairs
- While electric arc furnaces are generally robust, their complex systems can develop issues that require professional repairs. These repairs can be costly and time-consuming, leading to potential downtime.
- The need for specialized expertise further increases the overall cost of ownership.
-
Environmental and Operational Challenges
- Despite their ability to recycle scrap metal, EAFs still face challenges related to emissions and energy efficiency. While they produce fewer emissions compared to traditional blast furnaces, managing the release of gases like hydrogen and nitrogen remains a concern.
- The high energy consumption of EAFs also contributes to their environmental footprint, making it essential to balance their benefits with their operational drawbacks.
In summary, while electric arc furnaces offer significant advantages in terms of flexibility and recycling capabilities, their disadvantages, such as uneven heat distribution, high operating costs, and energy consumption, must be carefully considered. These factors can impact both the economic and environmental viability of using EAFs in steel production.
Summary Table:
Disadvantage | Impact |
---|---|
Uneven Heat Distribution | Leads to inconsistent melting, reduced efficiency, and product quality issues. |
Release of Harmful Gases | Affects steel quality, requires gas management systems, and poses safety risks. |
High Operating Costs | Increased expenses due to reliance on expensive electricity. |
Energy Consumption | Strains electrical grids, requires infrastructure upgrades, and adds complexity. |
Need for Professional Repairs | Costly and time-consuming repairs, leading to potential downtime. |
Environmental Challenges | Emissions and high energy consumption contribute to environmental concerns. |
Need help addressing the challenges of electric arc furnaces? Contact our experts today for tailored solutions!