Induction furnaces, while highly efficient for melting metals, come with several notable disadvantages. These include the inability to refine materials, requiring charge materials to be free of oxides and of known composition, which can lead to the loss of some alloying elements due to oxidation. Additionally, the initial investment for induction furnaces is significant, encompassing specialized equipment and power supplies. Operating these furnaces also demands skilled personnel knowledgeable in induction heating principles and safety procedures. Furthermore, induction heating is most effective for surface heating, potentially limiting its application in certain heat treatment processes.
Key Points Explained:
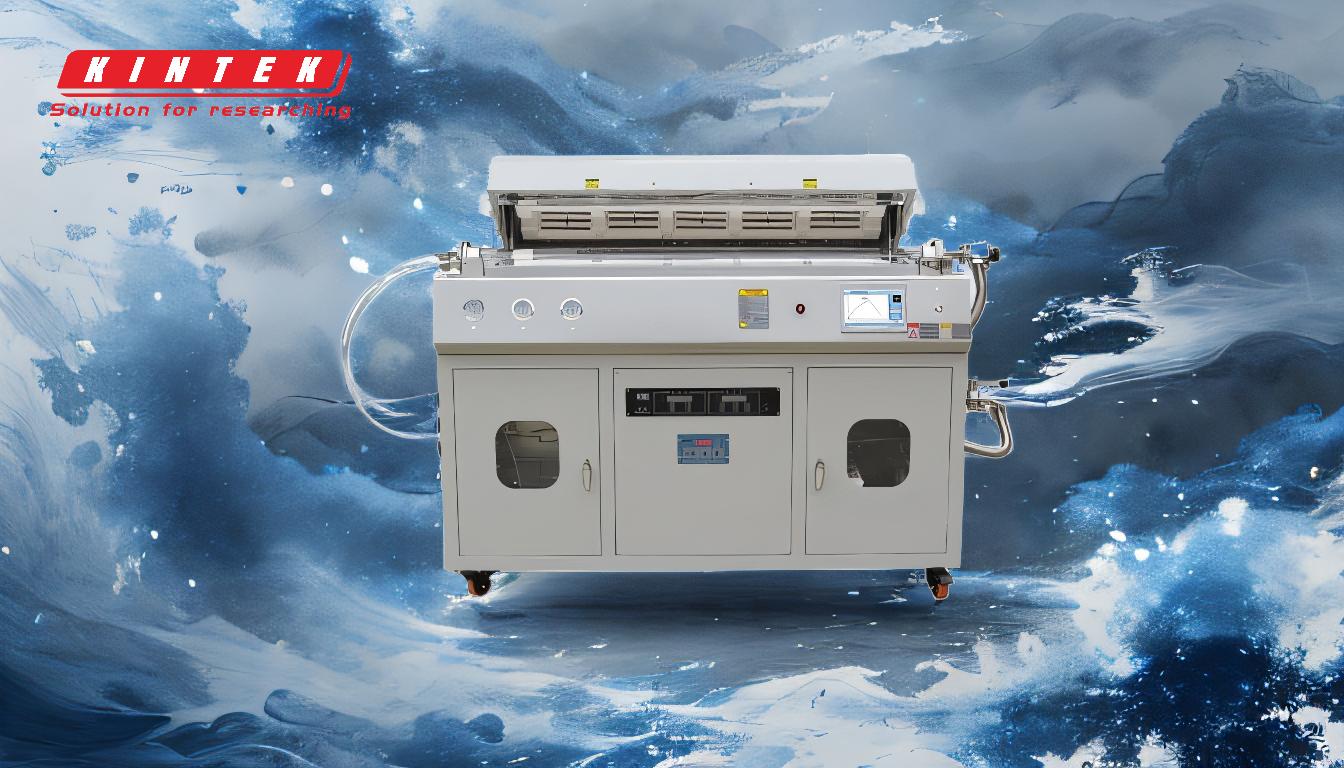
-
Lack of Refining Capacity
- Induction furnaces cannot refine materials, meaning the charge materials must already be free of oxides and of a known composition. This limitation can be problematic when dealing with impure or contaminated materials, as the furnace cannot remove impurities during the melting process.
- Some alloying elements may be lost due to oxidation, necessitating their re-addition to the melt. This adds complexity and cost to the process, especially in applications requiring precise alloy compositions.
-
High Initial Investment
- The cost of setting up an igbt induction furnace is substantial. This includes not only the furnace itself but also specialized equipment and power supplies required for operation. The initial capital expenditure can be a barrier for smaller operations or those with limited budgets.
- The need for high-quality components and advanced technology, such as IGBT (Insulated Gate Bipolar Transistor) systems, further drives up costs. These components are essential for efficient and reliable operation but come at a premium.
-
Requirement for Skilled Personnel
- Operating an induction furnace requires a high level of expertise. Personnel must be well-versed in induction heating principles, safety procedures, and the specific operational nuances of the equipment.
- The complexity of the technology means that training and retaining skilled operators can be challenging and costly. This is particularly true in regions where such expertise is scarce.
-
Limitations in Heat Treatment Applications
- Induction heating is most effective for surface heating, which can limit its application in processes that require uniform heating throughout the material. For example, certain heat treatment processes may not achieve the desired results if the heat does not penetrate deeply enough.
- This limitation can restrict the use of induction furnaces in industries where deep, uniform heating is essential, such as in the heat treatment of large or thick components.
-
Energy Consumption and Efficiency
- While induction furnaces are generally energy-efficient, the high power requirements for melting metals can lead to significant energy consumption. This can be a concern in regions with high electricity costs or where energy resources are limited.
- The efficiency of the furnace can also be influenced by the quality of the power supply and the condition of the equipment. Any inefficiencies can lead to increased operational costs over time.
-
Maintenance and Operational Challenges
- Induction furnaces require regular maintenance to ensure optimal performance. This includes checking and replacing components such as coils, crucibles, and power supplies, which can wear out over time.
- The operational environment can also pose challenges, such as the need for cooling systems to manage the heat generated during operation. These systems add to the complexity and cost of maintaining the furnace.
In summary, while induction furnaces offer many advantages, such as rapid heating and precise temperature control, they also come with significant drawbacks. These include the lack of refining capacity, high initial investment, the need for skilled personnel, limitations in heat treatment applications, energy consumption concerns, and maintenance challenges. Understanding these disadvantages is crucial for making informed decisions when considering the use of induction furnaces in various industrial applications.
Summary Table:
Disadvantage | Details |
---|---|
Lack of Refining Capacity | Cannot refine materials; requires pre-purified charge materials. |
High Initial Investment | Significant setup costs for equipment and power supplies. |
Requirement for Skilled Personnel | Needs operators trained in induction heating and safety protocols. |
Limitations in Heat Treatment | Effective for surface heating, but not for deep or uniform heating. |
Energy Consumption | High power requirements can lead to increased operational costs. |
Maintenance Challenges | Regular upkeep needed for coils, crucibles, and cooling systems. |
Want to learn more about induction furnaces and their alternatives? Contact our experts today!