The effect of pressure in sputtering is a critical factor that influences the behavior of sputtered ions, the energy distribution of source atoms, and the overall quality of the deposited film. At higher pressures, ions collide with gas atoms, leading to a diffusive motion and random walk, which affects the deposition uniformity and coverage. Lower pressures, on the other hand, allow for high-energy ballistic impacts, resulting in more direct and energetic deposition. Pressure also governs the mean free path of ions, impacting their energy distribution and the sputtering yield, which varies depending on target materials and sputtering conditions. Understanding these dynamics is essential for optimizing sputter deposition processes.
Key Points Explained:
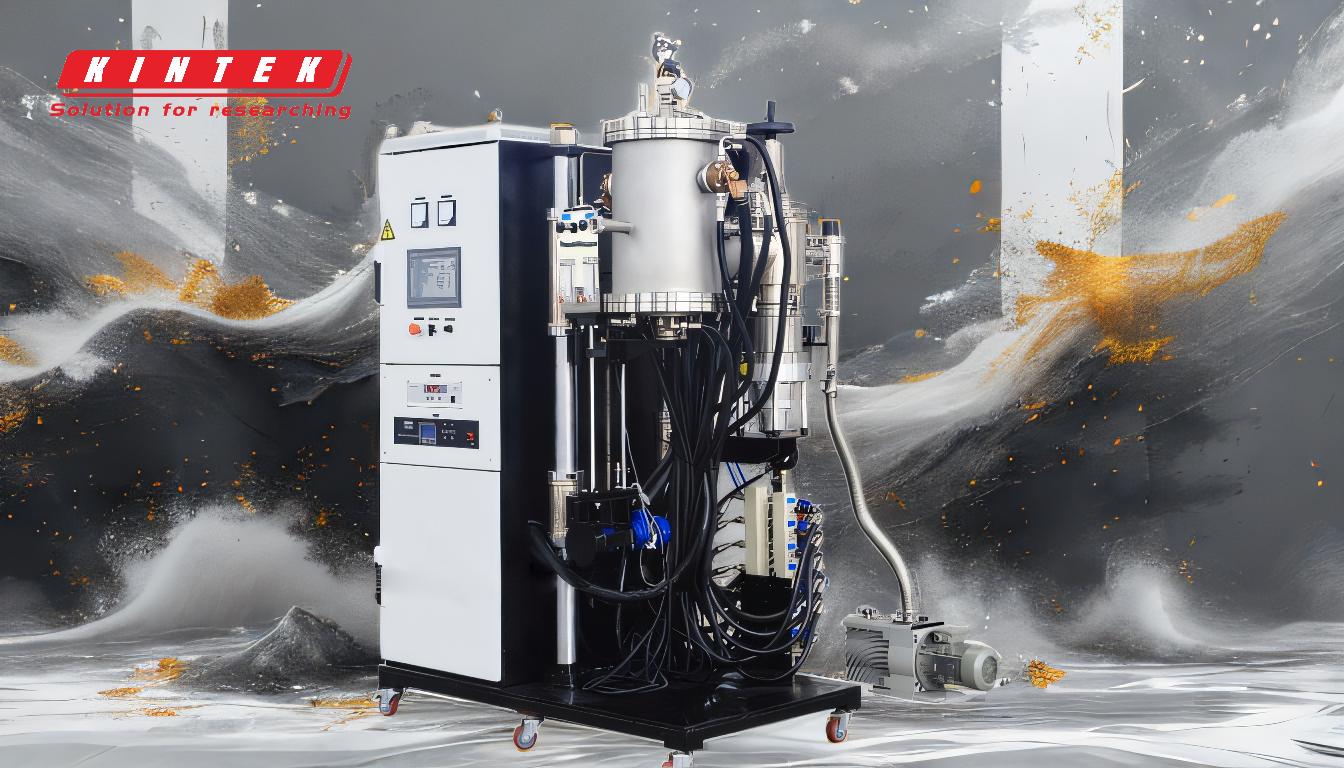
-
Influence of Pressure on Ion Motion:
- Higher Pressures: At elevated gas pressures, sputtered ions collide frequently with gas atoms. These collisions act as a moderator, causing the ions to move diffusively. This results in a random walk, where ions take a longer, less direct path to reach the substrate or chamber walls. This diffusive motion can improve coverage uniformity but may reduce the energy of the deposited particles.
- Lower Pressures: In contrast, lower pressures reduce the number of collisions between ions and gas atoms. This allows ions to travel in a more ballistic manner, maintaining higher energy levels and resulting in more direct impacts on the substrate. This can lead to denser and more adherent films but may reduce coverage uniformity.
-
Energy Distribution and Mean Free Path:
- Mean Free Path: The mean free path of ions is the average distance they travel between collisions. Pressure directly influences this parameter; higher pressures shorten the mean free path, while lower pressures extend it. A shorter mean free path at higher pressures leads to more frequent collisions and energy loss, whereas a longer mean free path at lower pressures allows ions to retain more energy until they reach the substrate.
- Energy Distribution: The energy distribution of source atoms is governed by the pressure. In hyperthermal techniques like sputtering, pressure plays a decisive role in determining how energy is distributed among the sputtered atoms. This affects the sputtering yield and the quality of the deposited film.
-
Sputtering Yield and Material Dependence:
- Sputtering Yield: The sputtering yield, defined as the number of target atoms ejected per incident ion, is influenced by pressure. Higher pressures can reduce the sputtering yield due to energy loss from collisions, while lower pressures can enhance it by allowing ions to retain more energy. The yield also varies depending on the target material and the specific sputtering conditions.
- Material Compatibility: Different materials respond differently to changes in pressure. For example, some materials may require higher pressures to achieve optimal sputtering yields, while others may perform better at lower pressures. Understanding these material-specific behaviors is crucial for optimizing the sputtering process.
-
Deposition Quality and Film Properties:
- Film Density and Adhesion: The kinetic energy of emitted particles, which is influenced by pressure, determines their direction and deposition on the substrate. Lower pressures generally result in higher kinetic energy, leading to denser and more adherent films. Higher pressures may result in less dense films due to energy loss from collisions.
- Surface Mobility: The excess energy of metal ions can increase surface mobility during the deposition process. This can impact the quality of the deposited film, as higher surface mobility can lead to smoother and more uniform films. Pressure plays a role in determining the extent of this surface mobility.
-
Process Optimization and Practical Considerations:
- Pressure and Temperature: Pressure should always be considered alongside deposition temperature when optimizing the sputtering process. The interplay between these two parameters can significantly affect the outcome of the deposition.
- Power Source: The type of power source (DC or RF) used in sputtering also interacts with pressure. For example, RF sputtering may be more effective at lower pressures, while DC sputtering might perform better at higher pressures. The choice of power source, along with pressure, affects the deposition rate, material compatibility, and overall cost of the process.
In summary, pressure is a fundamental parameter in sputtering that affects ion motion, energy distribution, sputtering yield, and the quality of the deposited film. By carefully controlling pressure, along with other parameters like temperature and power source, one can optimize the sputtering process to achieve desired film properties and deposition outcomes.
Summary Table:
Aspect | Higher Pressure | Lower Pressure |
---|---|---|
Ion Motion | Diffusive motion, random walk, improved coverage uniformity, reduced energy | Ballistic motion, direct impacts, higher energy, denser films |
Mean Free Path | Shorter, frequent collisions, energy loss | Longer, fewer collisions, retained energy |
Sputtering Yield | Reduced due to energy loss | Enhanced due to retained energy |
Film Density & Adhesion | Less dense films due to energy loss | Denser, more adherent films |
Surface Mobility | Lower surface mobility, less uniform films | Higher surface mobility, smoother, more uniform films |
Process Optimization | Better coverage uniformity, reduced energy | Higher energy, denser films, potential for reduced coverage uniformity |
Need help optimizing your sputtering process? Contact our experts today for tailored solutions!