Sintering temperature plays a critical role in determining the grain size of materials, which directly impacts their mechanical properties. Higher sintering temperatures generally lead to increased grain growth due to enhanced atomic diffusion, resulting in larger grains. However, excessive grain growth can degrade material properties such as strength and durability. Conversely, lower sintering temperatures may result in smaller grains but can also lead to insufficient densification, reducing the material's overall performance. Optimal sintering temperatures, such as 1500℃ for zirconia, balance grain growth and densification to achieve the desired material properties. Deviations from this temperature range can significantly affect grain size and, consequently, material strength.
Key Points Explained:
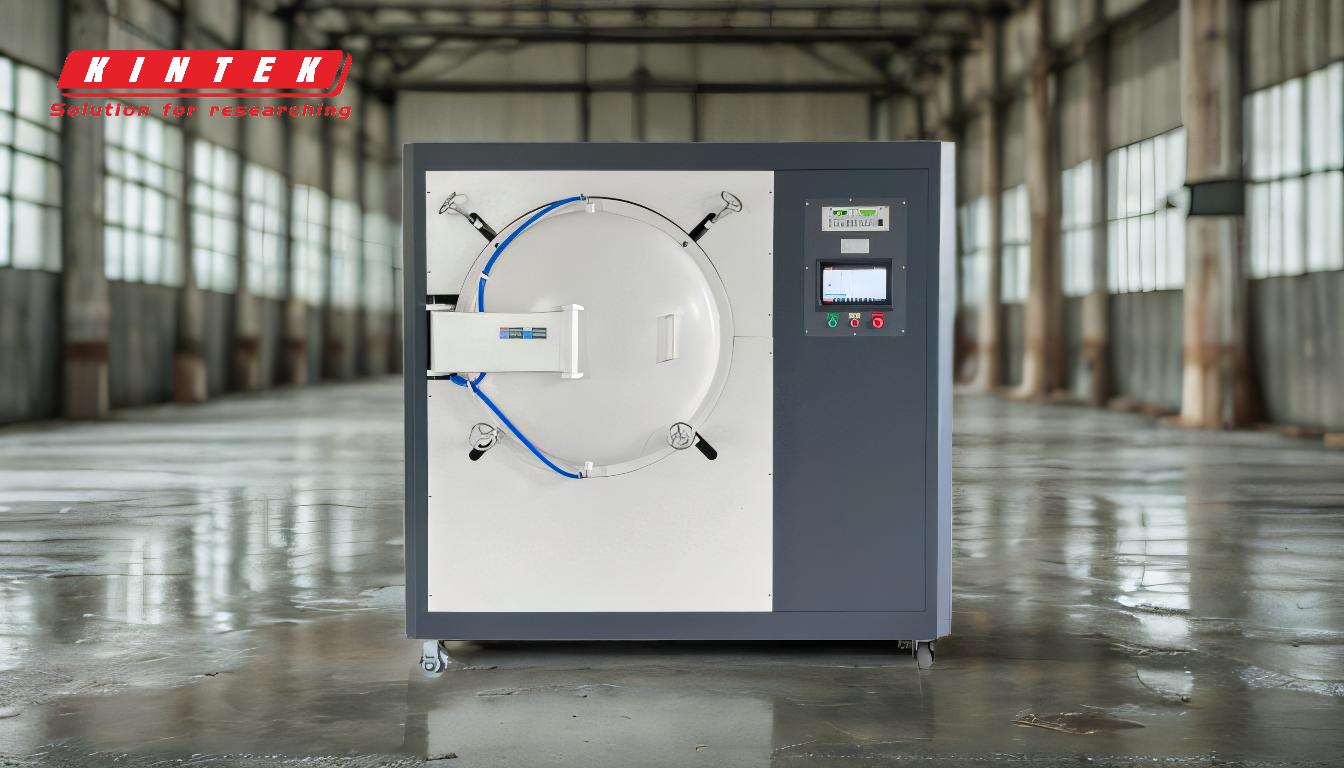
-
Effect of Sintering Temperature on Grain Growth:
- Higher sintering temperatures promote atomic diffusion, leading to increased grain growth.
- This results in larger grains, which can negatively impact material properties if excessive.
- Lower sintering temperatures restrict grain growth, producing smaller grains but may compromise densification.
-
Impact of Grain Size on Material Properties:
- Larger grains can reduce material strength and durability due to weakened grain boundaries.
- Smaller grains generally enhance strength and toughness but require optimal sintering conditions to ensure proper densification.
-
Optimal Sintering Temperature:
- For materials like zirconia, sintering at approximately 1500℃ maximizes strength by balancing grain growth and densification.
- Deviations of 150℃ above or below this temperature can lead to significant drops in strength due to uncontrolled grain growth or insufficient densification.
-
Role of Sintering Atmosphere:
- The sintering atmosphere (e.g., reducing or oxidizing) influences grain size and material properties.
- A reducing atmosphere prevents oxidation and promotes densification, contributing to controlled grain growth.
-
Microstructural Changes During Sintering:
- Sintering affects grain size, pore size, and grain boundary distribution, all of which influence material properties.
- Proper control of sintering parameters ensures a desirable microstructure with optimal mechanical properties.
-
Trade-offs in Sintering Parameters:
- Higher temperatures and longer sintering times can lead to defects and reduced properties if not carefully managed.
- Lower temperatures or insufficient heating times may result in incomplete densification and degraded performance.
By understanding these key points, purchasers of equipment and consumables can make informed decisions about sintering processes to achieve the desired material properties for specific applications.
Summary Table:
Factor | Impact on Material Properties |
---|---|
Higher Sintering Temperatures | Promotes grain growth, leading to larger grains but may reduce strength if excessive. |
Lower Sintering Temperatures | Restricts grain growth, producing smaller grains but may compromise densification. |
Optimal Sintering Temperature | Balances grain growth and densification (e.g., 1500℃ for zirconia) for maximum strength. |
Sintering Atmosphere | Reducing atmosphere prevents oxidation and promotes densification for controlled grain growth. |
Microstructural Changes | Affects grain size, pore size, and grain boundaries, influencing mechanical properties. |
Trade-offs in Sintering | Higher temperatures/longer times may cause defects; lower temperatures may lead to poor densification. |
Optimize your sintering process for superior material properties—contact our experts today!