Sintering is a critical process in materials science where temperature plays a pivotal role in determining the final properties of the material. The effect of temperature on sintering is multifaceted, influencing grain growth, densification, porosity, and mechanical properties such as strength and hardness. Optimal sintering temperatures and controlled heating and cooling rates are essential to achieve desired material characteristics. High temperatures promote particle bonding and diffusion, but excessive temperatures or improper heating rates can lead to defects or degraded properties. Understanding the interplay between temperature, heating rate, and other variables like atmosphere and particle size is crucial for optimizing the sintering process.
Key Points Explained:
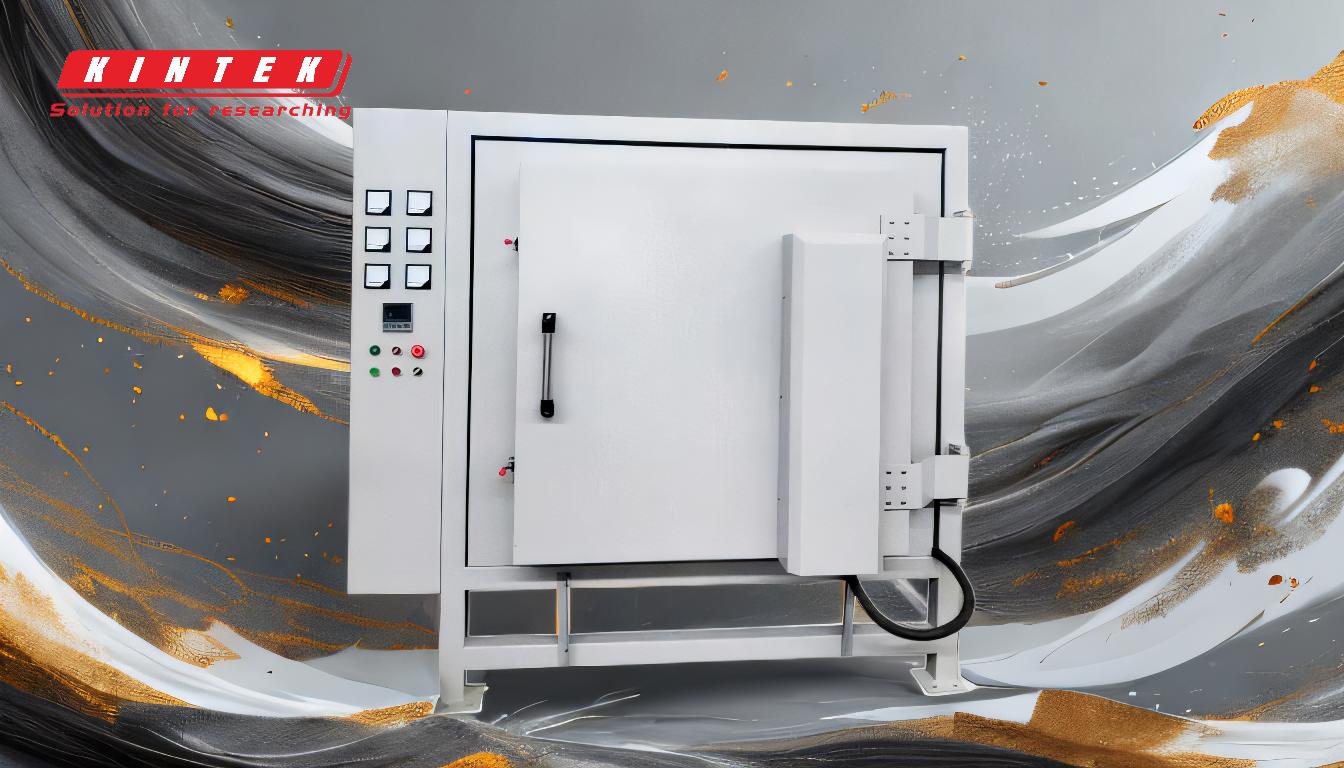
-
Temperature's Role in Particle Bonding and Diffusion:
- High temperatures, often reaching several thousand degrees Celsius, are essential for promoting bonding and diffusion between powder particles.
- This bonding leads to grain growth and densification, which are critical for achieving the desired microstructure and mechanical properties of the sintered material.
-
Sintering vs. Melting:
- Sintering occurs at temperatures below the material's melting point, relying on a combination of temperature and pressure to fuse particles.
- Melting, on the other hand, requires the material to reach its melting point, turning it into a liquid. Sintering can thus be performed at lower temperatures, making it suitable for materials that might degrade or oxidize at higher temperatures.
-
Critical Temperature Ranges:
- From room temperature to 900°C, the effect on the material is minimal. However, the temperature ramp rate from 900°C to the top sintering temperature, the consistency of temperature during the hold time, and the cooling rate back to around 900°C are all critical.
- Precise control over these temperature ranges ensures uniform densification and minimizes defects.
-
Impact on Microstructure:
- The sintering temperature directly influences the grain size, pore size, and grain boundary shape and distribution in the material's microstructure.
- These microstructural changes, in turn, affect the material's properties, such as strength, durability, and hardness.
-
Porosity, Density, and Mechanical Properties:
- Sintering temperature and time significantly impact the porosity, density, strength, and hardness of the sintered body.
- High sintering temperatures and prolonged heating times can reduce porosity and increase density, but excessive temperatures may lead to defects or degraded properties.
- Conversely, insufficient temperatures or heating times can result in incomplete sintering, leading to poor material properties.
-
Variables Affecting Sintering:
- Besides temperature, other variables such as the sintering atmosphere (air, vacuum, or inert gases like argon/nitrogen), heating rate, pressure, particle size, and composition play crucial roles.
- High-temperature sintering can enhance tensile strength, bending fatigue strength, and impact energy, but these benefits must be balanced against the risk of defects.
-
Heating Rate Considerations:
- The heating rate is a critical factor; if it is too high, it can cause insufficient sintering inside the material, leading to significant differences in sintering degree across different areas.
- This can result in a high-temperature melting peak and high crystallinity, which may not be desirable for certain applications.
-
Optimization of Sintering Parameters:
- To achieve the best results, it is essential to optimize the sintering parameters, including temperature, heating rate, pressure, and atmosphere.
- Smaller particle sizes and homogeneous compositions generally promote better densification and more uniform properties in the sintered material.
In summary, temperature is a fundamental factor in the sintering process, influencing everything from particle bonding and diffusion to the final material properties. Careful control of temperature, along with other sintering parameters, is essential to produce high-quality sintered materials with the desired characteristics.
Summary Table:
Aspect | Impact of Temperature |
---|---|
Particle Bonding | High temperatures promote bonding and diffusion, essential for grain growth and densification. |
Sintering vs. Melting | Sintering occurs below melting point, making it ideal for materials prone to degradation. |
Critical Temperature Ranges | Precise control between 900°C and top sintering temperature ensures uniform densification. |
Microstructure | Influences grain size, pore size, and grain boundary distribution, affecting material properties. |
Porosity & Density | High temperatures reduce porosity and increase density, but excessive heat may cause defects. |
Variables | Atmosphere, heating rate, pressure, particle size, and composition also play critical roles. |
Heating Rate | Too high a rate can cause uneven sintering, leading to undesirable material properties. |
Optimization | Balancing temperature, heating rate, and other parameters is key to achieving desired results. |
Need help optimizing your sintering process? Contact our experts today for tailored solutions!