The effective size of a sieve refers to the diameter of the smallest particle that can pass through the sieve's mesh openings. It is a critical parameter in particle size analysis, as it determines the classification and separation of materials based on their size. The effective size is influenced by the mesh design, including the wire diameter and the opening size, and is often used in industries such as construction, pharmaceuticals, and food processing to ensure consistent product quality. Understanding the effective size helps in selecting the right sieve for specific applications and achieving accurate particle size distribution results.
Key Points Explained:
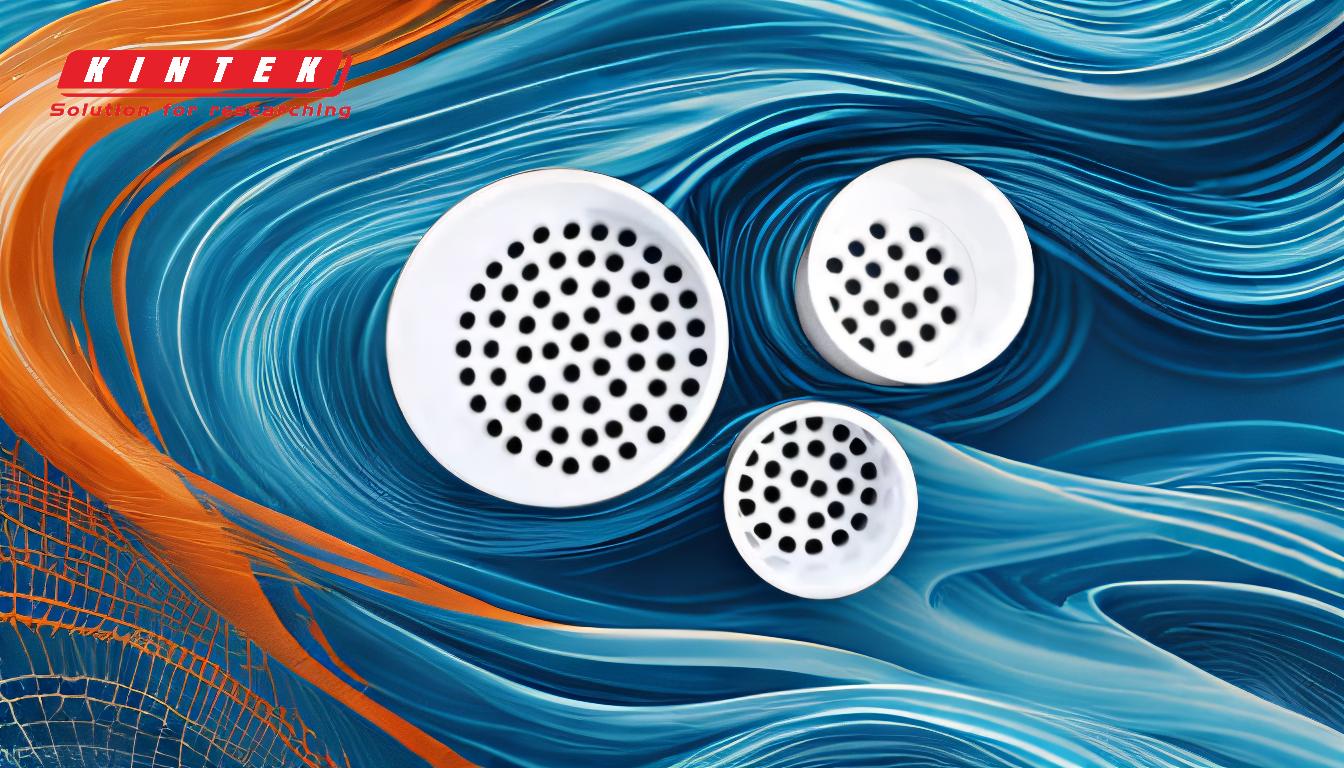
-
Definition of Effective Size:
- The effective size of a sieve is the diameter of the smallest particle that can pass through the sieve's openings. It is a measure of the sieve's ability to separate particles based on size.
- This parameter is crucial for applications requiring precise particle size control, such as in the pharmaceutical industry for drug formulation or in construction for grading aggregates.
-
Factors Influencing Effective Size:
- Mesh Design: The size of the openings in the sieve mesh directly affects the effective size. Larger openings allow larger particles to pass through, while smaller openings restrict passage to smaller particles.
- Wire Diameter: The thickness of the wires used in the sieve mesh can also influence the effective size. Thicker wires reduce the open area, potentially affecting the passage of particles.
- Material Properties: The type of material being sieved (e.g., shape, density, and hardness) can impact the effective size, as irregularly shaped or dense particles may not pass through as easily as spherical or less dense particles.
-
Measurement and Standards:
- The effective size is typically measured using standardized test methods, such as those outlined by ASTM (American Society for Testing and Materials) or ISO (International Organization for Standardization).
- These standards ensure consistency and accuracy in sieve analysis, allowing for reliable comparisons across different sieves and materials.
-
Applications of Effective Size:
- Quality Control: In industries like food processing, the effective size ensures that products meet specific size specifications, which can affect texture, taste, and shelf life.
- Material Separation: In mining and construction, sieves with specific effective sizes are used to separate materials into different grades, ensuring that only particles of the desired size are used in construction or further processing.
- Research and Development: In laboratories, understanding the effective size helps in developing new materials or formulations by providing precise control over particle size distribution.
-
Importance in Sieve Selection:
- Selecting a sieve with the appropriate effective size is essential for achieving accurate results in particle size analysis. Using a sieve with too large or too small an effective size can lead to incorrect classifications and affect the quality of the final product.
- The effective size also plays a role in determining the efficiency of the sieving process, as sieves with the correct effective size can reduce processing time and improve yield.
-
Challenges and Considerations:
- Particle Shape: Irregularly shaped particles may not pass through the sieve as easily as spherical particles, leading to potential inaccuracies in the effective size measurement.
- Sieve Wear and Tear: Over time, the effective size of a sieve can change due to wear and tear, especially in high-throughput applications. Regular calibration and maintenance are necessary to ensure consistent performance.
- Environmental Factors: Factors such as humidity and temperature can affect the sieving process, potentially altering the effective size and the accuracy of the results.
By understanding the effective size of a sieve, users can make informed decisions about sieve selection and application, ensuring that their processes meet the required standards and produce high-quality results.
Summary Table:
Aspect | Details |
---|---|
Definition | Diameter of the smallest particle that can pass through the sieve's openings. |
Key Factors | Mesh design, wire diameter, material properties. |
Measurement Standards | ASTM, ISO. |
Applications | Quality control, material separation, R&D. |
Importance | Ensures accurate particle size distribution and process efficiency. |
Challenges | Particle shape, sieve wear, environmental factors. |
Need help selecting the right sieve for your application? Contact our experts today for personalized guidance!