The electricity consumption of an induction furnace, particularly for steel melting, is a critical factor for operational efficiency and cost management. On average, a steel induction furnace consumes approximately 625 kWh per ton of steel melted. This figure can vary depending on factors such as furnace design, operating conditions, and the type of induction technology used, such as an IGBT induction furnace. Understanding these variables helps in optimizing energy usage and reducing operational costs.
Key Points Explained:
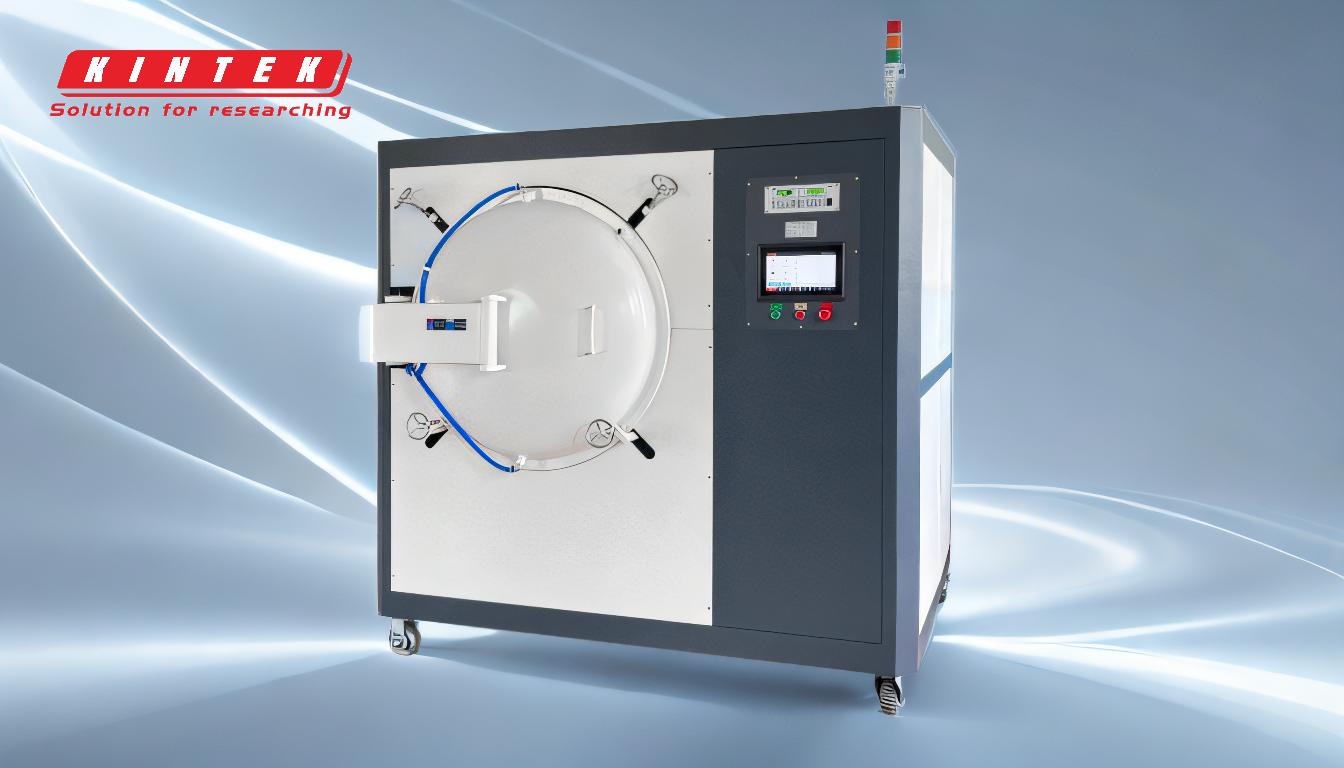
-
Standard Power Consumption:
- The standard power consumption for a steel induction furnace is 625 kWh/ton. This is a benchmark for energy efficiency in steel melting operations.
- This figure is based on well-designed and properly operated furnaces, ensuring minimal energy waste.
-
Factors Influencing Electricity Consumption:
- Furnace Design: The efficiency of the furnace design, including the coil configuration and insulation, plays a significant role in energy consumption.
- Operating Conditions: Factors such as melt rate, charge material quality, and temperature control impact energy usage. For example, higher melt rates may increase energy consumption.
- Induction Technology: Advanced technologies like IGBT induction furnaces offer higher efficiency and precise power control, reducing overall energy consumption compared to older SCR-based systems.
-
Importance of Energy Efficiency:
- Reducing electricity consumption directly lowers operational costs and improves the sustainability of the melting process.
- Energy-efficient furnaces also contribute to reduced greenhouse gas emissions, aligning with environmental regulations.
-
Optimization Strategies:
- Regular Maintenance: Ensuring the furnace is well-maintained minimizes energy losses due to wear and tear.
- Proper Charge Preparation: Using clean and appropriately sized charge materials reduces melting time and energy usage.
- Advanced Control Systems: Implementing modern control systems in IGBT induction furnaces allows for precise power management, further enhancing efficiency.
-
Comparison with Other Furnace Types:
- Induction furnaces generally have lower energy consumption compared to traditional arc furnaces, especially for smaller-scale operations.
- The use of IGBT induction furnaces further improves this advantage due to their higher efficiency and faster heating capabilities.
By focusing on these key points, operators can better understand and manage the electricity consumption of induction furnaces, ensuring cost-effective and sustainable operations.
Summary Table:
Key Aspect | Details |
---|---|
Standard Consumption | 625 kWh/ton of steel melted (benchmark for energy efficiency) |
Factors Affecting Usage | - Furnace design (coil, insulation) - Operating conditions (melt rate, charge quality) - Induction technology (e.g., IGBT) |
Optimization Strategies | - Regular maintenance - Proper charge preparation - Advanced control systems |
Comparison with Arc Furnaces | Lower energy consumption, especially with IGBT induction furnaces |
Discover how to optimize your induction furnace's energy efficiency—contact our experts today!