Electron beam evaporation is a thin-film deposition technique used to create high-purity coatings on substrates. It involves using a focused electron beam within a vacuum environment to heat and evaporate a target material, which then condenses onto a substrate to form a thin film. The process relies on key components such as a vacuum chamber, an electron beam source (typically a tungsten filament), a crucible to hold the source material, and a magnetic field to focus the electron beam. The electron beam's kinetic energy is converted into thermal energy upon impact, heating the target material to its evaporation point. This technique is widely used in industries requiring precise and high-quality thin-film coatings, such as semiconductors, optics, and aerospace.
Key Points Explained:
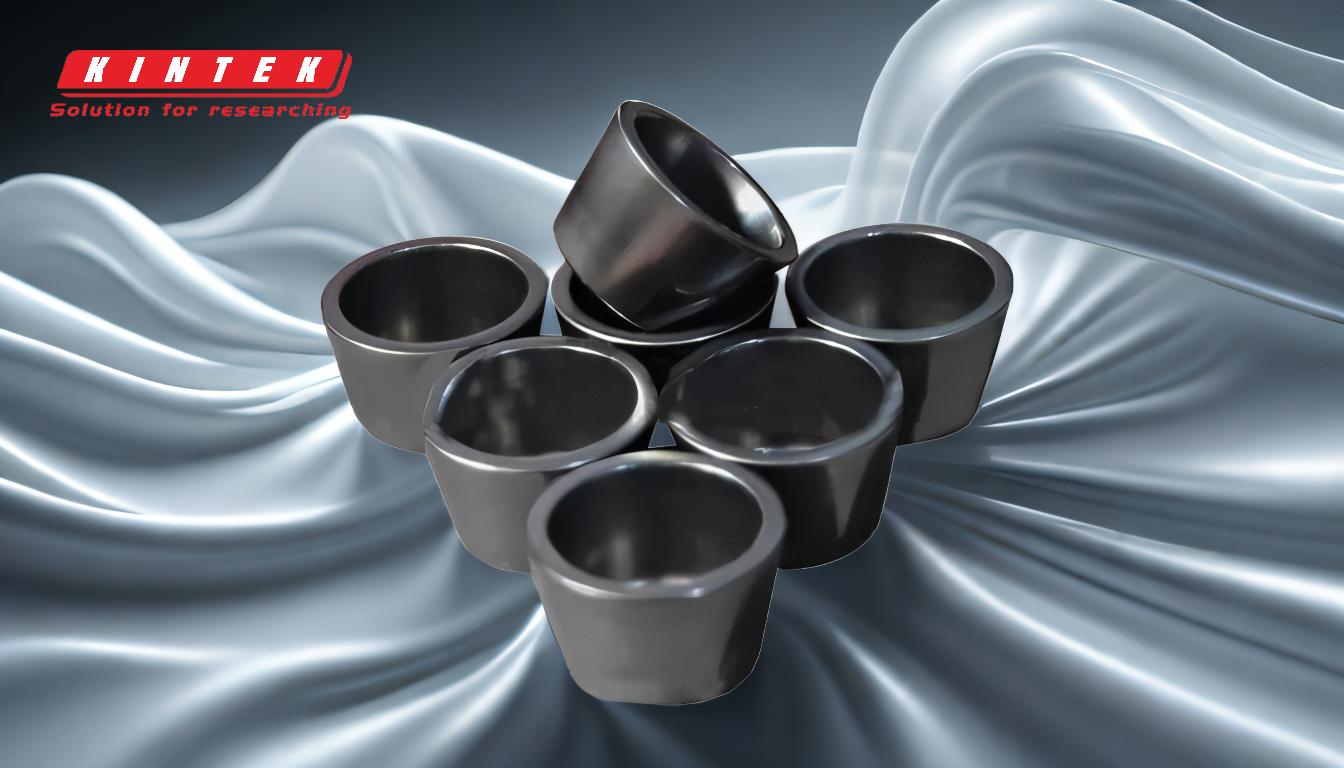
-
Vacuum Environment:
- The process takes place in a vacuum chamber to minimize contamination and ensure high-purity deposition. The vacuum environment reduces the presence of unwanted gases and particles, allowing the evaporated material to travel unimpeded to the substrate.
-
Electron Beam Source:
- A tungsten filament is heated to over 2,000°C using an electric current (5–10 kV), causing thermionic emission of electrons. These high-energy electrons are the core of the process, providing the energy required to heat and evaporate the target material.
-
Magnetic Field and Beam Focusing:
- A magnetic field is used to focus the emitted electrons into a concentrated beam. This ensures precise targeting of the electron beam onto the crucible containing the source material, maximizing energy transfer efficiency.
-
Crucible and Evaporant:
- The target material (evaporant) is placed in a water-cooled crucible, typically made of copper. The crucible is designed to withstand high temperatures while preventing contamination from the crucible material itself.
-
Energy Transfer and Evaporation:
- The focused electron beam transfers its kinetic energy to the target material upon impact, converting it into thermal energy. This heats the material to its evaporation point, causing it to transition into a gaseous phase.
-
Deposition on Substrate:
- The evaporated material disperses in the vacuum chamber and condenses onto a substrate, forming a thin film. The substrate is positioned to ensure uniform coating and adherence.
-
Applications and Advantages:
- Electron beam evaporation is used in industries requiring high-purity and precise thin films, such as semiconductors, optical coatings, and aerospace components. Its advantages include high deposition rates, excellent material utilization, and the ability to deposit a wide range of materials, including metals, ceramics, and compounds.
-
Reactive Deposition:
- Reactive gases like oxygen or nitrogen can be introduced into the vacuum chamber to deposit non-metallic films, such as oxides or nitrides. This expands the versatility of the technique for creating specialized coatings.
By understanding these key points, equipment and consumable purchasers can better evaluate the suitability of electron beam evaporation systems for their specific applications and ensure optimal performance and material selection.
Summary Table:
Key Component | Function |
---|---|
Vacuum Chamber | Minimizes contamination and ensures high-purity deposition. |
Electron Beam Source | Heats a tungsten filament to emit high-energy electrons for evaporation. |
Magnetic Field | Focuses the electron beam onto the crucible for precise energy transfer. |
Crucible | Holds the target material and withstands high temperatures. |
Substrate | Receives the evaporated material to form a uniform thin film. |
Applications | Used in semiconductors, optics, and aerospace for high-purity coatings. |
Discover how electron beam evaporation can enhance your thin-film processes—contact us today for expert guidance!