Endothermic gas, often referred to as RX® or endo gas, is a specialized gas mixture used in heat treatment processes to prevent oxidation and facilitate various metallurgical transformations. It is produced through the incomplete combustion of hydrocarbon gases in a controlled environment, resulting in a mixture of hydrogen (H₂), nitrogen (N₂), and carbon monoxide (CO). These components act as reducing agents, protecting metal surfaces from oxidation and enabling processes like carburizing, carbonitriding, neutral hardening, and bright quenching. Endothermic gas is widely used in industries requiring precise control over surface chemistry and mechanical properties of metals, such as in the treatment of carbon steel, alloy steel, stainless steel, and non-ferrous metals.
Key Points Explained:
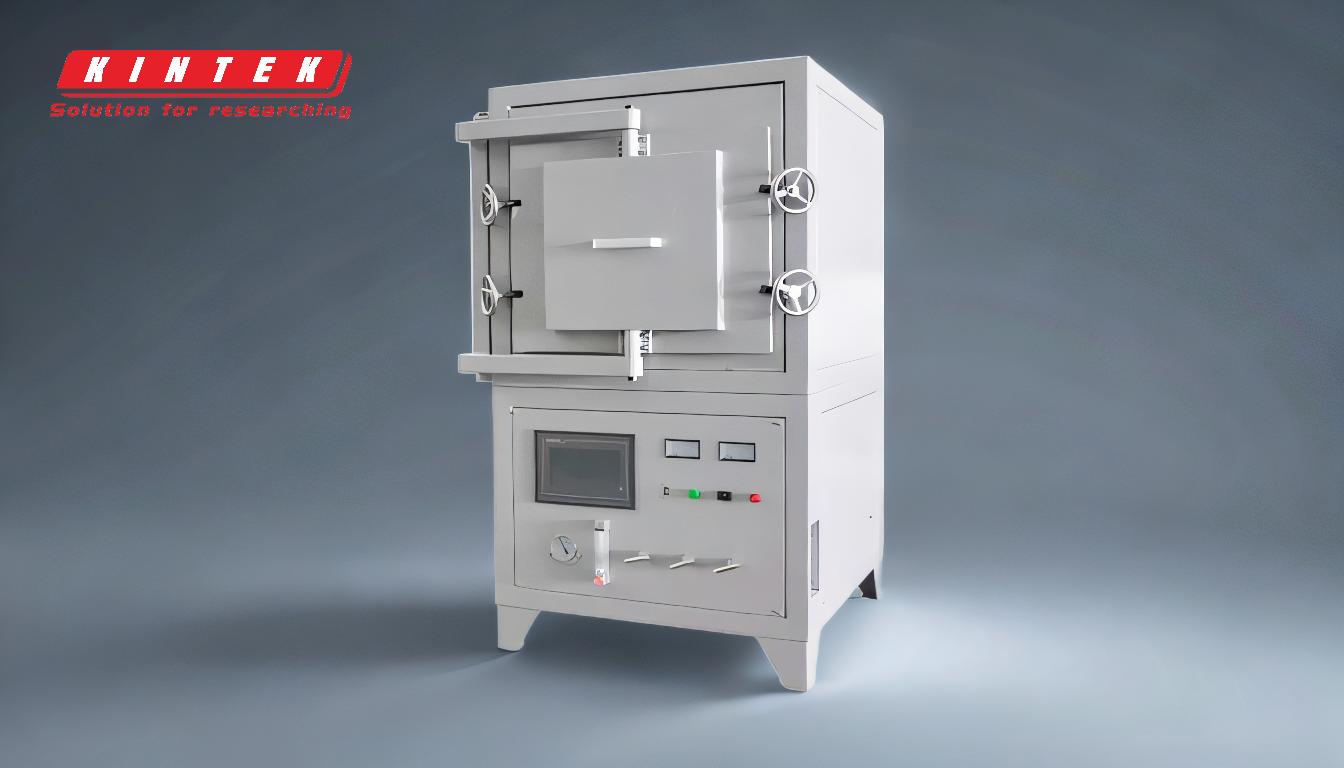
-
Composition of Endothermic Gas:
- Endothermic gas is a mixture of hydrogen (H₂), nitrogen (N₂), and carbon monoxide (CO). These gases are produced by the incomplete combustion of hydrocarbon gases like methane or propane in a controlled, oxygen-deficient environment.
- The hydrogen and carbon monoxide act as reducing agents, preventing oxidation on metal surfaces during heat treatment.
-
Primary Applications:
- Gas Carburizing: Endothermic gas serves as a carrier gas in carburizing processes, where carbon is introduced into the surface of low-carbon steels to enhance hardness and wear resistance.
- Carbonitriding: It is used as a carrier gas in carbonitriding, a process that introduces both carbon and nitrogen into the steel surface to improve hardness and fatigue resistance.
- Neutral Hardening: Endothermic gas is used in neutral hardening to prevent oxidation and decarburization, ensuring the metal retains its desired properties.
- Bright Quenching: It is employed in bright quenching processes to achieve a clean, oxide-free surface on carbon steel and low alloy structural steel.
-
Oxidation Prevention:
- The reducing nature of hydrogen and carbon monoxide in endothermic gas inhibits or reverses oxidation on metal surfaces. This is critical in processes where surface integrity and appearance are important, such as in the heat treatment of stainless steel, silicon steel, and high-chromium nickel alloys.
-
Versatility in Heat Treatment:
- Endothermic gas is suitable for a wide range of heat treatment applications, including:
- Sintering: Used in sintering processes that require a reducing atmosphere.
- Carbon Restoration: Helps restore carbon content in steel forgings that have been decarburized during prior processing.
- Annealing: Used for annealing non-ferrous metals and alloy steels to improve ductility and reduce hardness.
- Brazing: Provides a protective atmosphere during brazing to prevent oxidation and ensure strong joints.
- Endothermic gas is suitable for a wide range of heat treatment applications, including:
-
Advantages in Industrial Use:
- Surface Quality: Ensures bright, oxide-free surfaces, which are essential for applications requiring high aesthetic standards or minimal post-treatment finishing.
- Process Control: Offers precise control over surface chemistry, enabling consistent and repeatable results in heat treatment processes.
- Material Compatibility: Suitable for a wide range of materials, including carbon steel, alloy steel, stainless steel, and non-ferrous metals.
-
Production and Refinement:
- Endothermic gas is produced in endothermic generators, where hydrocarbon gases are mixed with air and passed over a catalyst at high temperatures. The resulting gas mixture is then refined to achieve the desired composition and properties.
- The gas can be further adjusted to optimize its performance for specific applications, such as reducing oxidation effects in stainless steel or enhancing carbon restoration in steel forgings.
By understanding the composition, applications, and benefits of endothermic gas, heat treatment professionals can make informed decisions about its use in various industrial processes. Its ability to prevent oxidation, enhance surface quality, and provide precise control over metallurgical transformations makes it an indispensable tool in modern heat treatment operations.
Summary Table:
Aspect | Details |
---|---|
Composition | Hydrogen (H₂), Nitrogen (N₂), Carbon Monoxide (CO) |
Primary Applications | Gas carburizing, carbonitriding, neutral hardening, bright quenching |
Key Benefits | Prevents oxidation, enhances surface quality, precise process control |
Material Compatibility | Carbon steel, alloy steel, stainless steel, non-ferrous metals |
Production | Produced via incomplete combustion of hydrocarbons in a controlled environment |
Optimize your heat treatment processes with endothermic gas—contact our experts today for tailored solutions!