Flash vacuum pyrolysis (FVP) is a rapid thermal decomposition process used to break down materials such as biomass or plastic waste into smaller molecules under high temperatures and low pressure. The process involves heating the material in a quartz or ceramic-packed tube furnace, where it is vaporized and then condensed into liquid products like bio-oil or fuel. FVP is characterized by extremely short reaction times (as low as 1 second) and high heating rates, which minimize unwanted side reactions like coke formation. The process requires precise control of parameters such as temperature, particle size, and heat transfer to optimize yields of valuable products like bio-oil, which has applications as a fuel. The mechanism relies on rapid heating and vaporization, followed by condensation, to achieve high conversion efficiency.
Key Points Explained:
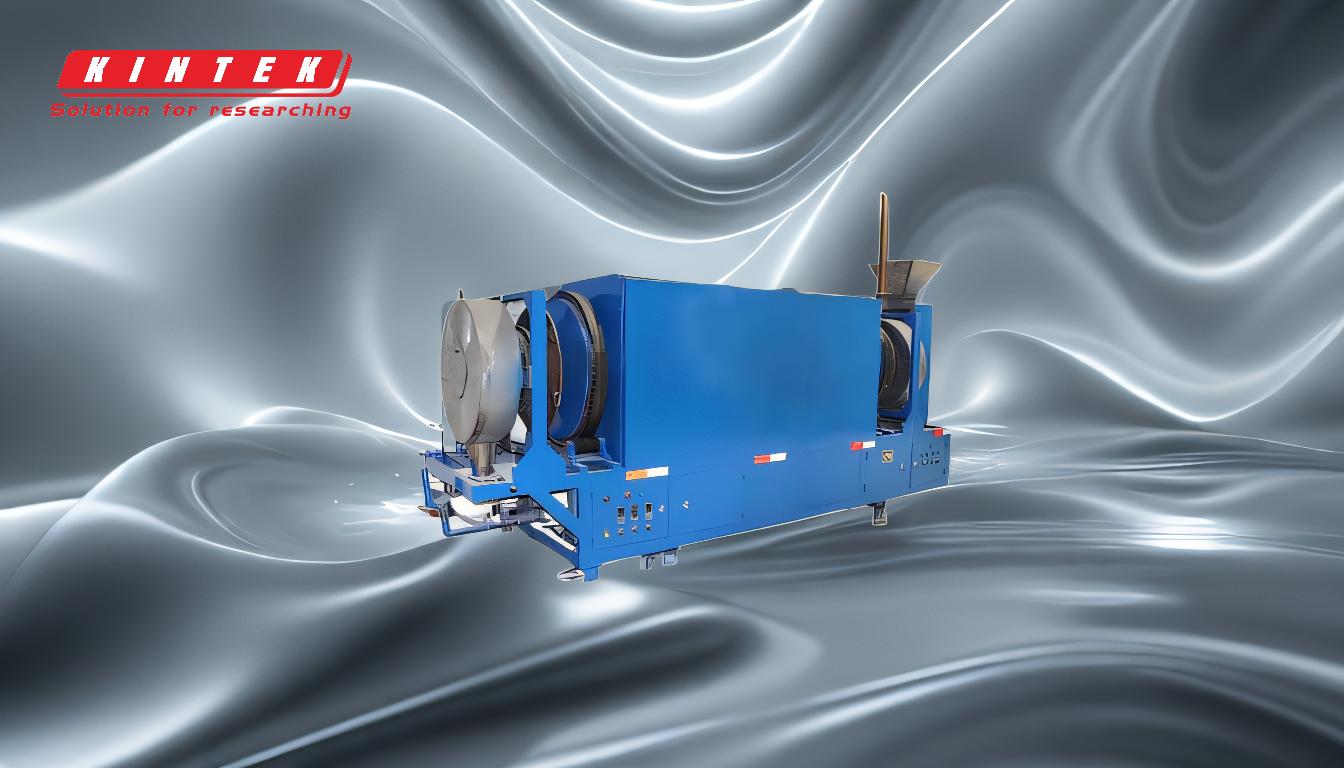
-
Definition and Purpose of Flash Vacuum Pyrolysis (FVP):
- FVP is a thermal decomposition process used to break down complex materials, such as biomass or plastic waste, into smaller molecules.
- The primary goal is to produce valuable products like bio-oil, fuel, or other chemicals through rapid heating and condensation.
-
Equipment and Setup:
- FVP typically uses a fused quartz tube packed with quartz or ceramic beads, which is heated in a tube furnace.
- The quartz tube ensures high thermal stability and resistance to extreme temperatures, while the beads provide a large surface area for efficient heat transfer.
-
Process Mechanism:
- The material (e.g., biomass or plastic) is pre-treated to remove impurities and ground to a specific size for optimal reaction.
- The material is then loaded into the pyrolysis chamber, where it is rapidly heated to temperatures between 200-900°C.
- The rapid heating causes the material to melt and vaporize almost instantly, minimizing the formation of unwanted byproducts like coke.
-
Key Parameters:
- Temperature: Optimal temperatures vary depending on the material but generally range between 200-900°C. Higher temperatures favor vaporization but must be carefully controlled to avoid excessive coke formation.
- Heating Rate: FVP involves extremely high heating rates, often achieving decomposition in as little as 1 second.
- Particle Size: Smaller particles are preferred to ensure uniform heating and minimize exposure to intermediate temperatures that promote coke formation.
-
Condensation and Product Formation:
- The vapors produced during pyrolysis are rapidly cooled and condensed into liquid products, such as bio-oil or fuel.
- Bio-oil has a caloric value about half that of diesel and can be further refined for use as a renewable fuel.
-
Advantages of FVP:
- High Efficiency: The rapid heating and short reaction times maximize the yield of valuable products like bio-oil.
- Minimized Byproducts: The process reduces the formation of coke and other unwanted byproducts by avoiding prolonged exposure to intermediate temperatures.
- Versatility: FVP can be applied to a wide range of materials, including biomass, plastics, and other organic waste.
-
Applications:
- Bio-Oil Production: FVP is widely used to produce bio-oil from biomass, which can serve as a renewable fuel source.
- Plastic Waste Conversion: The process can also be used to convert plastic waste into liquid fuels, reducing environmental pollution.
- Chemical Synthesis: FVP is employed in organic chemistry to synthesize complex molecules by breaking down larger precursors.
-
Challenges and Considerations:
- Precise Control: FVP requires careful control of temperature, heating rate, and particle size to achieve optimal results.
- Equipment Costs: The use of specialized equipment, such as quartz tubes and tube furnaces, can be expensive.
- Energy Input: The process demands significant energy input to achieve the high temperatures and heating rates required.
By understanding these key points, equipment and consumable purchasers can better evaluate the requirements and benefits of implementing flash vacuum pyrolysis in their operations. The process offers a sustainable and efficient method for converting waste materials into valuable products, provided that the necessary parameters and equipment are carefully managed.
Summary Table:
Aspect | Details |
---|---|
Process | Rapid thermal decomposition under high heat and low pressure. |
Equipment | Quartz or ceramic-packed tube furnace for high thermal stability. |
Key Parameters | Temperature (200-900°C), heating rate (1 second), and particle size control. |
Products | Bio-oil, fuel, and other chemicals. |
Advantages | High efficiency, minimized byproducts, and versatility. |
Applications | Bio-oil production, plastic waste conversion, and chemical synthesis. |
Challenges | Precise control, equipment costs, and high energy input. |
Ready to explore how FVP can transform your waste into valuable resources? Contact us today for expert guidance!