The heating element in a furnace is a critical component responsible for generating and maintaining the heat required for various processes, such as heat treatment. It ensures precise and uniform heating throughout the chamber, which is essential for achieving consistent results. Heating elements, whether electric resistance heaters or gas burners, must be of high quality and properly maintained to ensure energy efficiency, long service life, and optimal performance. Damaged or unsuitable heating elements can reduce heating efficiency and compromise the furnace's functionality. Additionally, advanced furnaces may feature multiple heating zones with independent temperature control to enhance temperature uniformity and process reliability.
Key Points Explained:
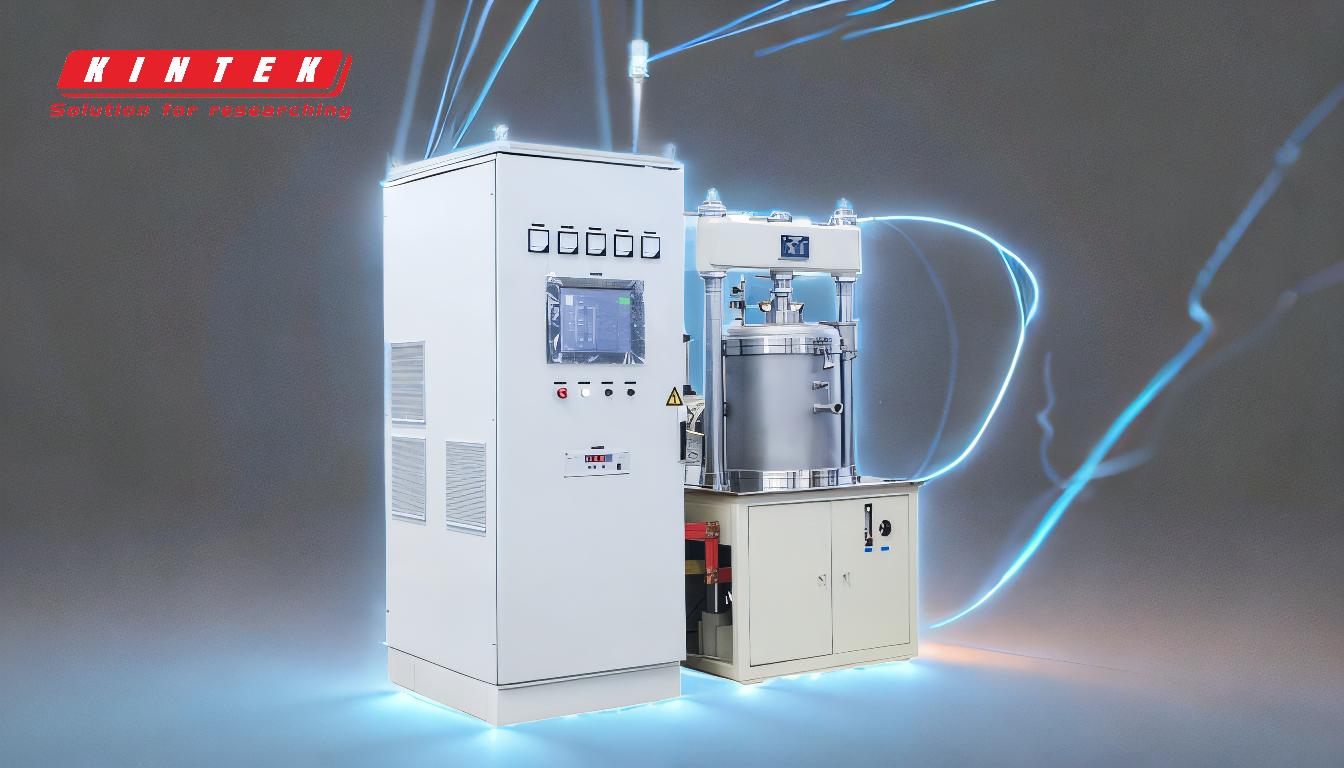
-
Function of the Heating Element:
- The primary function of the heating element is to generate heat within the furnace chamber. This heat is essential for processes like heat treatment, sintering, or annealing.
- It ensures precise and uniform heating, which is critical for maintaining consistent temperatures throughout the chamber. This uniformity is necessary to achieve the desired material properties or process outcomes.
-
Types of Heating Elements:
- Electric Resistance Heaters: These are commonly used in muffle furnaces. They convert electrical energy into heat through resistance, providing controlled and efficient heating.
- Gas Burners: These use combustion of fuel (e.g., natural gas) to generate heat. They are often used in industrial furnaces and rely on components like nozzles, mixing tubes, and air-fuel ratio controls to produce a stable and efficient flame.
-
Importance of Quality and Maintenance:
- High-quality heating elements, made from durable materials like metal or ceramic, ensure energy efficiency and a long service life. Poor-quality or aging elements can lead to reduced heating efficiency and increased operational costs.
- Regular maintenance is essential to prevent issues such as uneven heating, energy wastage, or furnace downtime. Damaged elements should be replaced promptly to maintain optimal performance.
-
Design Features for Uniform Heating:
- Advanced furnaces often incorporate multiple heating zones, each with independent temperature control. This design allows for better temperature uniformity across the chamber, which is crucial for processes requiring precise thermal conditions.
- Heating elements may be arranged in rings or on two sides of the chamber to distribute heat evenly and minimize hot or cold spots.
-
Impact on Energy Efficiency:
- Efficient heating elements reduce energy consumption and operational costs. For example, ceramic heating elements provide free heat radiation within the furnace cavity, enhancing energy efficiency.
- Proper air-fuel ratio control in gas burners ensures stable and cost-effective combustion, further improving energy efficiency.
-
Integration with Furnace Components:
- Heating elements work in conjunction with other furnace components, such as cooling chambers and loading mechanisms, to ensure seamless operation.
- In gas burners, components like nozzles and mixing tubes play a vital role in achieving efficient combustion, which directly impacts the performance of the heating element.
By understanding the function and importance of heating elements, equipment and consumable purchasers can make informed decisions about furnace selection, maintenance, and upgrades to ensure optimal performance and cost-effectiveness.
Summary Table:
Aspect | Details |
---|---|
Function | Generates and maintains heat for processes like heat treatment, sintering. |
Types | Electric resistance heaters, gas burners. |
Quality & Maintenance | High-quality materials and regular maintenance ensure efficiency and longevity. |
Design Features | Multiple heating zones, independent temperature control for uniformity. |
Energy Efficiency | Reduces energy consumption and operational costs. |
Integration | Works with cooling chambers, loading mechanisms, and combustion components. |
Upgrade your furnace's performance with high-quality heating elements—contact us today for expert advice!