The heat required for pyrolysis depends on several factors, including the type of pyrolysis (fast, slow, or flash), the biomass feedstock, and the specific energy requirements of the process. The energy needed primarily includes heating the biomass and any water content to the desired pyrolysis temperature, evaporating the water, supplying energy for the endothermic pyrolysis reaction, and compensating for heat losses. For example, in fast pyrolysis, temperatures typically range from 450–600 °C, with rapid heating rates and short residence times. Slow pyrolysis, on the other hand, operates at lower heating rates and may use external heat sources like combusted gases or char. The heat sources can include hot flue gas, combustible gases, or leftover char and biomass.
Key Points Explained:
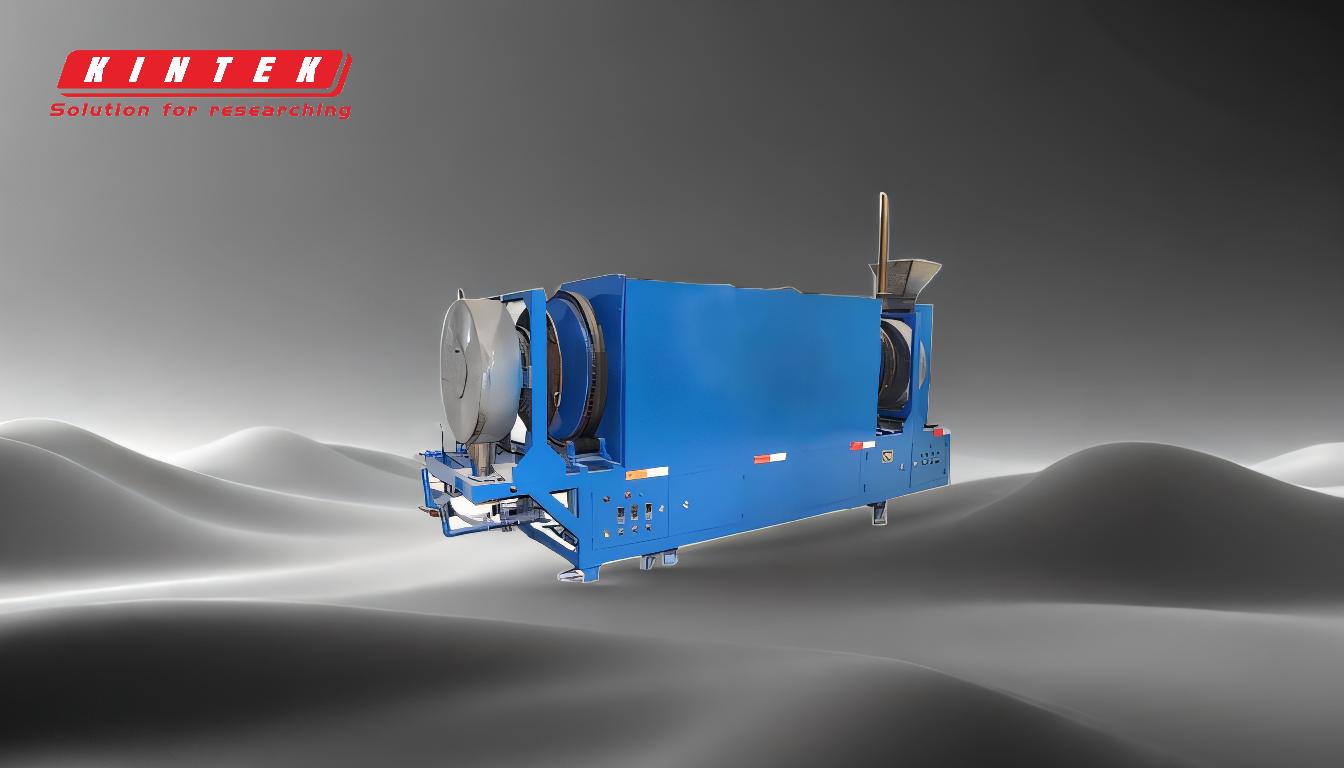
-
Types of Pyrolysis and Their Heat Requirements:
- Fast Pyrolysis: Requires temperatures between 450–600 °C, with heating rates of 10^3 to 10^4 °C/s and residence times of less than 1 second. The heat is primarily used to rapidly decompose biomass into bio-oil, gases, and char.
- Slow Pyrolysis: Operates at lower heating rates (1–30 °C/min) and typically at atmospheric pressure. The heat is supplied externally, often from the combustion of produced gases or partial combustion of biomass. This process is optimized for char production.
- Flash Pyrolysis: Similar to fast pyrolysis but with even shorter residence times and higher heating rates. The heat requirements are focused on achieving rapid thermal decomposition.
-
Energy Requirements for Pyrolysis:
-
Heating Biomass and Water: The biomass and any water content must be heated to the pyrolysis temperature (e.g., 500 °C). This includes:
- Heating the biomass from ambient temperature to 500 °C.
- Evaporating water at 100 °C (if present).
- Heating water vapor from 100 °C to 500 °C.
- Endothermic Pyrolysis Reaction: Pyrolysis is an endothermic process, meaning it requires additional energy to break down the biomass into its constituent components (bio-oil, gases, and char).
- Heat Losses: Energy is also needed to compensate for heat losses to the environment, which can vary depending on the reactor design and insulation.
-
Heating Biomass and Water: The biomass and any water content must be heated to the pyrolysis temperature (e.g., 500 °C). This includes:
-
Heat Sources for Pyrolysis:
- Hot Flue Gas: Often used to dry the biomass feedstock before pyrolysis. Combustible gases in the flue gas can be partially combusted to provide additional heat.
- Combustible Gases: Gases produced during pyrolysis (e.g., syngas) can be combusted to generate heat for the process.
- Char and Biomass Combustion: Leftover char and biomass can be burned to provide a significant portion of the required heat.
-
Temperature and Pressure Ranges:
- Pyrolysis typically occurs at temperatures between 450–1200 °C, depending on the type of pyrolysis and desired products.
- Pressure ranges from 1–30 bar, with most processes conducted at or near atmospheric pressure.
-
Reactor Design and Heat Transfer:
- Pyrolysis reactors are often designed to optimize heat transfer. For example, refractory alloy reactor tubes are used in high-temperature processes to withstand thermal stress and improve efficiency.
- Fluidized bed reactors, like those using sand as a heat carrier, enhance heat transfer by ensuring uniform temperature distribution and rapid heating of the biomass.
-
Heat Recovery and Efficiency:
- Efficient heat recovery systems can reduce the overall energy requirements by reusing heat from exhaust gases or other sources.
- Insulation and reactor design play a critical role in minimizing heat losses and improving the energy efficiency of the pyrolysis process.
By understanding these key points, a purchaser can make informed decisions about the equipment and consumables needed for pyrolysis, ensuring optimal performance and energy efficiency.
Summary Table:
Factor | Details |
---|---|
Types of Pyrolysis | Fast (450–600 °C, rapid heating), Slow (low heating rates, char-focused), Flash (ultra-fast) |
Energy Requirements | Heating biomass/water, endothermic reaction, compensating for heat losses |
Heat Sources | Hot flue gas, combustible gases, char/biomass combustion |
Temperature Range | 450–1200 °C, depending on process type |
Pressure Range | 1–30 bar, typically atmospheric pressure |
Reactor Design | Refractory alloy tubes, fluidized beds for efficient heat transfer |
Heat Recovery | Reuse heat from exhaust gases, optimize insulation for efficiency |
Ready to optimize your pyrolysis process? Contact our experts today for tailored solutions!