The heating rate of spark plasma sintering (SPS) is a critical parameter that significantly influences the microstructure and properties of the final sintered product. SPS is a rapid sintering technique that utilizes pulsed direct current (DC) to generate heat internally within the material, allowing for much faster heating rates compared to conventional sintering methods. The heating rate in SPS can range from a few degrees per minute to several hundred degrees per minute, depending on the material being sintered and the desired properties. This rapid heating is achieved through the combination of plasma heating and joule heating stages, where localized and momentary heating of particle surfaces occurs, followed by uniform heating through joule heat generated by the pulsed DC current. The ability to control the heating rate precisely is one of the key advantages of SPS, enabling the production of high-density materials with fine microstructures.
Key Points Explained:
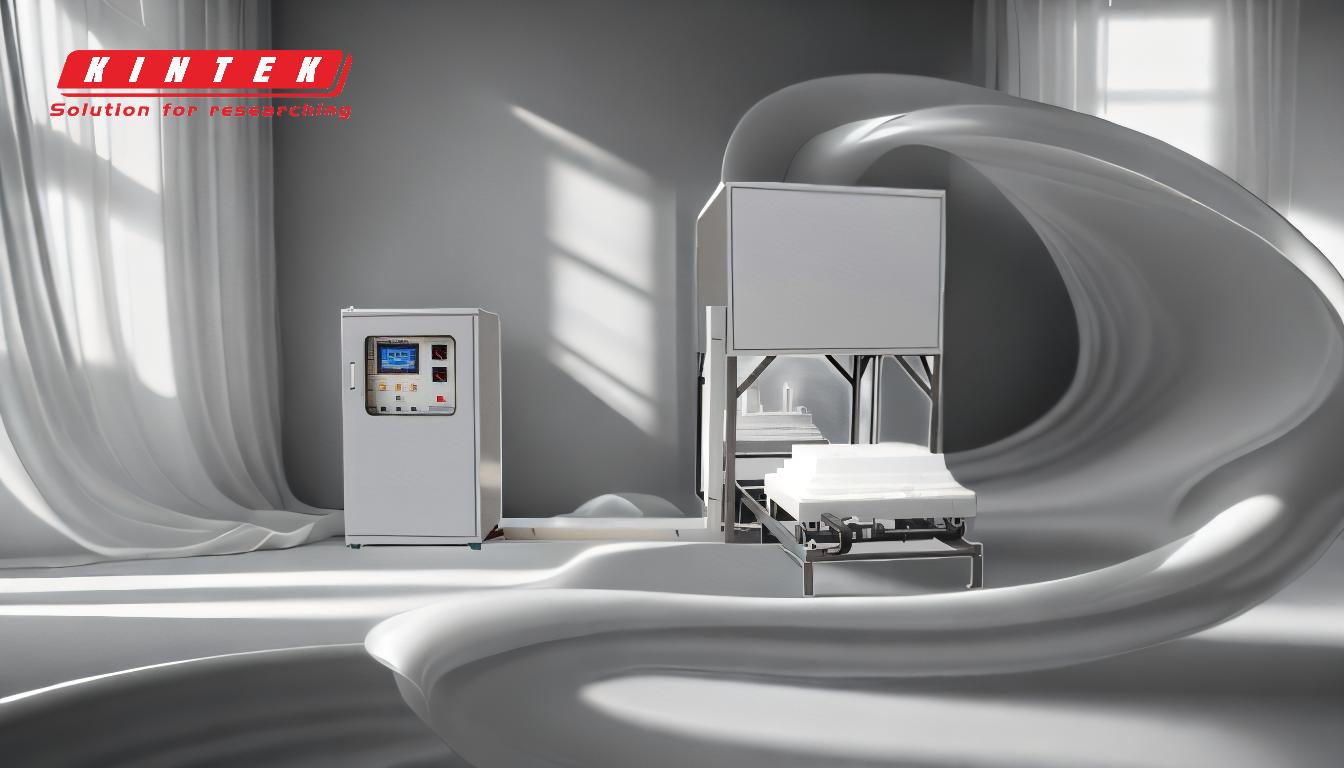
-
Heating Rate in SPS:
- The heating rate in spark plasma sintering (SPS) can vary widely, typically ranging from 50°C/min to 500°C/min or even higher, depending on the material and the desired outcome. This rapid heating is one of the distinguishing features of SPS compared to traditional sintering methods, which often have much slower heating rates.
-
Plasma Heating Stage:
- During the plasma heating stage, electrical discharge between powder particles results in localized and momentary heating of the particle surfaces up to several thousand degrees Celsius. This heating is uniformly distributed throughout the sample volume, purifying and activating the particle surfaces by vaporizing impurities. The purified surface layers melt and fuse, forming 'necks' between the particles. This stage contributes to the initial rapid heating and surface activation.
-
Joule Heating Stage:
- In the joule heating stage, a pulsed DC electrical current flows through the necks connecting the particles, generating joule heat. This heat increases the diffusion of atoms/molecules in the necks, enhancing their growth. The localized and uniform heating allows for rapid temperature rise and drop, which minimizes coarsening of the material grains. This stage is crucial for achieving high heating rates and maintaining fine microstructures.
-
Advantages of High Heating Rates:
- Minimized Grain Growth: Rapid heating rates in SPS help to minimize grain growth, which is beneficial for maintaining fine microstructures and enhancing mechanical properties such as strength and toughness.
- Reduced Processing Time: The ability to achieve high heating rates significantly reduces the overall processing time, making SPS a more efficient sintering method compared to conventional techniques.
- Improved Densification: The combination of plasma and joule heating stages promotes rapid densification, leading to high-density materials with minimal porosity.
-
Factors Influencing Heating Rate:
- Material Properties: The thermal conductivity, electrical conductivity, and melting point of the material being sintered can influence the achievable heating rate.
- Sample Size and Geometry: Larger or more complex samples may require adjustments in heating rate to ensure uniform heating and avoid thermal gradients.
- Equipment Capabilities: The design and power of the SPS equipment, including the ability to deliver high-current pulses, play a critical role in determining the maximum heating rate.
-
Applications of SPS with High Heating Rates:
- Advanced Ceramics: SPS is widely used for sintering advanced ceramics, where rapid heating rates help to achieve fine-grained microstructures and high densities.
- Metallic Alloys: High heating rates are beneficial for sintering metallic alloys, particularly those that require fine microstructures for enhanced mechanical properties.
- Composite Materials: SPS is also used for sintering composite materials, where the rapid heating rates help to maintain the integrity of the different phases within the composite.
In summary, the heating rate in spark plasma sintering is a key parameter that can be precisely controlled to achieve rapid densification and fine microstructures. The combination of plasma heating and joule heating stages allows for high heating rates, which offer several advantages, including minimized grain growth, reduced processing time, and improved densification. The ability to achieve high heating rates makes SPS a powerful tool for sintering a wide range of materials, from advanced ceramics to metallic alloys and composites.
Summary Table:
Aspect | Details |
---|---|
Heating Rate Range | 50°C/min to 500°C/min or higher, depending on material and desired outcome |
Plasma Heating Stage | Localized heating up to thousands of °C, purifies and activates surfaces |
Joule Heating Stage | Pulsed DC current generates uniform heat, minimizing grain growth |
Key Advantages | Minimized grain growth, reduced processing time, improved densification |
Applications | Advanced ceramics, metallic alloys, composite materials |
Ready to optimize your sintering process with SPS? Contact us today to learn more!