The interior of a kiln is typically constructed using materials that can withstand extremely high temperatures and provide excellent thermal insulation. These materials are chosen based on their ability to resist heat, maintain structural integrity, and ensure efficient heat distribution. Common materials include refractory bricks, ceramic fiber, and insulating firebricks, which are designed to endure the intense heat generated during firing processes. The choice of material depends on the type of kiln, its intended use, and the temperature range it operates in. Below, we explore the key materials used in kiln interiors and their properties in detail.
Key Points Explained:
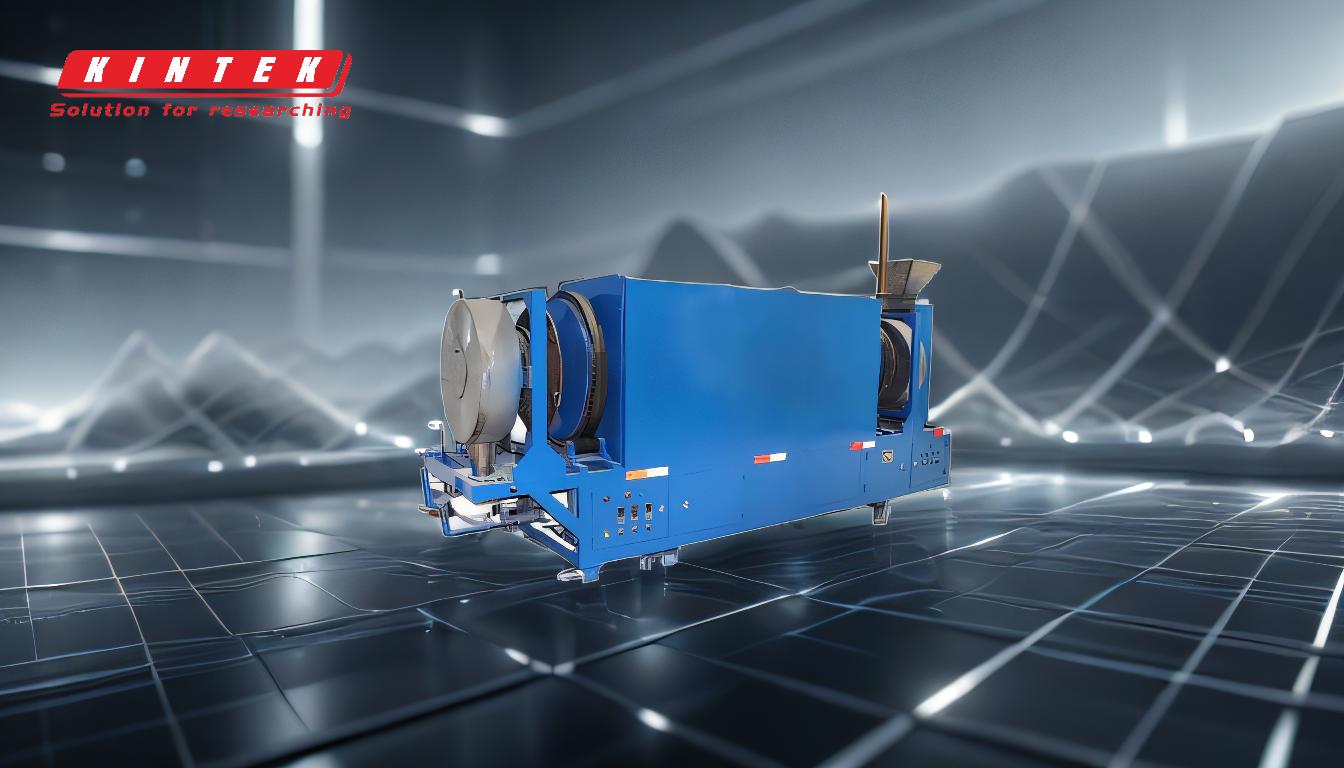
-
Refractory Bricks:
- Refractory bricks are the most common material used in kiln interiors due to their high heat resistance and durability.
- They are made from refractory ceramics, such as alumina, silica, and fireclay, which can withstand temperatures exceeding 2000°F (1093°C).
- These bricks are dense and provide excellent thermal insulation, ensuring that heat is retained within the kiln.
- They are often used in kilns for pottery, ceramics, and metalworking, where consistent high temperatures are required.
-
Ceramic Fiber:
- Ceramic fiber is a lightweight, flexible material made from alumina-silica fibers.
- It is used in kiln interiors for its superior insulating properties and ability to withstand rapid temperature changes.
- Ceramic fiber is often used in modern kilns, especially those designed for quick heating and cooling cycles, such as glass kilns or small pottery kilns.
- Its lightweight nature reduces the overall weight of the kiln, making it easier to handle and install.
-
Insulating Firebricks:
- Insulating firebricks are a type of refractory brick designed to provide both heat resistance and thermal insulation.
- They are less dense than standard refractory bricks, which makes them more efficient at reducing heat loss.
- These bricks are ideal for kilns that require energy efficiency, as they help maintain high temperatures with less energy consumption.
- They are commonly used in electric kilns and smaller industrial kilns.
-
Kiln Wash and Coatings:
- The interior of a kiln may also be coated with a kiln wash or protective coating to prevent damage from molten materials or glaze drips.
- Kiln wash is typically made from refractory materials like alumina hydrate and kaolin, which create a protective barrier on the kiln's interior surfaces.
- Coatings are especially important in glass kilns, where molten glass can stick to and damage the kiln lining.
-
Material Selection Based on Kiln Type:
- The choice of interior materials depends on the type of kiln and its intended use.
- Pottery Kilns: Often use refractory bricks or insulating firebricks due to their ability to withstand high temperatures and provide even heat distribution.
- Glass Kilns: May use ceramic fiber or specialized coatings to handle rapid temperature changes and prevent glass from sticking.
- Industrial Kilns: Typically use dense refractory bricks for their durability and ability to handle extreme temperatures over long periods.
- The choice of interior materials depends on the type of kiln and its intended use.
-
Thermal Efficiency and Durability:
- The materials used in the interior of a kiln are selected not only for their heat resistance but also for their ability to enhance thermal efficiency.
- Efficient insulation reduces energy consumption and ensures consistent temperatures throughout the kiln.
- Durability is also a key factor, as the materials must withstand repeated heating and cooling cycles without degrading.
-
Maintenance and Longevity:
- Proper maintenance of the kiln interior is essential to ensure its longevity.
- Regular inspection for cracks, wear, or damage to the refractory lining is necessary to prevent heat loss and maintain performance.
- Replacing worn or damaged materials promptly can extend the life of the kiln and improve its efficiency.
In summary, the interior of a kiln is made from specialized materials like refractory bricks, ceramic fiber, and insulating firebricks, chosen for their ability to withstand high temperatures and provide efficient insulation. The specific materials used depend on the type of kiln and its intended application, with considerations for thermal efficiency, durability, and maintenance playing a crucial role in material selection.
Summary Table:
Material | Properties | Common Applications |
---|---|---|
Refractory Bricks | High heat resistance, durability, excellent thermal insulation | Pottery, ceramics, metalworking |
Ceramic Fiber | Lightweight, flexible, superior insulation, withstands rapid temperature changes | Glass kilns, small pottery kilns |
Insulating Firebricks | Heat resistance, thermal insulation, energy-efficient | Electric kilns, smaller industrial kilns |
Kiln Wash/Coatings | Protective barrier against molten materials, prevents damage | Glass kilns |
Need help selecting the right materials for your kiln? Contact our experts today for personalized advice!