The Selective Laser Sintering (SLS) process, while highly effective for producing complex geometries and functional prototypes, has several limitations. These include material constraints, such as the limited range of materials that can be used effectively, and issues related to the mechanical, thermal, and electrical properties of the final products. For instance, Polyamide 11 (PA11), a commonly used material in SLS, exhibits poor thermal, electrical, and flame-retardant properties, which can restrict its application in certain industries. Additionally, the SLS process faces challenges related to surface finish, dimensional accuracy, and post-processing requirements, which can impact the overall efficiency and cost-effectiveness of the process.
Key Points Explained:
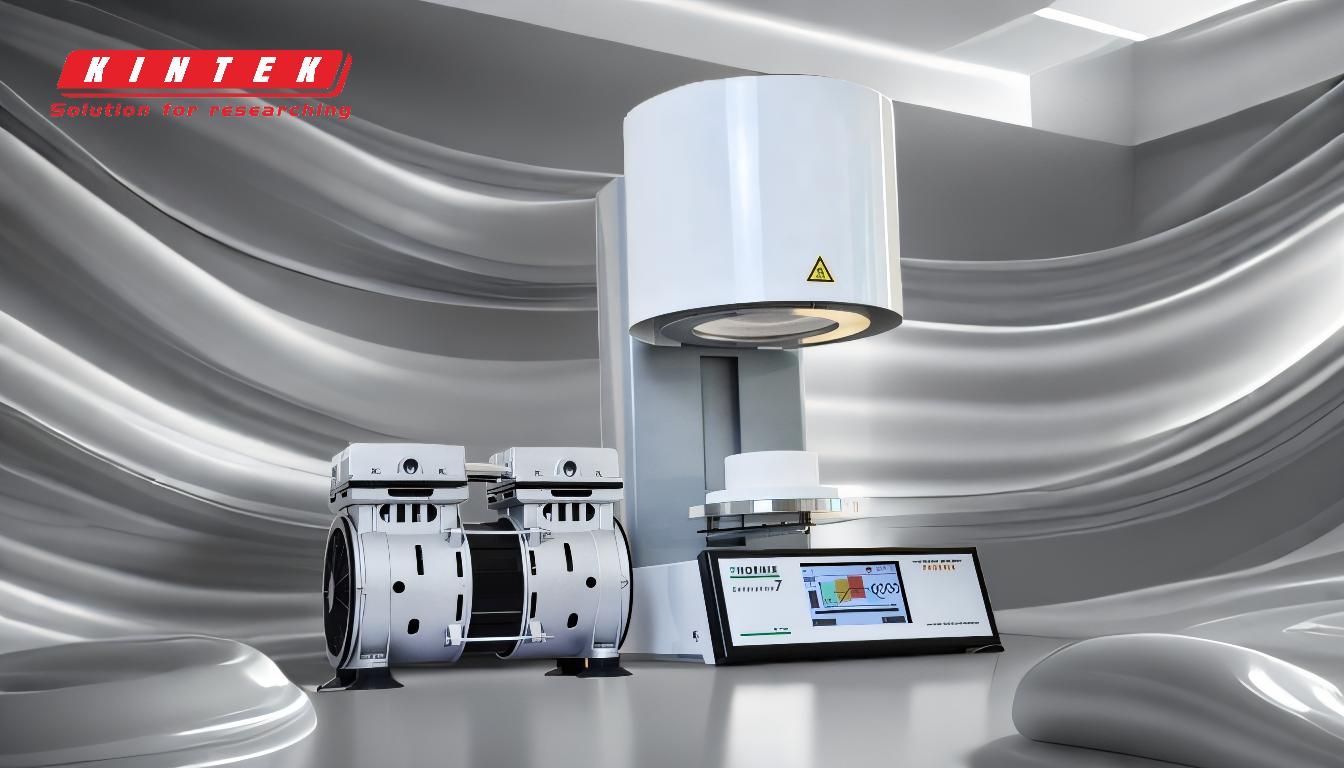
-
Material Limitations:
- Thermal Properties: Polyamide 11 (PA11), a common material used in SLS, has poor thermal properties. This limits its use in applications where high thermal resistance is required.
- Electrical Properties: PA11 also exhibits poor electrical properties, making it unsuitable for applications that require electrical insulation or conductivity.
- Flame-Retardant Properties: The lack of flame-retardant properties in PA11 can be a significant drawback for industries that require materials to meet specific fire safety standards.
-
Surface Finish and Dimensional Accuracy:
- Surface Roughness: Parts produced using SLS often have a rough surface finish, which may require additional post-processing to achieve the desired smoothness.
- Dimensional Accuracy: Achieving high dimensional accuracy can be challenging with SLS, especially for complex geometries. This can lead to parts that do not meet tight tolerances without further machining or finishing.
-
Post-Processing Requirements:
- Support Structures: Unlike some other additive manufacturing processes, SLS does not require support structures during printing. However, post-processing steps such as powder removal and surface finishing can be labor-intensive and time-consuming.
- Material Removal: Excess powder must be carefully removed from the printed parts, which can be a delicate and time-consuming process, especially for intricate designs.
-
Cost and Efficiency:
- Material Costs: The cost of materials used in SLS, such as PA11, can be relatively high, impacting the overall cost-effectiveness of the process.
- Machine Costs: SLS machines are generally expensive, and the process can be slower compared to other additive manufacturing techniques, affecting production efficiency.
-
Environmental and Safety Concerns:
- Powder Handling: The handling of fine powders used in SLS can pose health and safety risks, requiring proper ventilation and protective measures.
- Waste Management: The process generates waste powder that must be managed and disposed of properly, adding to the environmental impact.
In summary, while the SLS process offers significant advantages in terms of design flexibility and the ability to produce complex parts, it is important to consider its limitations, particularly in terms of material properties, surface finish, dimensional accuracy, and post-processing requirements. These factors can influence the suitability of SLS for specific applications and industries.
Summary Table:
Limitation | Details |
---|---|
Material Limitations | - Poor thermal, electrical, and flame-retardant properties of PA11 |
Surface Finish | - Rough surface finish requiring additional post-processing |
Dimensional Accuracy | - Challenges in achieving tight tolerances for complex geometries |
Post-Processing Requirements | - Labor-intensive powder removal and surface finishing |
Cost and Efficiency | - High material and machine costs, slower production |
Environmental and Safety | - Health risks from powder handling, waste management challenges |
Need help overcoming SLS limitations? Contact our experts today to find the best solutions for your needs!