Magnetron sputtering is a highly efficient physical vapor deposition (PVD) technique used to deposit thin films onto substrates. It operates by ionizing a target material in a vacuum chamber using a magnetic field to generate plasma. The plasma ionizes the target material, causing it to sputter or vaporize and deposit onto the substrate. This method is widely used in industries for applications such as optical coatings, semiconductor devices, and protective coatings due to its ability to produce high-quality, uniform thin films at relatively low temperatures. The process involves the use of inert gases like argon, and it can be adapted for various materials, including metals, alloys, and insulators, by employing different power sources such as DC, AC, or RF magnetron sources.
Key Points Explained:
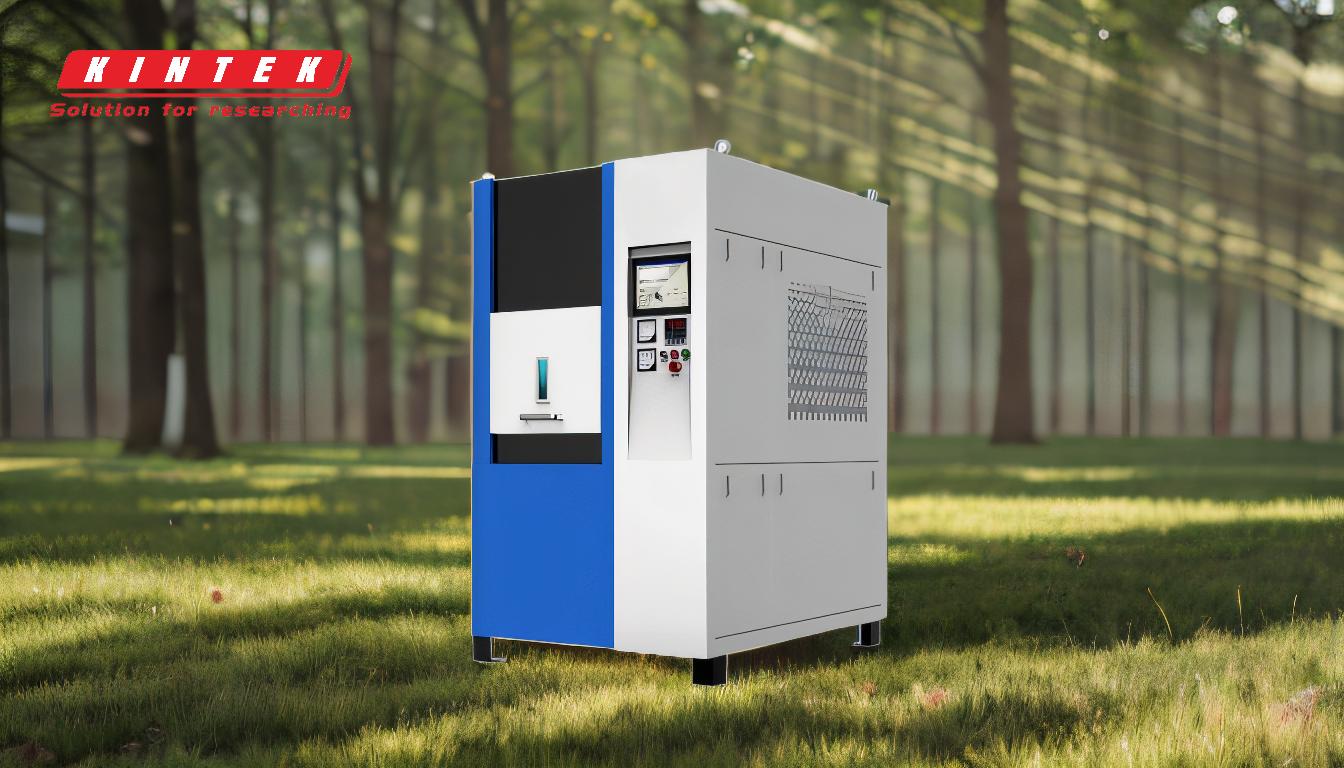
-
Basic Principle of Magnetron Sputtering:
- Magnetron sputtering is a PVD technique where a target material is ionized in a vacuum chamber using a magnetic field to generate plasma.
- The plasma ionizes the target material, causing it to sputter or vaporize and deposit onto a substrate.
-
Role of Magnetic and Electric Fields:
- The technique uses powerful magnets to confine plasma electrons close to the target surface, increasing the efficiency of ionizing collisions with gaseous neutrals.
- This confinement allows the plasma to be sustained at lower pressures and results in a higher deposition rate.
-
Use of Inert Gases:
- Inert gases like argon are commonly used in magnetron sputtering. Argon ions are created in the plasma, which then bombard the target material, causing it to sputter.
- The use of inert gases helps in creating a stable plasma environment and prevents unwanted chemical reactions.
-
Types of Magnetron Sputtering:
- DC Magnetron Sputtering: Uses direct current to generate the plasma. Suitable for conductive materials.
- RF Magnetron Sputtering: Uses radio frequency to avoid charge build-up on insulating targets. Commonly used for non-conductive materials.
- Reactive Sputtering: Involves the introduction of a reactive gas (like oxygen or nitrogen) to form compound films (e.g., oxides, nitrides).
- HIPIMS (High-Power Impulse Magnetron Sputtering): Uses short, high-power pulses to achieve high ionization of the sputtered material, leading to better film quality and adhesion.
-
Advantages of Magnetron Sputtering:
- High Deposition Rates: The magnetic confinement of electrons increases the ionization efficiency, leading to faster deposition rates.
- Low Substrate Temperature: The process can be carried out at relatively low temperatures, making it suitable for temperature-sensitive substrates.
- Uniform Coatings: The technique produces highly uniform and dense thin films, which are essential for applications in optics, electronics, and protective coatings.
- Versatility: Can be used to deposit a wide range of materials, including metals, alloys, and insulators.
-
Applications of Magnetron Sputtering:
- Optical Coatings: Used to create anti-reflective, reflective, and transparent conductive coatings for lenses, mirrors, and displays.
- Semiconductor Devices: Essential for depositing thin films in the fabrication of integrated circuits, sensors, and solar cells.
- Protective Coatings: Applied to tools, medical devices, and automotive components to enhance durability and resistance to wear and corrosion.
- Architectural Glass: Used in large-scale industrial installations to coat glass with energy-efficient and aesthetically pleasing layers.
-
Equipment and Configurations:
- In-line Systems: Substrates travel past the target material on a conveyor belt, suitable for large-scale production.
- Circular Systems: Designed for smaller applications, where substrates are placed in a circular arrangement around the target.
- Bench-top Units: Small-scale systems used for coating samples in research and development settings.
-
Comparison with Other Thin Film Deposition Techniques:
- Chemical Vapour Deposition (CVD): Involves chemical reactions to deposit thin films, often requiring higher temperatures compared to PVD.
- Atomic Layer Deposition (ALD): Deposits films one atomic layer at a time, offering excellent control over film thickness and composition but at slower deposition rates.
- Spray Pyrolysis: Involves spraying a material solution onto the substrate and thermally degrading it to form a thin layer, less precise compared to PVD techniques.
In summary, magnetron sputtering is a versatile and efficient technique for depositing thin films with high precision and uniformity. Its ability to operate at lower temperatures and its adaptability to various materials make it a preferred choice in many industrial and research applications.
Summary Table:
Aspect | Details |
---|---|
Basic Principle | Ionizes target material in a vacuum chamber using a magnetic field. |
Key Components | Magnetic field, inert gases (e.g., argon), and power sources (DC, RF, etc.). |
Types | DC, RF, Reactive, HIPIMS. |
Advantages | High deposition rates, low substrate temperature, uniform coatings. |
Applications | Optical coatings, semiconductor devices, protective coatings, architectural glass. |
Comparison with Others | More efficient than CVD and ALD, precise compared to spray pyrolysis. |
Discover how magnetron sputtering can enhance your thin film processes—contact us today!