The ashing method is a fundamental analytical technique used in chemistry to determine the composition of a sample by heating it to remove organic materials, leaving behind inorganic ash. This process is widely applied in fields like soil analysis, food science, and material testing to measure organic content, mineral composition, or impurities. Ashing involves heating samples in air or controlled environments, often following standardized procedures like ISO, ASTM, or EN. Techniques include dry ashing, wet ashing, and low-temperature ashing, each suited for specific sample types and analytical goals. The residual ash is then analyzed to provide insights into the sample's elemental or mineral composition.
Key Points Explained:
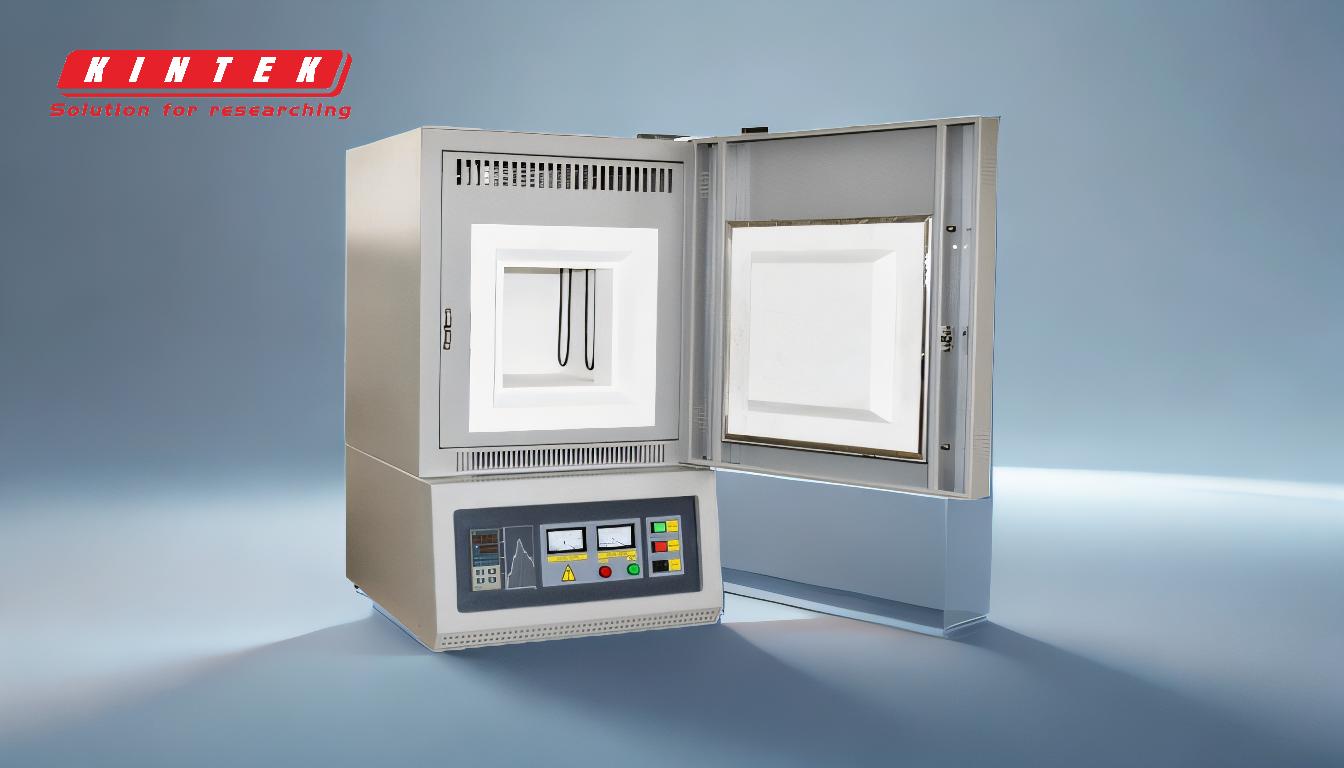
1. Definition and Purpose of Ashing
- Ashing is a process where a sample is heated to high temperatures to remove organic matter, leaving behind inorganic, non-combustible ash.
- It is used to determine the composition of materials, such as organic content in soil, mineral content in food, or impurities in industrial samples.
- The residual ash can be analyzed for elemental or mineral composition, aiding in quality control, research, and regulatory compliance.
2. Types of Ashing Techniques
-
Dry Ashing:
- Involves heating samples in a muffle furnace at temperatures between 500-600°C.
- Organic matter is oxidized, producing gases like carbon dioxide and water vapor, while inorganic compounds remain as ash.
- Commonly used for soil, food, and plant samples.
-
Wet Ashing:
- Uses strong acids (e.g., nitric or sulfuric acid) at lower temperatures to oxidize organic matter.
- Suitable for samples that may degrade at high temperatures or require specific chemical treatments.
-
Low-Temperature Ashing:
- Conducted at around 200°C using plasma or controlled atmospheres.
- Ideal for heat-sensitive samples that might lose volatile components at higher temperatures.
-
Sulfated Ashing:
- Involves adding sulfuric acid to neutralize sulfur dioxide and convert sulfates into ash.
- Used for samples containing sulfur compounds.
-
Closed System Ashing:
- Performed in airtight chambers to control the atmosphere and prevent contamination.
- Ensures precise results for sensitive analyses.
3. Process of Ashing
-
Sample Preparation:
- Samples are dried and weighed to determine the initial mass (M(dry)).
-
Heating:
- Samples are heated in air or a controlled environment until organic matter combusts.
- The temperature and duration depend on the sample type and ashing technique.
-
Cooling and Weighing:
- After heating, the sample is cooled in a desiccator to prevent moisture absorption.
- The residual ash is weighed (M(ash)) to calculate the ash content.
-
Calculation:
- Ash content is calculated using the formula:
[ \text{Ash content (%)} = \frac{M(\text{ash})}{M(\text{dry})} \times 100 ]
- Ash content is calculated using the formula:
4. Applications of Ashing
-
Soil Analysis:
- Determines the organic content by measuring mass loss after ashing (Loss on Ignition, LOI).
-
Food Science:
- Measures mineral content in food products, such as ash in flour or milk.
-
Material Testing:
- Assesses the purity or composition of industrial materials, such as polymers or ceramics.
-
Environmental Studies:
- Analyzes organic and inorganic components in environmental samples like water or sediments.
5. Standards and Quality Control
- Ashing processes are often governed by international standards such as ISO, ASTM, or EN.
- These standards ensure consistency, accuracy, and reproducibility in results.
- Quality control measures include:
- Calibrating equipment (e.g., muffle furnaces, balances).
- Using certified reference materials for validation.
- Maintaining controlled heating rates and temperatures.
6. Advantages and Limitations
-
Advantages:
- Simple and cost-effective method for determining organic and inorganic content.
- Suitable for a wide range of sample types.
- Provides accurate results when performed under controlled conditions.
-
Limitations:
- High temperatures in dry ashing may cause loss of volatile elements.
- Wet ashing requires hazardous chemicals and careful handling.
- Low-temperature ashing may be time-consuming and require specialized equipment.
7. Practical Considerations for Equipment and Consumables
-
Equipment:
- Muffle furnaces for dry ashing.
- Plasma ashers for low-temperature ashing.
- Acid digestion systems for wet ashing.
-
Consumables:
- Crucibles (e.g., porcelain, quartz, or platinum) for holding samples.
- Desiccators for cooling samples.
- Acids and reagents for wet ashing.
-
Safety:
- Proper ventilation and protective gear are essential when handling high temperatures or corrosive chemicals.
- Regular maintenance of equipment to ensure accurate and safe operation.
By understanding the ashing method and its various techniques, purchasers can select the appropriate equipment and consumables for their specific analytical needs, ensuring reliable and accurate results.
Summary Table:
Aspect | Details |
---|---|
Purpose | Determines organic and inorganic content in samples. |
Techniques | Dry ashing, wet ashing, low-temperature ashing, sulfated ashing, closed system ashing. |
Applications | Soil analysis, food science, material testing, environmental studies. |
Standards | ISO, ASTM, EN for consistent and accurate results. |
Equipment | Muffle furnaces, plasma ashers, acid digestion systems. |
Advantages | Simple, cost-effective, and suitable for a wide range of samples. |
Limitations | Potential loss of volatile elements, hazardous chemicals, specialized equipment required. |
Need help selecting the right ashing equipment for your lab? Contact us today for expert guidance!