Heat treatment of steel involves controlled heating and cooling processes to alter its physical and mechanical properties, such as hardness, strength, ductility, and toughness. The primary methods include annealing, hardening, tempering, normalizing, case hardening, and quenching. Each method follows a specific sequence of heating to a precise temperature, holding at that temperature for a set duration, and cooling under controlled conditions. These processes are tailored to achieve desired material characteristics for specific applications, such as improving machinability, enhancing wear resistance, or reducing internal stresses.
Key Points Explained:
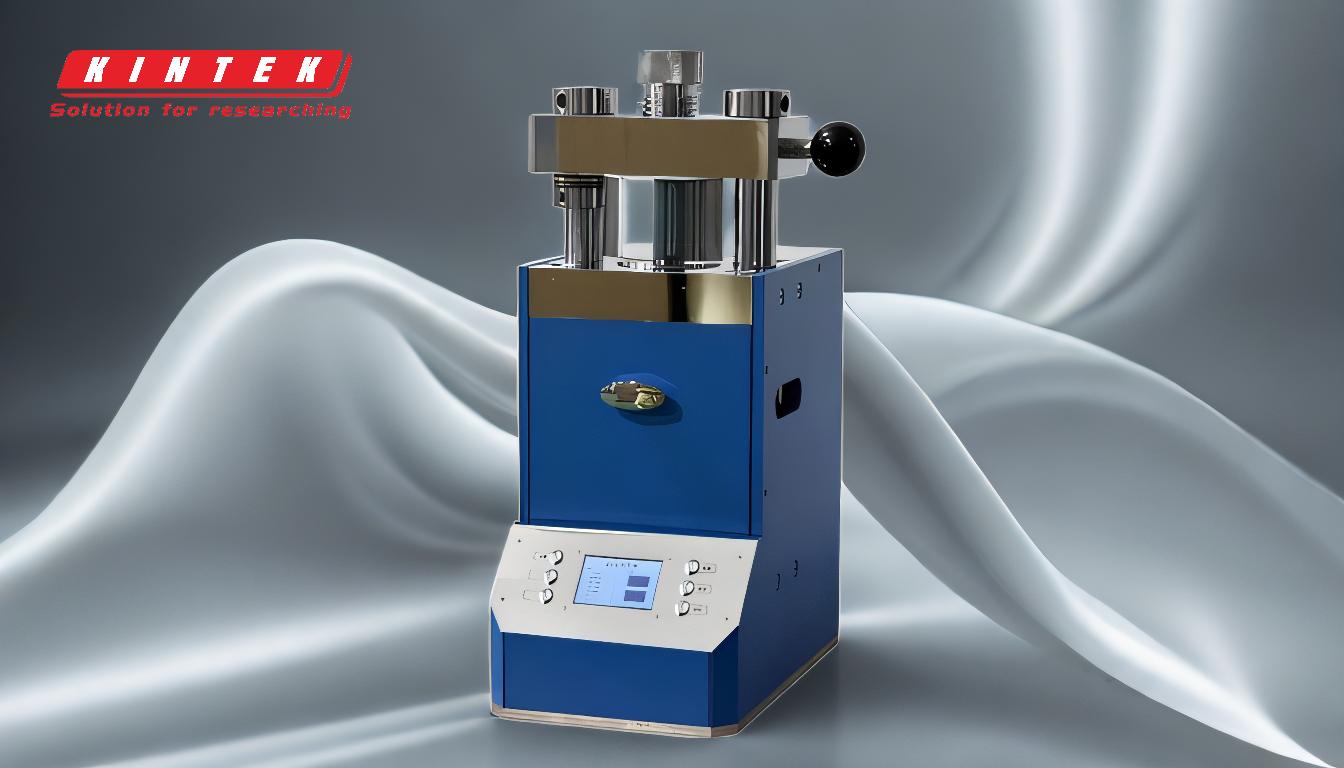
-
Basic Steps of Heat Treatment:
- Heating: The steel is heated to a specific temperature, which can range from a few hundred degrees to as high as 2,400°F, depending on the desired outcome.
- Holding: The material is maintained at the target temperature for a set period, which can vary from seconds to several hours, to ensure uniform heat distribution and structural changes.
- Cooling: The steel is cooled using prescribed methods, such as air cooling, oil quenching, or water quenching, to achieve the desired properties.
-
Common Heat Treatment Methods:
-
Annealing:
- Purpose: To soften the steel, improve machinability, and relieve internal stresses.
- Process: The steel is heated to a temperature above its critical range, held, and then slowly cooled, often in a furnace.
- Outcome: Increased ductility and reduced hardness.
-
Hardening (Through Hardening):
- Purpose: To increase the hardness and strength of the steel.
- Process: The steel is heated to a high temperature and then rapidly cooled (quenched) in water, oil, or air.
- Outcome: High hardness but reduced ductility.
-
Tempering:
- Purpose: To reduce brittleness and improve toughness after hardening.
- Process: The hardened steel is reheated to a temperature below its critical range and then cooled.
- Outcome: Balanced hardness and toughness.
-
Normalizing:
- Purpose: To refine the grain structure and improve mechanical properties.
- Process: The steel is heated above its critical temperature and then air-cooled.
- Outcome: Uniform microstructure and improved strength.
-
Case Hardening (Surface Hardening):
- Purpose: To harden the surface while maintaining a tough core.
- Process: Methods like carburizing, nitriding, or induction hardening are used to introduce carbon or nitrogen into the surface layer.
- Outcome: A hard, wear-resistant surface with a ductile core.
-
Quenching:
- Purpose: To rapidly cool the steel to achieve high hardness.
- Process: The steel is heated and then immersed in a quenching medium (water, oil, or air).
- Outcome: High hardness but potential brittleness, often followed by tempering.
-
Precipitation Hardening:
- Purpose: To increase strength by forming fine precipitates within the steel.
- Process: The steel is heated to a specific temperature, held, and then cooled to allow precipitates to form.
- Outcome: Enhanced strength and hardness without significant loss of ductility.
-
Annealing:
-
Applications of Heat Treatment:
- Annealing: Used for improving machinability and reducing internal stresses in parts that will undergo further processing.
- Hardening and Tempering: Applied to tools, gears, and structural components requiring high strength and wear resistance.
- Case Hardening: Ideal for components like gears and shafts that need a hard surface for wear resistance and a tough core for impact resistance.
- Normalizing: Commonly used to prepare steel for further processing or to achieve a uniform microstructure.
- Quenching: Essential for achieving high hardness in cutting tools and other wear-resistant components.
-
Factors Influencing Heat Treatment:
- Material Composition: The specific alloying elements in the steel determine the appropriate heat treatment method and parameters.
- Temperature and Time: Precise control of heating and cooling rates is critical to achieving the desired properties.
- Cooling Medium: The choice of quenching medium (water, oil, air) affects the cooling rate and final properties of the steel.
By understanding these methods and their applications, manufacturers can tailor the heat treatment process to achieve the optimal balance of properties for specific steel components.
Summary Table:
Method | Purpose | Process | Outcome |
---|---|---|---|
Annealing | Soften steel, improve machinability, relieve stress | Heat above critical range, hold, slow cool in furnace | Increased ductility, reduced hardness |
Hardening | Increase hardness and strength | Heat to high temperature, rapidly cool (quench in water, oil, or air) | High hardness, reduced ductility |
Tempering | Reduce brittleness, improve toughness | Reheat hardened steel below critical range, cool | Balanced hardness and toughness |
Normalizing | Refine grain structure, improve properties | Heat above critical temperature, air-cool | Uniform microstructure, improved strength |
Case Hardening | Harden surface, maintain tough core | Introduce carbon/nitrogen via carburizing, nitriding, or induction hardening | Hard surface, ductile core |
Quenching | Achieve high hardness | Heat, immerse in quenching medium (water, oil, air) | High hardness, potential brittleness |
Precipitation Hardening | Increase strength via fine precipitates | Heat, hold, cool to form precipitates | Enhanced strength, minimal ductility loss |
Discover how heat treatment can optimize your steel components—contact our experts today!