The minimum melting temperature for brazing material is a critical factor in determining the success of the brazing process. Brazing involves joining metal parts using a filler metal that melts at a temperature above 450°C (842°F) but below the melting point of the base metals being joined. The dwell temperature and time are essential parameters that influence the quality of the brazed joint. The filler metal must melt and flow properly to form a strong bond, and the temperature must be carefully controlled to avoid damaging the base materials.
Key Points Explained:
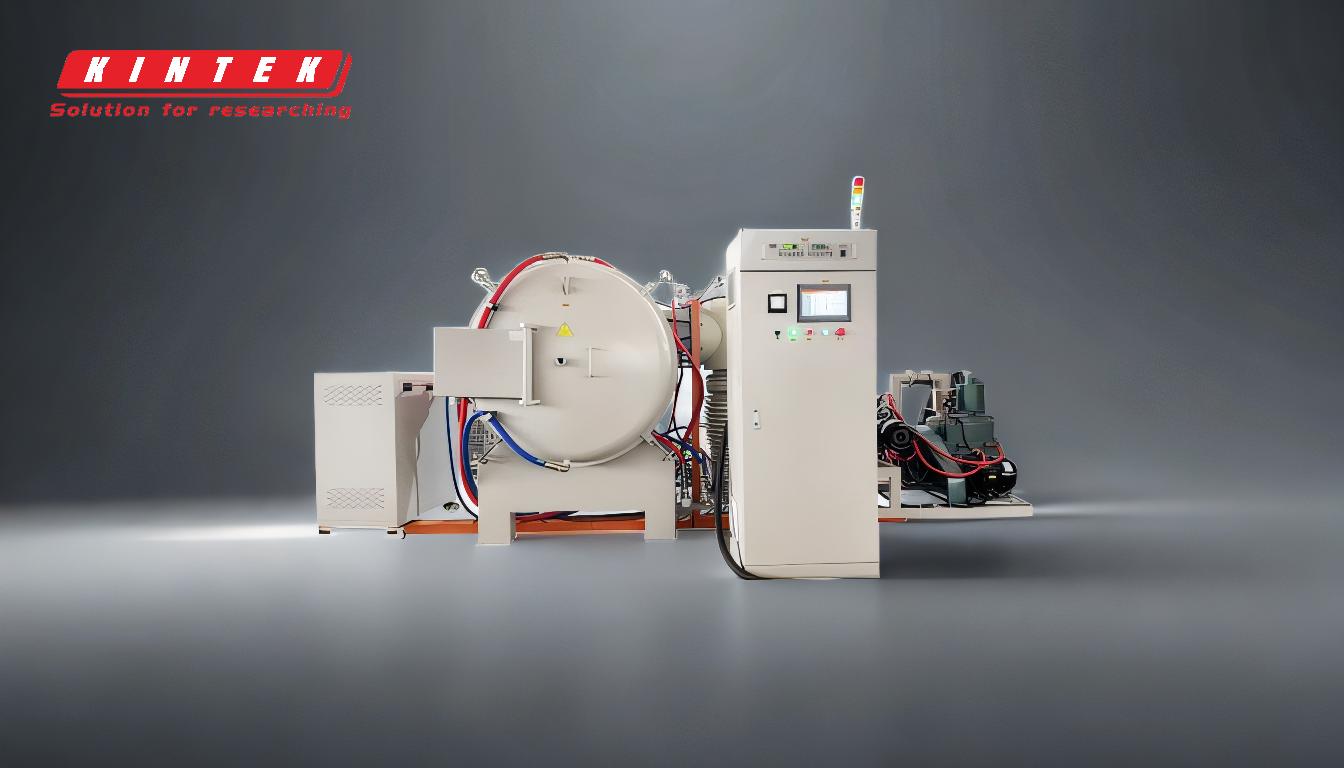
-
Definition of Brazing Temperature:
- Brazing is defined as a joining process where the filler metal melts at a temperature above 450°C (842°F) but below the melting point of the base metals. This ensures that the base materials remain solid while the filler metal flows into the joint.
-
Minimum Melting Temperature:
- The minimum melting temperature for brazing materials is typically around 450°C (842°F). This is the threshold that distinguishes brazing from soldering, which uses filler metals with lower melting points.
-
Importance of Dwell Temperature:
- The dwell temperature is the temperature at which the brazing process is held to allow the filler metal to melt and flow into the joint. This temperature must be carefully controlled to ensure proper wetting and bonding without overheating the base materials.
-
Time at Temperature:
- The time spent at the brazing temperature (dwell time) is crucial for achieving a strong joint. Insufficient time can lead to poor filler metal flow, while excessive time can cause unwanted diffusion or damage to the base materials.
-
Filler Metal Selection:
- The choice of filler metal depends on the base materials and the desired properties of the joint. Common filler metals include silver-based alloys, copper-based alloys, and nickel-based alloys, each with specific melting temperature ranges.
-
Thermal Considerations:
- The thermal properties of the base materials and the filler metal must be considered to avoid thermal stress, distortion, or damage during the brazing process. Proper heating and cooling rates are essential for achieving a high-quality joint.
-
Application-Specific Requirements:
- The minimum melting temperature for brazing materials can vary depending on the application. For example, high-temperature brazing for aerospace or industrial applications may require filler metals with higher melting points.
By understanding these key points, a purchaser can make informed decisions about the appropriate brazing materials and processes for their specific needs. Proper control of temperature and time ensures strong, reliable joints in brazed assemblies.
Summary Table:
Key Aspect | Details |
---|---|
Minimum Melting Temperature | 450°C (842°F) or higher, below the melting point of base metals. |
Dwell Temperature | Critical for proper filler metal flow and bonding, avoiding overheating. |
Dwell Time | Ensures strong joints; too little or too much time can compromise quality. |
Filler Metals | Silver, copper, or nickel-based alloys, chosen based on application needs. |
Thermal Considerations | Proper heating and cooling rates prevent thermal stress and distortion. |
Application-Specific Needs | High-temperature applications may require higher melting point fillers. |
Need help selecting the right brazing materials for your project? Contact our experts today for tailored solutions!