Pyrolysis is an oxygen-free thermal decomposition process in which organic materials are heated to high temperatures (typically 300-900℃), causing the breakdown of chemical bonds and the formation of smaller molecules. This process produces a mixture of gases, liquids (such as tar), and solid residues (like coke). The absence of oxygen prevents combustion, allowing for the recovery of valuable byproducts such as fuels and chemicals. Pyrolysis involves the cleavage of covalent bonds, releasing free radicals that drive further reactions. The process can occur under various conditions, including inert atmospheres, vacuums, or in the presence of other substances, leading to different types of pyrolysis (slow, fast, and flash) with distinct characteristics.
Key Points Explained:
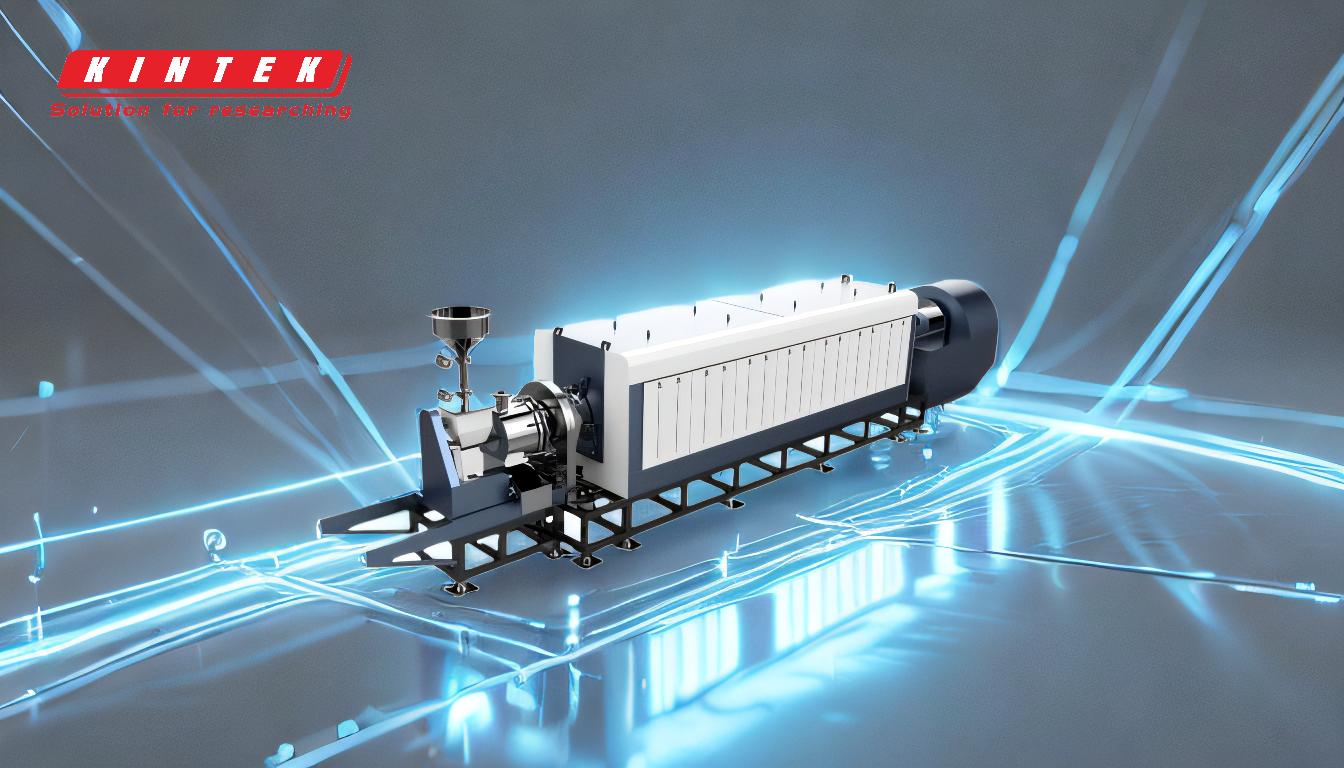
-
Definition and Mechanism of Pyrolysis:
- Pyrolysis is a thermal decomposition process that occurs in the absence of oxygen.
- It involves heating organic materials to high temperatures, causing the breakdown of chemical bonds.
- The process releases free radicals, which drive further reactions, leading to the formation of smaller molecules or residues with larger molecular mass.
-
Products of Pyrolysis:
- Gases: Light gases such as methane, hydrogen, and carbon monoxide are produced.
- Liquids: Tar and other liquid byproducts are formed, which can be used as fuels or chemical feedstocks.
- Solids: Coke and char are solid residues left after pyrolysis, often used in industrial applications.
-
Types of Pyrolysis:
- Slow Pyrolysis: Characterized by low heating rates and long residence times, resulting in higher yields of solid residues (char).
- Fast Pyrolysis: Involves rapid heating and short residence times, maximizing the production of liquid products (bio-oil).
- Flash Pyrolysis: A more extreme version of fast pyrolysis, with very high heating rates and extremely short residence times, often used to produce gases and light liquids.
-
Conditions and Influencing Factors:
- Temperature: Pyrolysis typically occurs at temperatures between 300-900℃, with higher temperatures favoring gas production.
- Atmosphere: The process is usually conducted in an inert atmosphere or vacuum to prevent side reactions like combustion or hydrolysis.
- Residence Time: The duration of heating affects the distribution of products, with longer times favoring solid residues and shorter times favoring liquids and gases.
-
Applications of Pyrolysis:
- Fuel Production: Pyrolysis is used to produce biofuels, syngas, and other energy sources.
- Chemical Feedstocks: The liquid and gaseous products can be used as raw materials in chemical synthesis.
- Waste Management: Pyrolysis is employed in the treatment of organic waste, converting it into useful products and reducing environmental impact.
-
Comparison with Combustion:
- Unlike combustion, which requires oxygen and produces mainly carbon dioxide and water, pyrolysis occurs in the absence of oxygen and yields a diverse range of products.
- Pyrolysis is more controlled and can be tailored to produce specific outputs, making it a versatile process for industrial applications.
By understanding these key points, one can appreciate the complexity and utility of pyrolysis as a chemical process, particularly in the context of producing valuable materials from organic waste or biomass.
Summary Table:
Aspect | Details |
---|---|
Definition | Oxygen-free thermal decomposition of organic materials at 300-900℃. |
Products | Gases (methane, hydrogen), liquids (tar), and solids (coke, char). |
Types | Slow, fast, and flash pyrolysis, each with distinct characteristics. |
Key Factors | Temperature, atmosphere, and residence time influence product distribution. |
Applications | Fuel production, chemical feedstocks, and waste management. |
Comparison | Unlike combustion, pyrolysis occurs without oxygen, yielding diverse outputs. |
Discover how pyrolysis can transform your industrial processes—contact our experts today!