Brazing carbide involves using a specialized paste or filler material to join carbide tips to a substrate, typically a steel body. The paste used in this process is crucial as it ensures a strong, durable bond between the carbide and the steel, which is essential for tools like cutting inserts, drill bits, and wear parts. The paste typically contains a combination of metals and fluxes that facilitate the brazing process by lowering the melting point of the filler material and preventing oxidation. The most common filler metals used are silver-based alloys, while the flux helps clean the surfaces and promotes wetting. The choice of paste depends on factors such as the type of carbide, the substrate material, and the operating conditions of the final product.
Key Points Explained:
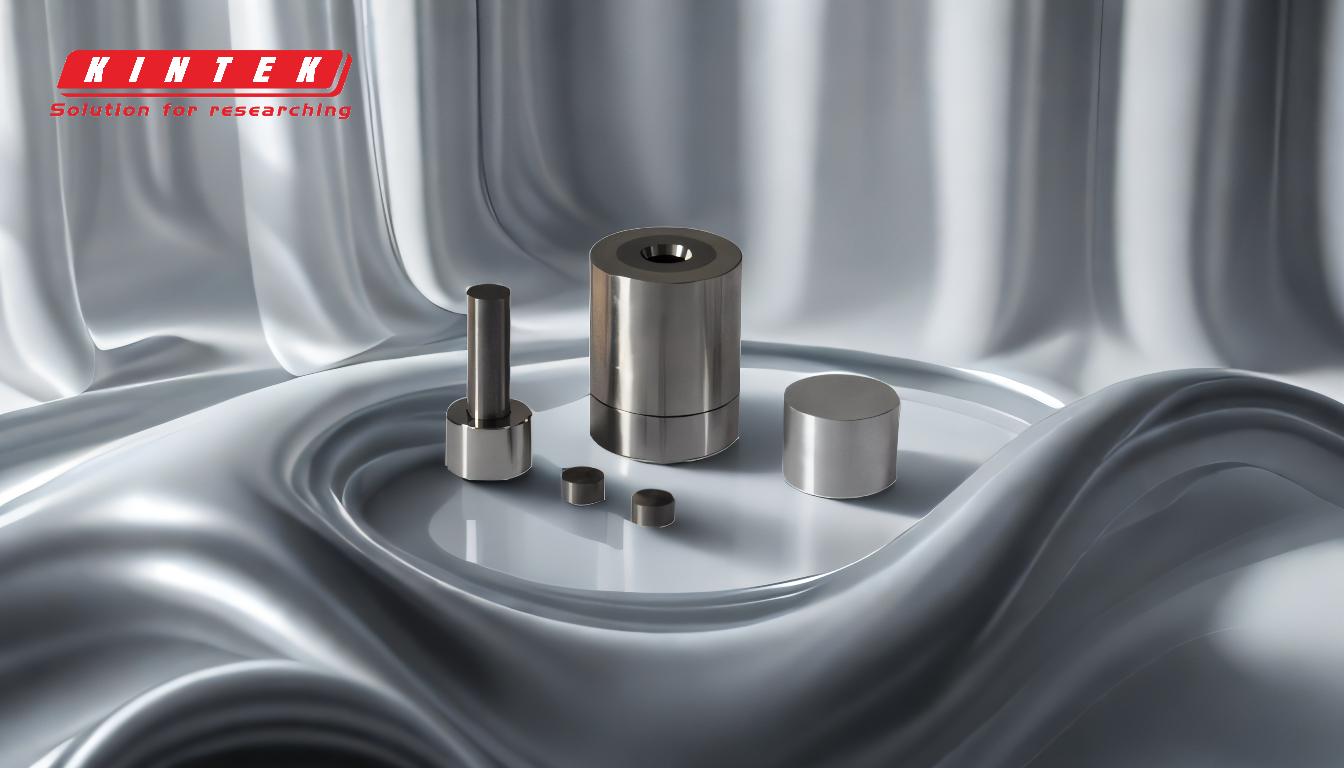
-
Purpose of Brazing Paste for Carbide
- Brazing paste is used to create a strong metallurgical bond between carbide and a substrate, usually steel.
- It ensures the carbide tip remains securely attached during high-stress applications like cutting or drilling.
- The paste must withstand high temperatures and provide excellent adhesion to both materials.
-
Composition of Brazing Paste
- Filler Metals: Silver-based alloys are the most common due to their excellent flow properties, low melting point, and strong bonding capability. Examples include silver-copper and silver-copper-zinc alloys.
- Flux: The flux component removes oxides from the surfaces of the carbide and steel, ensuring a clean bond. It also promotes wetting, allowing the filler metal to spread evenly.
- Binders: These hold the paste together and ensure it can be applied easily before the brazing process.
-
Types of Brazing Pastes
- Silver-Based Pastes: Widely used for their versatility and ability to bond carbide to steel effectively.
- Nickel-Based Pastes: Suitable for high-temperature applications where silver-based pastes may not perform well.
- Copper-Based Pastes: Less common but used in specific applications where cost is a concern.
-
Application Process
- The paste is applied to the joint area between the carbide and the substrate.
- The assembly is heated in a furnace or with a torch to the brazing temperature, typically between 600°C and 900°C.
- The flux activates, cleaning the surfaces, and the filler metal melts, flowing into the joint and forming a strong bond upon cooling.
-
Factors Influencing Paste Selection
- Carbide Type: Different grades of carbide may require specific pastes to ensure compatibility.
- Substrate Material: The paste must bond well with both the carbide and the substrate, usually steel.
- Operating Conditions: High-temperature or high-stress applications may require specialized pastes with enhanced properties.
-
Advantages of Using Brazing Paste
- Provides a strong, durable bond that can withstand mechanical and thermal stresses.
- Ensures precise application, reducing waste and improving efficiency.
- Suitable for complex geometries and small joint areas.
-
Challenges and Considerations
- Proper surface preparation is critical to ensure a strong bond.
- The brazing temperature must be carefully controlled to avoid damaging the carbide or substrate.
- Residual flux must be cleaned after brazing to prevent corrosion.
By understanding the composition, types, and application of brazing paste for carbide, manufacturers can select the right material for their specific needs, ensuring high-quality and long-lasting carbide tools and components.
Summary Table:
Aspect | Details |
---|---|
Purpose | Creates a strong bond between carbide and steel for high-stress applications. |
Composition | Filler metals (e.g., silver-based alloys), flux, and binders. |
Types | Silver-based, nickel-based, and copper-based pastes. |
Application Process | Applied to joint area, heated to 600°C–900°C, and cooled for bonding. |
Selection Factors | Carbide type, substrate material, and operating conditions. |
Advantages | Strong bond, precise application, and suitability for complex geometries. |
Challenges | Requires proper surface prep, temperature control, and flux cleaning. |
Need the right brazing paste for your carbide tools? Contact us today for expert advice!