The physical process of deposition involves the formation of a thin film or coating on a substrate through a series of well-defined steps. This process is influenced by material properties, substrate characteristics, and deposition methods. Key phases include adsorption, surface diffusion, nucleation, and growth, which determine the structure and quality of the deposited film. Techniques such as Physical Vapor Deposition (PVD) and vacuum deposition are commonly used, each involving specific steps like vacuum creation, material evaporation or sputtering, and film formation. The process may also include post-deposition treatments like annealing to enhance film properties.
Key Points Explained:
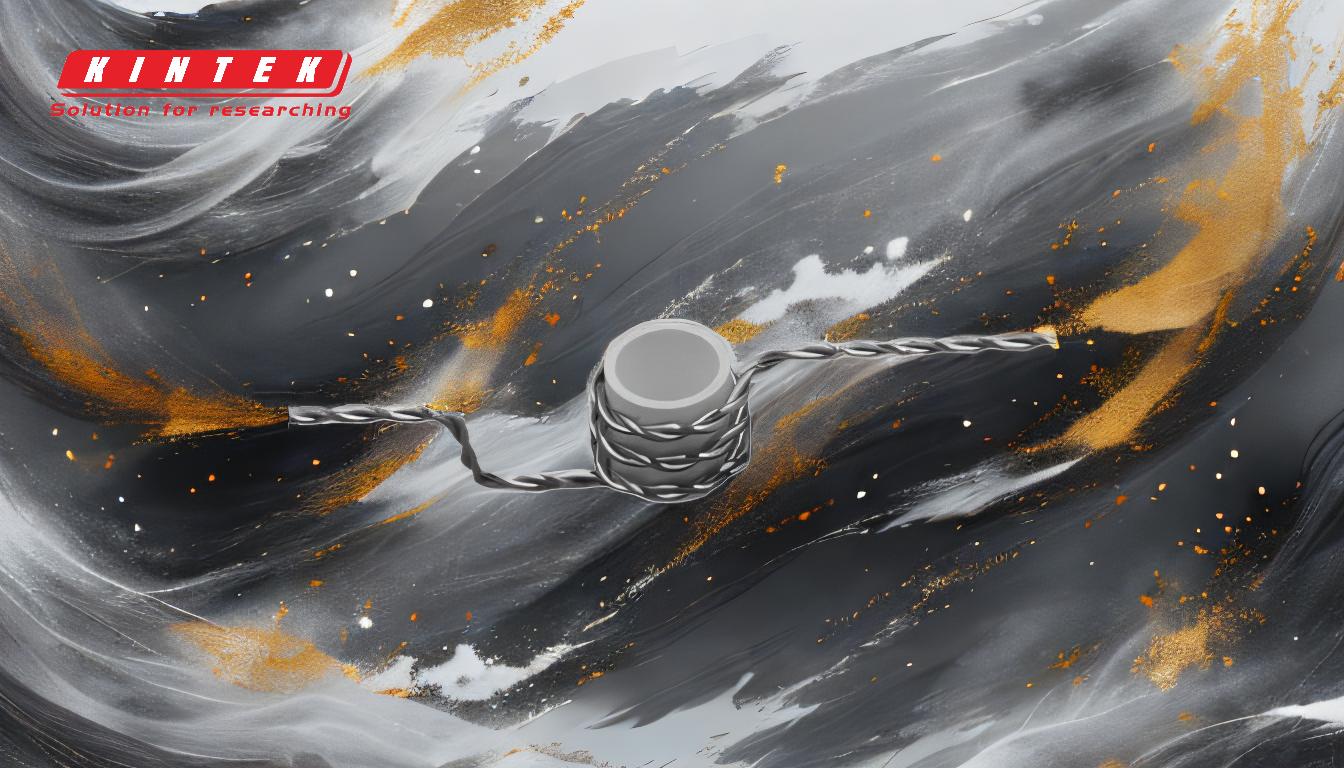
-
Phases of Thin Film Deposition:
- Adsorption: The initial phase where atoms or molecules from the coating material adhere to the substrate surface. This step is crucial as it determines the initial interaction between the material and the substrate.
- Surface Diffusion: After adsorption, the atoms or molecules migrate across the substrate surface to find stable positions. This diffusion is influenced by temperature and surface energy.
- Nucleation: Atoms or molecules cluster together to form stable nuclei, which serve as the foundation for further growth. The size and density of these nuclei affect the film's microstructure.
- Growth: The nuclei grow into a continuous thin film through the addition of more atoms or molecules. The growth mode (e.g., layer-by-layer or island growth) depends on the material-substrate interaction.
-
Physical Vapor Deposition (PVD):
- PVD is a widely used deposition technique that involves the physical transfer of material from a source to a substrate in a vacuum environment.
- Plasma-Assisted PVD (PAPVD): A modern variant of PVD that uses plasma to enhance the deposition process. It includes technologies like DC diode, RF, and ion beam-assisted coatings, which improve film quality and adhesion.
-
Vacuum Deposition Process:
- Vacuum Creation: A vacuum chamber is used to remove air and gases that could interfere with the deposition process. This ensures a clean environment for material transfer.
- Substrate Preparation: The substrate is cleaned or treated to improve adhesion and film quality. This step is critical for achieving a uniform and defect-free coating.
- Material Evaporation or Sputtering: The coating material is either heated to form a vapor (evaporation) or bombarded with ions to eject atoms (sputtering). Both methods transport the material to the substrate.
- Film Formation: The vaporized or sputtered material condenses on the substrate, forming a thin film. The film's properties, such as thickness and uniformity, depend on deposition parameters like temperature and pressure.
- Post-Deposition Steps: After deposition, the system is cooled and vented. The film may undergo additional treatments like annealing to enhance its properties.
-
Material and Substrate Interaction:
- The success of the deposition process depends on the compatibility between the coating material and the substrate. Factors like surface energy, lattice mismatch, and chemical reactivity play a significant role in determining the film's structure and adhesion.
-
Post-Deposition Treatments:
- Annealing: A heat treatment process that relieves internal stresses, improves crystallinity, and enhances the film's mechanical and electrical properties.
- Analysis and Optimization: The deposited film is analyzed to evaluate its properties, such as thickness, adhesion, and microstructure. This feedback is used to refine the deposition process for better results.
By understanding these key points, one can better appreciate the complexity and precision required in the physical process of deposition, whether for industrial applications or advanced research.
Summary Table:
Key Phase | Description |
---|---|
Adsorption | Atoms or molecules adhere to the substrate surface, initiating the process. |
Surface Diffusion | Atoms migrate across the substrate to find stable positions. |
Nucleation | Atoms cluster to form stable nuclei, laying the foundation for film growth. |
Growth | Nuclei expand into a continuous thin film through additional material deposition. |
Post-Deposition | Treatments like annealing enhance film properties and performance. |
Ready to optimize your deposition process? Contact our experts today for tailored solutions!