Plasma-enhanced chemical vapor deposition (PECVD) is a widely used low-temperature vacuum thin-film deposition process in the semiconductor industry. Unlike traditional CVD, PECVD operates at much lower temperatures, making it suitable for coating temperature-sensitive materials. The process involves the use of plasma to induce chemical reactions, enabling the deposition of thin films at near-ambient temperatures. Key factors influencing PECVD include pressure, precursor gases, and electrode spacing. The pressure in PECVD typically ranges from 0.1 to 10 Torr, balancing vapor scattering and deposition uniformity. Precursor gases like silane and ammonia, often mixed with inert gases, are introduced into the chamber to control the deposition process. Electrode spacing and chamber design also play crucial roles in ensuring uniform film deposition and minimizing substrate damage.
Key Points Explained:
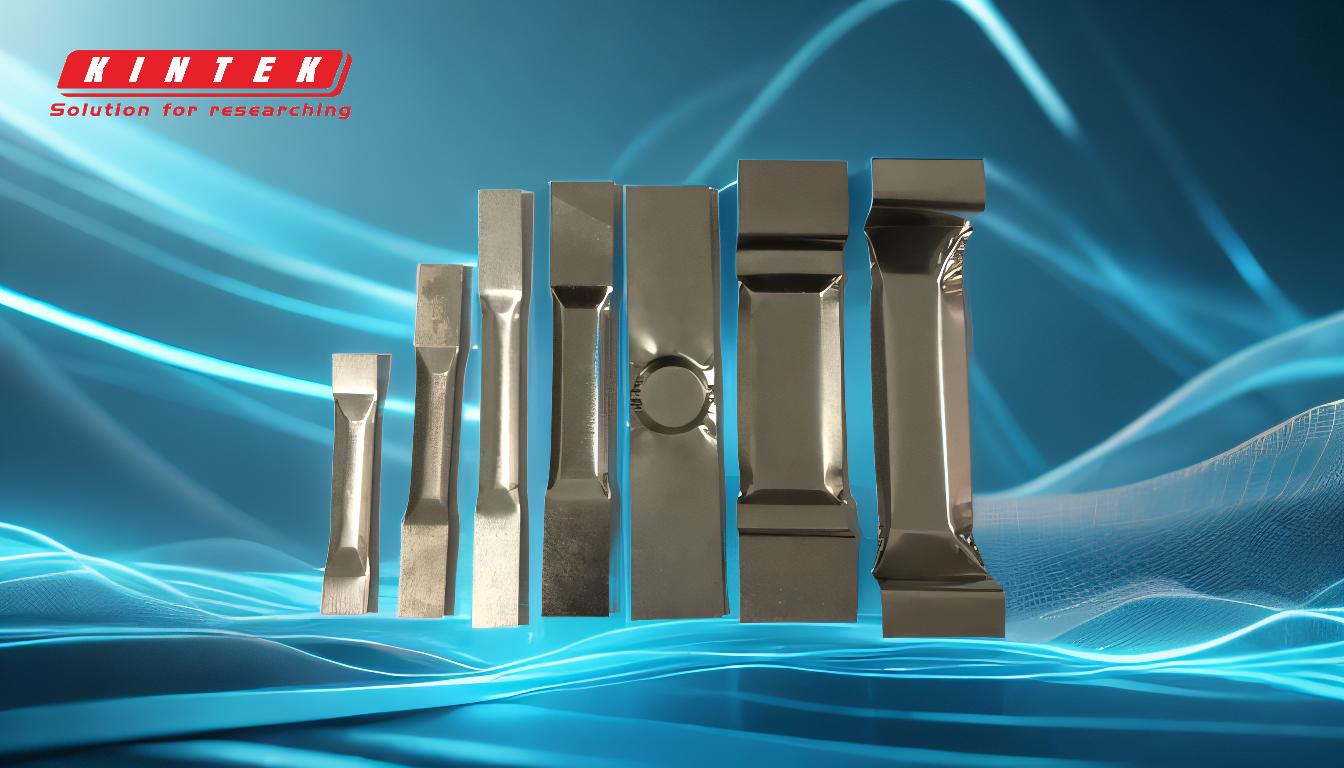
-
Pressure Range in PECVD:
- PECVD operates at relatively low pressures, typically between 0.1 and 10 Torr. This pressure range is crucial for maintaining plasma stability and ensuring uniform film deposition.
- At lower pressures (<10⁻⁴ Torr), processes like EBPVD become line-of-sight, limiting their ability to coat non-line-of-sight surfaces. In contrast, PECVD's higher pressure range allows for significant vapor scattering, enabling the coating of surfaces not directly in the line of sight of the source.
- The pressure is carefully controlled to balance the need for uniform deposition with the avoidance of excessive scattering, which could lead to non-uniform film thickness.
-
Role of Plasma in PECVD:
- PECVD utilizes plasma to induce chemical reactions at lower temperatures compared to traditional CVD. This is achieved through the use of an RF (radio frequency) power source, which excites the precursor gases into a plasma state.
- The plasma provides the energy required for the chemical reactions to occur, allowing deposition to take place at temperatures close to ambient. This is particularly beneficial for materials that are sensitive to high temperatures.
- The use of plasma also opens up new reaction pathways, enabling the deposition of films that would otherwise require much higher temperatures.
-
Precursor Gases and Their Role:
- Precursor gases such as silane (SiH₄) and ammonia (NH₃) are commonly used in PECVD. These gases are often mixed with inert gases like argon (Ar) or nitrogen (N₂) to control the deposition process.
- The gases are introduced into the reaction chamber via a shower head fixture, ensuring even distribution over the substrate. This helps in achieving uniform film thickness and composition.
- The choice of precursor gases and their ratios can significantly affect the properties of the deposited film, including its stoichiometric purity and structural integrity.
-
Electrode Spacing and Chamber Design:
- The spacing between the electrodes in a PECVD system affects the starting voltage, plasma potential, and substrate damage. A larger spacing can reduce substrate damage but must be carefully balanced to avoid aggravating the edge effect of the electric field, which can affect deposition uniformity.
- The size and design of the reaction chamber also impact productivity and thickness uniformity. Larger chambers can accommodate more substrates, increasing throughput, but must be designed to maintain uniform plasma distribution.
- Proper chamber design and electrode spacing are critical for minimizing defects and ensuring high-quality film deposition.
-
Advantages of PECVD:
- One of the primary advantages of PECVD is its ability to deposit thin films at low temperatures, making it suitable for temperature-sensitive materials.
- The use of plasma allows for the deposition of films with unique properties that are difficult to achieve with traditional CVD.
- PECVD is highly versatile and can be used to deposit a wide range of materials, including silicon-based films, oxides, and nitrides, making it a valuable tool in the semiconductor industry.
In summary, PECVD is a highly effective thin-film deposition technique that leverages plasma to enable low-temperature deposition. The pressure range, precursor gases, and chamber design are all critical factors that influence the quality and uniformity of the deposited films. Understanding these parameters is essential for optimizing the PECVD process and achieving the desired film properties.
Summary Table:
Parameter | Details |
---|---|
Pressure Range | 0.1 to 10 Torr |
Key Role | Balances vapor scattering and deposition uniformity |
Impact of Low Pressure | Limits non-line-of-sight coating (e.g., EBPVD) |
Impact of High Pressure | Enables coating of non-line-of-sight surfaces |
Precursor Gases | Silane (SiH₄), Ammonia (NH₃), mixed with inert gases (Ar, N₂) |
Chamber Design | Critical for uniform plasma distribution and minimizing substrate damage |
Need help optimizing your PECVD process? Contact our experts today for tailored solutions!