The pressure in chemical vapor deposition (CVD) varies significantly depending on the specific type of CVD process and the materials being deposited. Generally, CVD processes can operate at a wide range of pressures, from very low pressures (e.g., a few millitorr) to atmospheric pressure or even higher. For example, low-pressure CVD (LPCVD) typically operates between 0.1 to 10 Torr, while plasma-enhanced CVD (PECVD) operates between 10 to 100 Pa. Atmospheric pressure CVD (APCVD) operates at or near atmospheric pressure. The choice of pressure depends on factors such as the desired film quality, deposition rate, and equipment capabilities.
Key Points Explained:
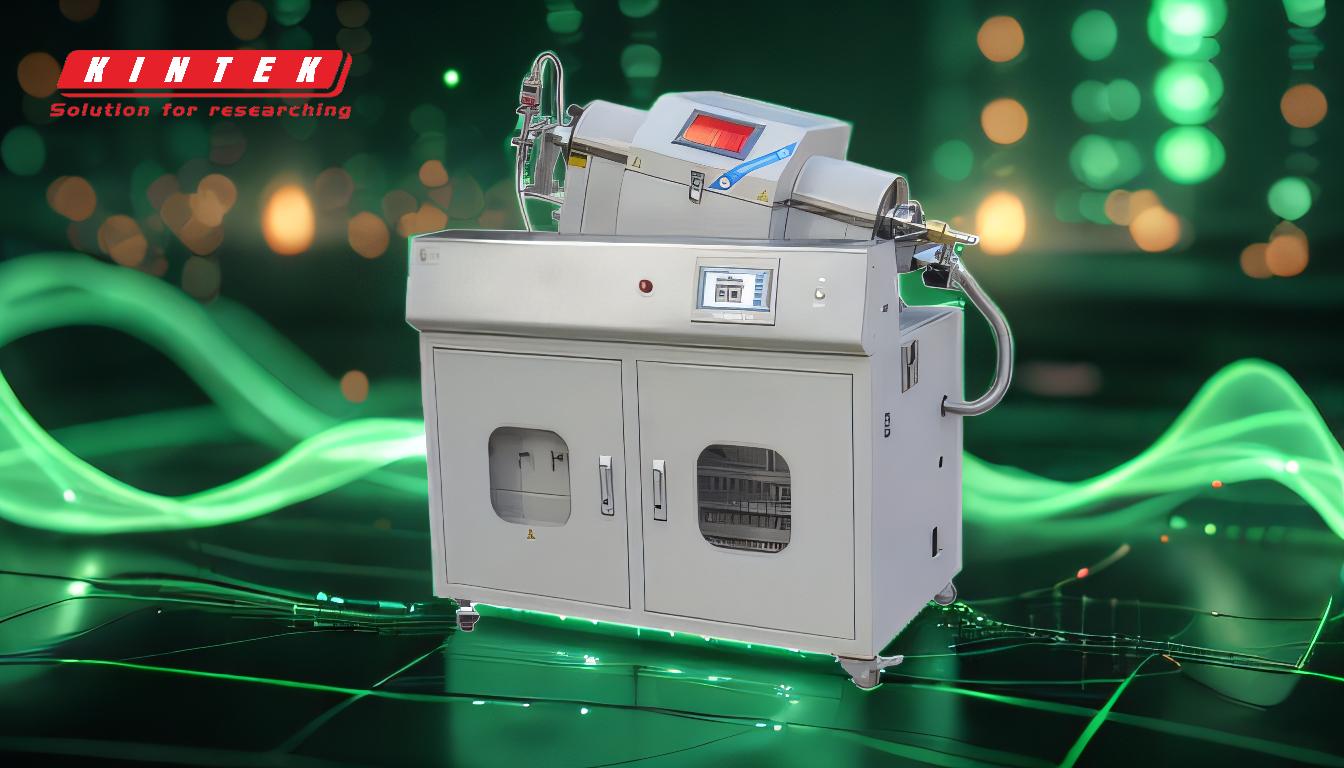
-
Pressure Range in CVD Processes:
- CVD processes can operate at a wide range of pressures, from a few millitorr (low vacuum) to atmospheric pressure or higher.
- The pressure range is influenced by the specific type of CVD process and the materials being deposited.
-
Low-Pressure CVD (LPCVD):
- LPCVD operates in the range of 0.1 to 10 Torr, which is considered a medium vacuum application.
- This pressure range is suitable for producing high-quality, uniform films with good step coverage, often used in semiconductor manufacturing.
-
Plasma-Enhanced CVD (PECVD):
- PECVD systems typically operate at pressures between 10 to 100 Pa.
- The use of plasma allows for lower deposition temperatures, making it suitable for temperature-sensitive substrates.
-
Atmospheric Pressure CVD (APCVD):
- APCVD operates at or near atmospheric pressure.
- This method is often used for high-throughput applications where lower film quality is acceptable, such as in the production of solar cells.
-
Pressure in Silicon Dioxide Deposition:
- Silicon dioxide deposition typically occurs at pressures ranging from a few millitorr to a few torr.
- This range is common in processes like thermal oxidation and LPCVD.
-
Low-Pressure Plasma for CVD:
- Low-pressure plasma used in CVD applications is generally produced in a pressure range of 10^−5 to 10 torr.
- This range is suitable for creating a stable plasma environment, which enhances the deposition process.
-
Influence of Pressure on Film Properties:
- Lower pressures (e.g., LPCVD) tend to produce films with better uniformity and step coverage but may require longer deposition times.
- Higher pressures (e.g., APCVD) can lead to faster deposition rates but may result in less uniform films.
-
Equipment Considerations:
- The choice of pressure range also depends on the capabilities of the CVD equipment, including the vacuum system and gas delivery system.
- For example, operating at very low pressures requires robust vacuum pumps and precise control systems.
By understanding these key points, a purchaser or engineer can make informed decisions about the appropriate pressure range for a specific CVD application, balancing factors such as film quality, deposition rate, and equipment requirements.
Summary Table:
CVD Process | Pressure Range | Key Applications |
---|---|---|
LPCVD | 0.1 to 10 Torr | High-quality, uniform films for semiconductors |
PECVD | 10 to 100 Pa | Temperature-sensitive substrates |
APCVD | Atmospheric pressure | High-throughput applications (e.g., solar cells) |
Silicon Dioxide | Few millitorr to few torr | Thermal oxidation, LPCVD |
Low-Pressure Plasma | 10^−5 to 10 torr | Stable plasma-enhanced deposition |
Need help selecting the right CVD process for your application? Contact our experts today for personalized guidance!