Low-pressure chemical vapor deposition (LPCVD) systems typically operate within a pressure range of 0.1 to 10 Torr, which is considered a medium vacuum application. This pressure range is essential for achieving uniform film deposition, minimizing gas-phase reactions, and ensuring high-quality thin films. The operating temperature for LPCVD systems generally ranges from 425°C to 900°C, depending on the material being deposited. For example, silicon dioxide is often deposited at around 650°C. The pressure and temperature ranges are carefully controlled to optimize film properties, such as uniformity, density, and adhesion, while minimizing defects and contamination.
Key Points Explained:
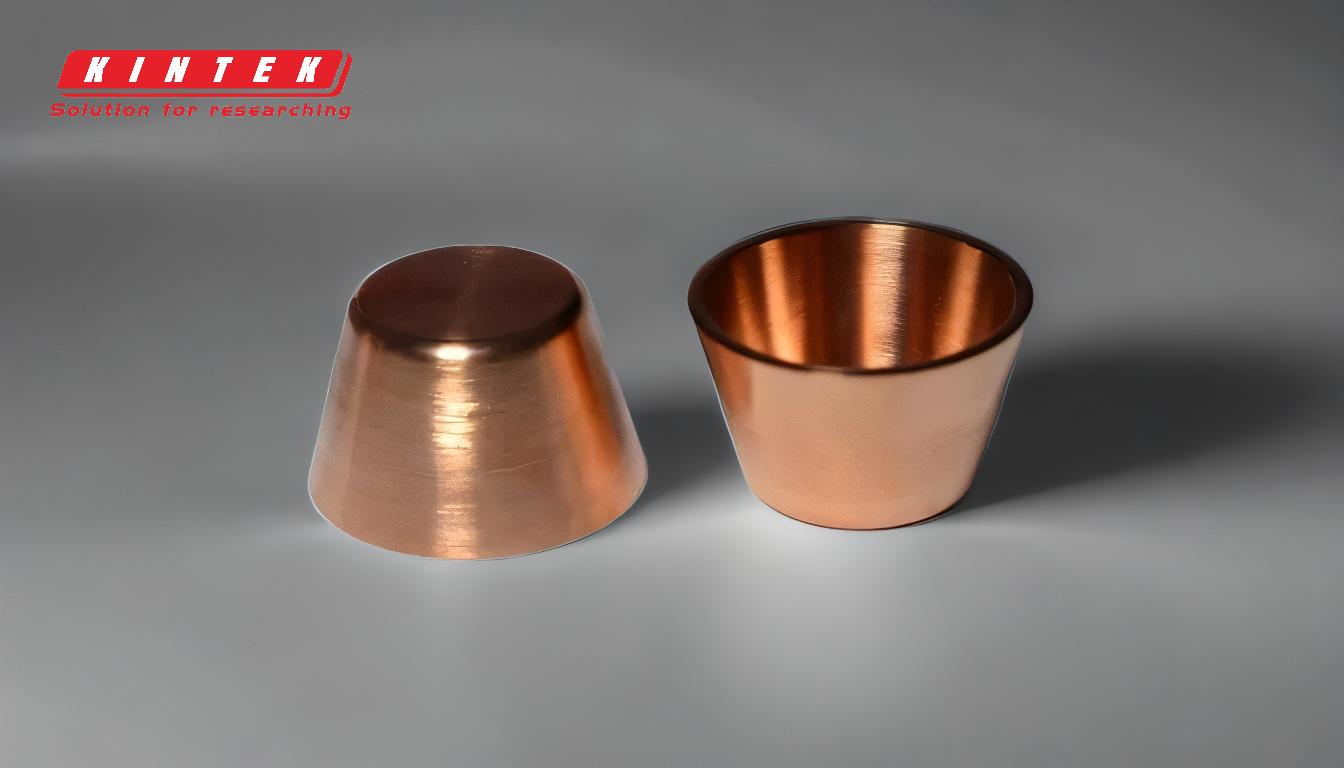
-
Pressure Range in LPCVD Systems:
- LPCVD systems typically operate at pressures between 0.1 to 10 Torr.
- This range is classified as a medium vacuum, which is lower than atmospheric pressure (760 Torr) but higher than high-vacuum systems.
- The low-pressure environment reduces gas-phase reactions and promotes uniform film deposition by ensuring that reactant gases reach the substrate surface without significant scattering.
-
Importance of Pressure Control:
- Maintaining a precise pressure range is critical for achieving consistent film quality.
- Pressure control is achieved using vacuum pumps and pressure control systems, which ensure that the pressure remains constant throughout the deposition process.
- Deviations from the optimal pressure range can lead to defects, poor film uniformity, or incomplete reactions.
-
Temperature Range in LPCVD:
- LPCVD processes typically require high temperatures, ranging from 425°C to 900°C.
- The specific temperature depends on the material being deposited. For example:
- Silicon dioxide is often deposited at around 650°C.
- Other materials, such as silicon nitride or polysilicon, may require higher temperatures.
- High temperatures are necessary to activate the chemical reactions that form the thin films on the substrate.
-
Comparison with Other CVD Techniques:
-
PECVD (Plasma-Enhanced Chemical Vapor Deposition):
- Operates at lower pressures (typically 0.1 to 10 Torr) and lower temperatures (200°C to 500°C).
- Uses plasma to enhance chemical reactions, allowing for lower operating temperatures.
-
APCVD (Atmospheric Pressure Chemical Vapor Deposition):
- Operates at or near atmospheric pressure, which can lead to higher gas-phase reactions and less uniform films compared to LPCVD.
- LPCVD strikes a balance between the high-quality films of low-pressure systems and the higher throughput of atmospheric systems.
-
PECVD (Plasma-Enhanced Chemical Vapor Deposition):
-
Advantages of LPCVD:
- Uniform Film Deposition: The low-pressure environment ensures that reactant gases are evenly distributed across the substrate, leading to highly uniform films.
- High-Quality Films: The combination of low pressure and high temperature results in dense, defect-free films with excellent adhesion.
- Versatility: LPCVD can deposit a wide range of materials, including silicon dioxide, silicon nitride, and polysilicon, making it suitable for various semiconductor and MEMS applications.
-
Applications of LPCVD:
- LPCVD is widely used in the semiconductor industry for depositing thin films in integrated circuit (IC) fabrication.
- It is also used in the production of microelectromechanical systems (MEMS), where precise control over film thickness and uniformity is critical.
- Common materials deposited using LPCVD include:
- Silicon Dioxide (SiO₂): Used as an insulating layer in ICs.
- Silicon Nitride (Si₃N₄): Used as a passivation layer or mask in lithography.
- Polysilicon: Used for gate electrodes in transistors.
-
System Configurations:
- LPCVD systems come in various configurations, including:
- Tubular Hot-Wall Reactors: These are batch systems where multiple wafers are processed simultaneously in a heated tube.
- Vertical Flow Batch Reactors: These systems allow for better gas flow control and are often used for high-volume production.
- Single-Wafer Reactors: These are used in modern fabs for better process control and integration, especially in advanced semiconductor manufacturing.
- LPCVD systems come in various configurations, including:
-
Challenges and Considerations:
- Thermal Budget: The high temperatures required for LPCVD can limit its use in processes where thermal damage to the substrate is a concern.
- Throughput: Batch systems offer higher throughput but may sacrifice some uniformity compared to single-wafer systems.
- Cost: LPCVD systems can be expensive to operate due to the need for precise temperature and pressure control, as well as high-quality vacuum equipment.
By understanding the pressure and temperature ranges of LPCVD systems, as well as their advantages and limitations, equipment and consumable purchasers can make informed decisions about the suitability of LPCVD for their specific applications.
Summary Table:
Parameter | Range | Details |
---|---|---|
Pressure Range | 0.1 to 10 Torr | Medium vacuum, essential for uniform film deposition and minimal gas-phase reactions. |
Temperature Range | 425°C to 900°C | Depends on material (e.g., 650°C for SiO₂). High temps activate reactions. |
Key Advantages | Uniformity, Quality, Versatility | Ensures dense, defect-free films with excellent adhesion. |
Applications | Semiconductors, MEMS | Used for IC fabrication, MEMS production, and depositing SiO₂, Si₃N₄, polysilicon. |
System Configurations | Tubular, Vertical, Single-Wafer | Batch or single-wafer systems for varied throughput and precision. |
Need expert advice on LPCVD systems? Contact us today to optimize your thin film processes!