Hot isostatic pressing (HIP) is a manufacturing process that uses high temperature and pressure to improve the properties of materials, such as density, strength, and uniformity. The pressure applied during this process is a critical factor, as it directly influences the quality and characteristics of the final product. The pressure in hot isostatic pressing typically ranges from 100 to 300 MPa, depending on the material and application. For warm isostatic pressing, the pressure is generally around 300 MPa, which is sufficient to achieve the desired densification and uniformity in materials like ceramics and metals. This process is widely used in industries such as aerospace, automotive, and medical devices to produce high-performance components.
Key Points Explained:
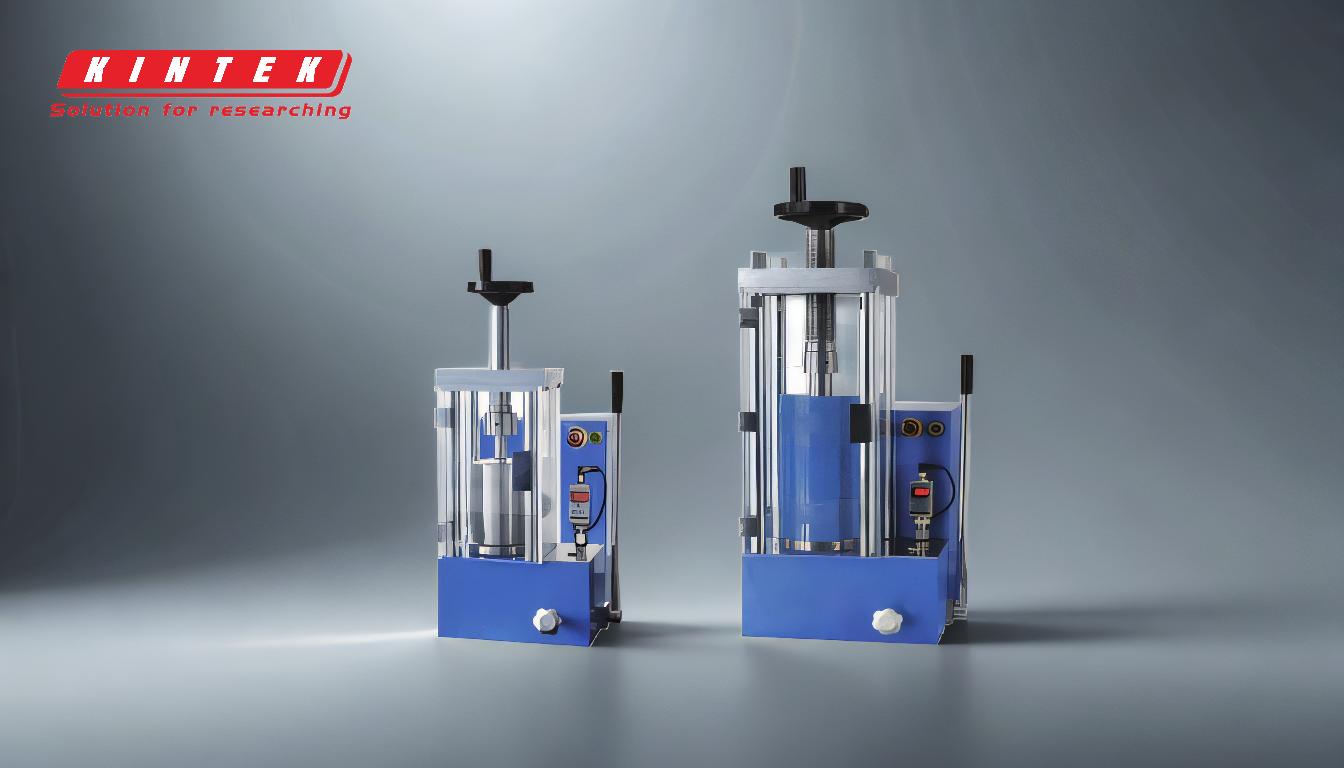
-
Pressure Range in Hot Isostatic Pressing:
- The pressure in hot isostatic pressing typically ranges from 100 to 300 MPa. This range ensures that the material undergoes sufficient densification and uniformity.
- For ceramics, the pressure can vary between 21 to 210 MPa (3000 to 30000 psi), depending on the specific material and application requirements.
- In some cases, particularly for advanced materials, pressures can exceed 690 MPa (100,000 psi) to achieve the desired properties.
-
Pressure in Warm Isostatic Pressing:
- Warm isostatic pressing operates at a slightly lower temperature compared to hot isostatic pressing but still uses high pressure to densify materials.
- The pressure used in warm isostatic press is typically around 300 MPa. This pressure is sufficient to achieve the necessary densification and uniformity in materials like ceramics and metals.
-
Factors Influencing Pressure Requirements:
- Material Type: Different materials require different pressures for optimal densification. For example, ceramics may require lower pressures compared to metals.
- Application Requirements: The intended use of the final product can influence the pressure needed. High-performance components, such as those used in aerospace, may require higher pressures.
- Vessel Size and Pump Capacity: The size of the isostatic pressing vessel and the capacity of the pump can also affect the pressure that can be applied.
-
Process Efficiency and Production Rates:
- The efficiency of the isostatic pressing process depends on factors such as applied pressure, vessel size, and level of automation.
- Production rates can achieve one operation cycle per minute or faster, depending on the equipment and process parameters.
-
Importance of Pressure in Isostatic Pressing:
- The pressure applied during isostatic pressing is crucial for achieving the desired material properties, such as density, strength, and uniformity.
- High pressure ensures that the material is uniformly compressed, leading to a more homogeneous final product.
In summary, the pressure used in hot and warm isostatic pressing is a critical parameter that directly influences the quality and characteristics of the final product. The typical pressure range for hot isostatic pressing is 100 to 300 MPa, while warm isostatic pressing generally uses around 300 MPa. Understanding the pressure requirements for different materials and applications is essential for optimizing the isostatic pressing process and achieving high-quality results.
Summary Table:
Parameter | Details |
---|---|
Hot Isostatic Pressing (HIP) | Pressure range: 100–300 MPa, up to 690 MPa for advanced materials |
Warm Isostatic Pressing | Pressure: ~300 MPa, ideal for ceramics and metals |
Key Influencing Factors | Material type, application requirements, vessel size, and pump capacity |
Applications | Aerospace, automotive, medical devices, and high-performance components |
Process Efficiency | Achieves one operation cycle per minute or faster |
Optimize your material properties with precise isostatic pressing—contact our experts today!