Vacuum induction melting (VIM) is a sophisticated process used to melt metals under vacuum conditions using electromagnetic induction as the energy source. The process involves placing solid metal raw materials in a crucible surrounded by an induction coil. When an alternating current passes through the coil, it generates an induced electromotive force, creating eddy currents within the metal. These eddy currents produce heat, which melts the metal. The vacuum environment removes gas impurities, ensuring the production of high-purity metal alloys. Additionally, the electromagnetic forces in the crucible stir the molten metal, ensuring uniform composition. This method is highly efficient, fast, and environmentally friendly, making it ideal for producing high-quality metal alloys.
Key Points Explained:
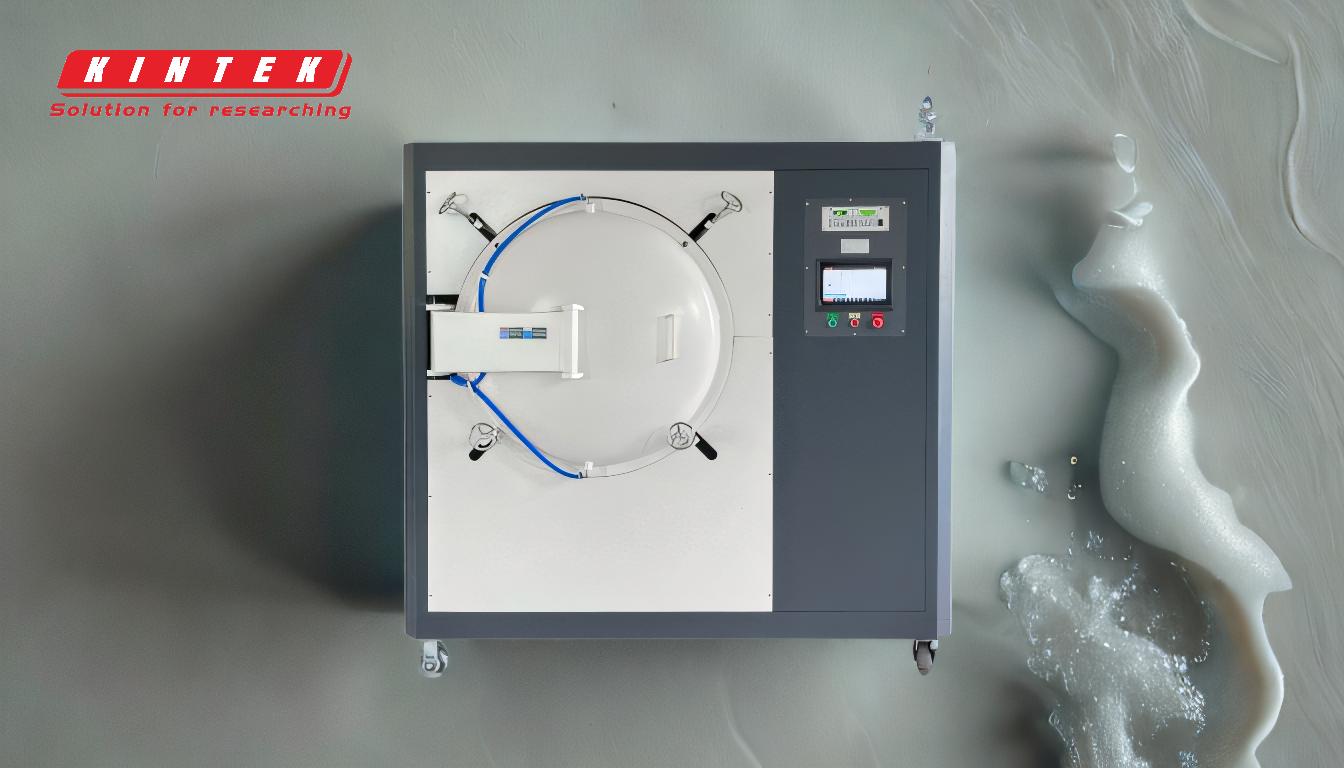
-
Electromagnetic Induction:
- The core principle of VIM is electromagnetic induction. When an alternating current flows through the induction coil, it generates a magnetic field. This magnetic field induces eddy currents in the metal charge placed inside the crucible.
- These eddy currents generate heat due to the electrical resistance of the metal, leading to its melting. The process is highly efficient as it directly heats the metal without any intermediate heat transfer medium.
-
Skin Effect:
- The skin effect is a phenomenon where alternating currents tend to flow near the surface of a conductor. In VIM, this effect ensures that the heat generation is concentrated on the outer layers of the metal charge, promoting efficient and uniform heating.
- This concentration of heat on the surface helps in faster melting and reduces the risk of overheating the core of the metal charge.
-
Vacuum Environment:
- The vacuum environment is crucial in VIM as it prevents the metal from reacting with atmospheric gases like oxygen and nitrogen. This is particularly important for metals and alloys that have a high affinity for these gases.
- The vacuum also helps in removing dissolved gases and volatile impurities from the molten metal, resulting in higher purity and better quality of the final product.
-
Induction Coil and Crucible:
- The induction coil, typically made of copper, is water-cooled to withstand the high temperatures generated during the process. The crucible, lined with suitable refractories, holds the metal charge and is designed to withstand the thermal and mechanical stresses of the melting process.
- The crucible is placed inside a vacuum chamber, which is airtight to maintain the required vacuum conditions.
-
Heat Generation and Melting:
- The heat generated by the eddy currents must exceed the rate of heat dissipation for the metal to melt. This ensures that the metal transitions from a solid to a liquid state efficiently.
- The melting process is controlled by regulating the power supplied to the induction coil, ensuring precise temperature control.
-
Electromagnetic Stirring:
- The electromagnetic forces generated during the process cause the molten metal to stir automatically. This stirring action ensures a uniform composition and temperature throughout the molten metal, which is essential for producing high-quality alloys.
- The stirring also helps in the removal of inclusions and impurities, further enhancing the purity of the metal.
-
Process Control and Monitoring:
- VIM involves precise control and monitoring of various parameters such as power, temperature, vacuum level, and feeding of raw materials. This ensures the process is carried out under optimal conditions, leading to consistent and high-quality results.
- Advanced control systems are often used to automate and monitor the process, ensuring reproducibility and efficiency.
-
Applications and Advantages:
- VIM is widely used in the production of high-performance alloys, superalloys, and specialty metals used in aerospace, medical, and energy industries. The process offers several advantages, including high purity, uniform composition, and the ability to melt reactive and refractory metals.
- The vacuum environment and electromagnetic stirring contribute to the production of metals with superior mechanical properties and performance characteristics.
In summary, vacuum induction melting is a highly controlled and efficient process that leverages electromagnetic induction to melt metals under vacuum conditions. The combination of electromagnetic induction, skin effect, and vacuum environment ensures the production of high-purity, high-quality metal alloys with uniform composition and superior properties.
Summary Table:
Key Aspect | Description |
---|---|
Electromagnetic Induction | Generates eddy currents to heat and melt metal directly, ensuring high efficiency. |
Skin Effect | Concentrates heat on the metal's surface for faster, uniform heating. |
Vacuum Environment | Prevents gas reactions, removes impurities, and ensures high-purity alloys. |
Induction Coil & Crucible | Water-cooled coil and refractory-lined crucible withstand extreme conditions. |
Heat Generation | Controlled melting by regulating power to the induction coil. |
Electromagnetic Stirring | Ensures uniform composition and removes impurities in molten metal. |
Process Control | Precise monitoring of power, temperature, and vacuum for consistent results. |
Applications | Used in aerospace, medical, and energy industries for high-performance alloys. |
Learn how vacuum induction melting can revolutionize your metal production—contact our experts today!