Vapor deposition is a process used to create thin films or coatings on a substrate by depositing material from a vapor phase. This technique is widely used in industries such as semiconductor manufacturing, optics, and protective coatings. There are two main types of vapor deposition: Chemical Vapor Deposition (CVD) and Physical Vapor Deposition (PVD). CVD involves chemical reactions to deposit material, while PVD relies on physical processes like evaporation or sputtering. Both methods require controlled environments, such as vacuum chambers, and specific conditions like temperature and pressure to ensure precise and high-quality coatings.
Key Points Explained:
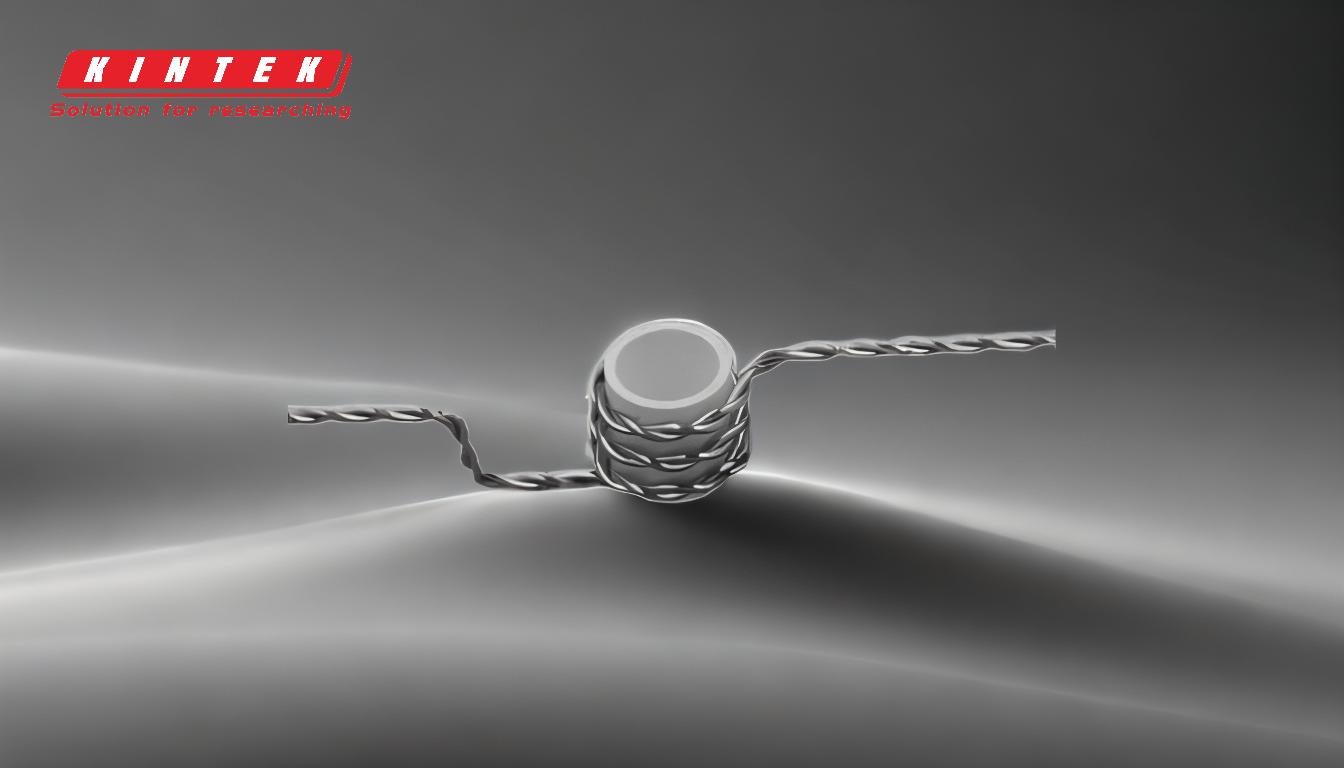
-
Overview of Vapor Deposition:
- Vapor deposition is a process where materials are deposited onto a substrate in the form of a thin film or coating.
- It is used in various industries, including electronics, optics, and surface engineering.
- The process can be categorized into Chemical Vapor Deposition (CVD) and Physical Vapor Deposition (PVD).
-
Chemical Vapor Deposition (CVD):
- Principle: CVD involves the use of chemical reactions to deposit a solid material from a vapor phase onto a substrate.
-
Process:
- A precursor gas is introduced into a reaction chamber.
- The gas reacts either on the substrate surface or in the vicinity of the substrate, forming a solid deposit.
- The reaction is often facilitated by heat, plasma, or other energy sources.
- Applications: CVD is used to deposit materials like silicon, silicon dioxide, and various metals in semiconductor manufacturing.
-
Advantages:
- High-quality, uniform coatings.
- Ability to deposit complex materials and alloys.
-
Limitations:
- Requires high temperatures and controlled environments.
- Can involve toxic or hazardous gases.
-
Physical Vapor Deposition (PVD):
- Principle: PVD involves the physical transformation of a solid material into a vapor phase, which then condenses onto a substrate to form a thin film.
-
Process:
- The solid material (target) is vaporized using methods like thermal evaporation, sputtering, or laser ablation.
- The vaporized material travels through a low-pressure chamber and deposits onto the substrate.
- Applications: PVD is used to create durable, corrosion-resistant coatings for tools, medical devices, and decorative finishes.
-
Advantages:
- High precision and control over film thickness.
- Ability to deposit a wide range of materials, including metals, ceramics, and alloys.
-
Limitations:
- Requires vacuum conditions, which can increase equipment costs.
- Limited to line-of-sight deposition, making it less suitable for complex geometries.
-
Key Components of Vapor Deposition Systems:
- Target Material: The material to be deposited, which can be a metal, semiconductor, or ceramic.
- Substrate: The surface onto which the material is deposited.
- Reaction Chamber: A controlled environment (often a vacuum) where the deposition occurs.
- Energy Source: Heat, plasma, or lasers used to vaporize or activate the precursor material.
- Pressure and Temperature Control: Critical parameters that influence the quality and properties of the deposited film.
-
Comparison Between CVD and PVD:
-
CVD:
- Relies on chemical reactions.
- Typically requires higher temperatures.
- Suitable for depositing complex materials and alloys.
-
PVD:
- Relies on physical processes like evaporation or sputtering.
- Operates at lower temperatures compared to CVD.
- Better for creating highly durable and corrosion-resistant coatings.
-
CVD:
-
Applications of Vapor Deposition:
- Semiconductors: CVD is widely used to deposit thin films of silicon, silicon dioxide, and other materials in integrated circuit fabrication.
- Optics: Both CVD and PVD are used to create anti-reflective coatings, mirrors, and optical filters.
- Protective Coatings: PVD is commonly used to apply hard, wear-resistant coatings on tools and components.
- Decorative Finishes: PVD is used to create aesthetically pleasing, durable finishes on consumer products like watches and jewelry.
-
Future Trends in Vapor Deposition:
- Atomic Layer Deposition (ALD): A variant of CVD that allows for extremely precise control of film thickness at the atomic level.
- Hybrid Techniques: Combining CVD and PVD to leverage the advantages of both methods.
- Sustainability: Developing environmentally friendly precursor materials and reducing energy consumption in deposition processes.
In conclusion, vapor deposition is a versatile and essential technology for creating thin films and coatings with precise control over material properties. Whether through chemical or physical means, the process enables the production of high-performance materials used in a wide range of applications, from electronics to protective coatings.
Summary Table:
Aspect | Chemical Vapor Deposition (CVD) | Physical Vapor Deposition (PVD) |
---|---|---|
Principle | Uses chemical reactions to deposit material from a vapor phase. | Relies on physical processes like evaporation or sputtering to deposit material. |
Temperature | Requires higher temperatures. | Operates at lower temperatures compared to CVD. |
Applications | Ideal for depositing complex materials and alloys (e.g., semiconductors). | Best for durable, corrosion-resistant coatings (e.g., tools, medical devices). |
Advantages | High-quality, uniform coatings; suitable for complex materials. | High precision, durable coatings; wide range of materials. |
Limitations | High temperatures, toxic gases, and controlled environments required. | Vacuum conditions increase costs; limited to line-of-sight deposition. |
Discover how vapor deposition can enhance your projects—contact our experts today for tailored solutions!