The process of carbon regeneration, also known as reactivation, involves thermally treating activated carbon to remove adsorbed contaminants from its surface. This process restores the carbon's adsorption capacity, allowing it to be reused. The regeneration process typically involves heating the carbon to high temperatures in a controlled environment, which decomposes and volatilizes the adsorbed substances. The regenerated carbon can then be reused in various applications, making it a cost-effective and environmentally friendly solution.
Key Points Explained:
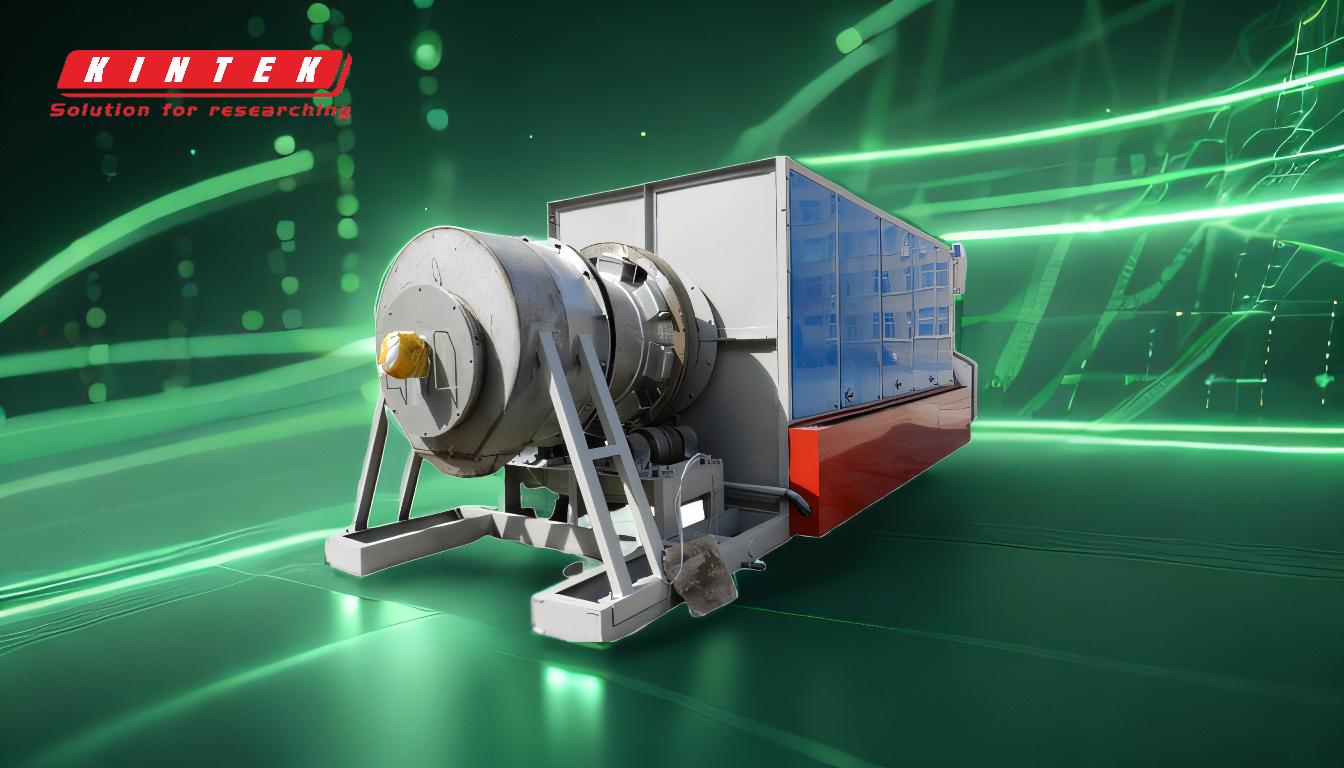
-
Definition of Carbon Regeneration:
- Carbon regeneration is the process of thermally treating activated carbon to remove adsorbed contaminants, restoring its adsorption capacity.
- This process is also referred to as reactivation.
-
Purpose of Regeneration:
- The primary goal is to remove adsorbed components from the carbon surface, allowing it to be reused.
- This extends the life of the activated carbon, reducing the need for frequent replacement and lowering operational costs.
-
Thermal Processing:
- The regeneration process involves heating the carbon to high temperatures, typically between 600°C and 900°C.
- This high-temperature environment decomposes and volatilizes the adsorbed substances, effectively cleaning the carbon surface.
-
Controlled Environment:
- The process is conducted in a controlled environment, often in a rotary kiln or a multiple hearth furnace.
- This ensures that the carbon is evenly heated and that the adsorbed contaminants are completely removed.
-
Destruction of Adsorbed Components:
- The adsorbed components are almost completely destroyed during the regeneration process.
- This results in a regenerated carbon that has adsorption properties similar to virgin activated carbon.
-
Reuse of Regenerated Carbon:
- After regeneration, the carbon can be reused in various applications, such as water treatment, air purification, and chemical processing.
- This makes the process both cost-effective and environmentally sustainable.
-
Environmental and Economic Benefits:
- Regeneration reduces the need for new activated carbon, conserving natural resources.
- It also minimizes waste, as the regenerated carbon can be used multiple times before it needs to be replaced.
-
Quality of Regenerated Carbon:
- The quality of the regenerated carbon depends on the efficiency of the regeneration process.
- Properly regenerated carbon should have adsorption properties comparable to new activated carbon.
By understanding these key points, purchasers of equipment and consumables can make informed decisions about the use and regeneration of activated carbon, ensuring optimal performance and cost-efficiency in their operations.
Summary Table:
Aspect | Details |
---|---|
Definition | Thermal treatment to remove contaminants from activated carbon. |
Purpose | Restores adsorption capacity, enabling reuse and reducing replacement costs. |
Temperature Range | 600°C to 900°C in a controlled environment. |
Equipment Used | Rotary kiln or multiple hearth furnace. |
Applications | Water treatment, air purification, chemical processing. |
Benefits | Cost-effective, environmentally sustainable, and conserves resources. |
Quality | Comparable adsorption properties to virgin activated carbon. |
Discover how carbon regeneration can optimize your operations—contact us today!