E-beam evaporation, or electron beam evaporation, is a highly precise physical vapor deposition (PVD) technique used to deposit thin, high-purity coatings on substrates. The process involves using a high-power electron beam to heat and vaporize a source material in a vacuum chamber. The vaporized material then condenses onto a substrate, forming a thin film. This method is favored for its ability to produce high-density coatings with excellent adhesion, low impurity levels, and high deposition rates. It is widely used in industries requiring high-performance coatings, such as semiconductors, optics, and aerospace.
Key Points Explained:
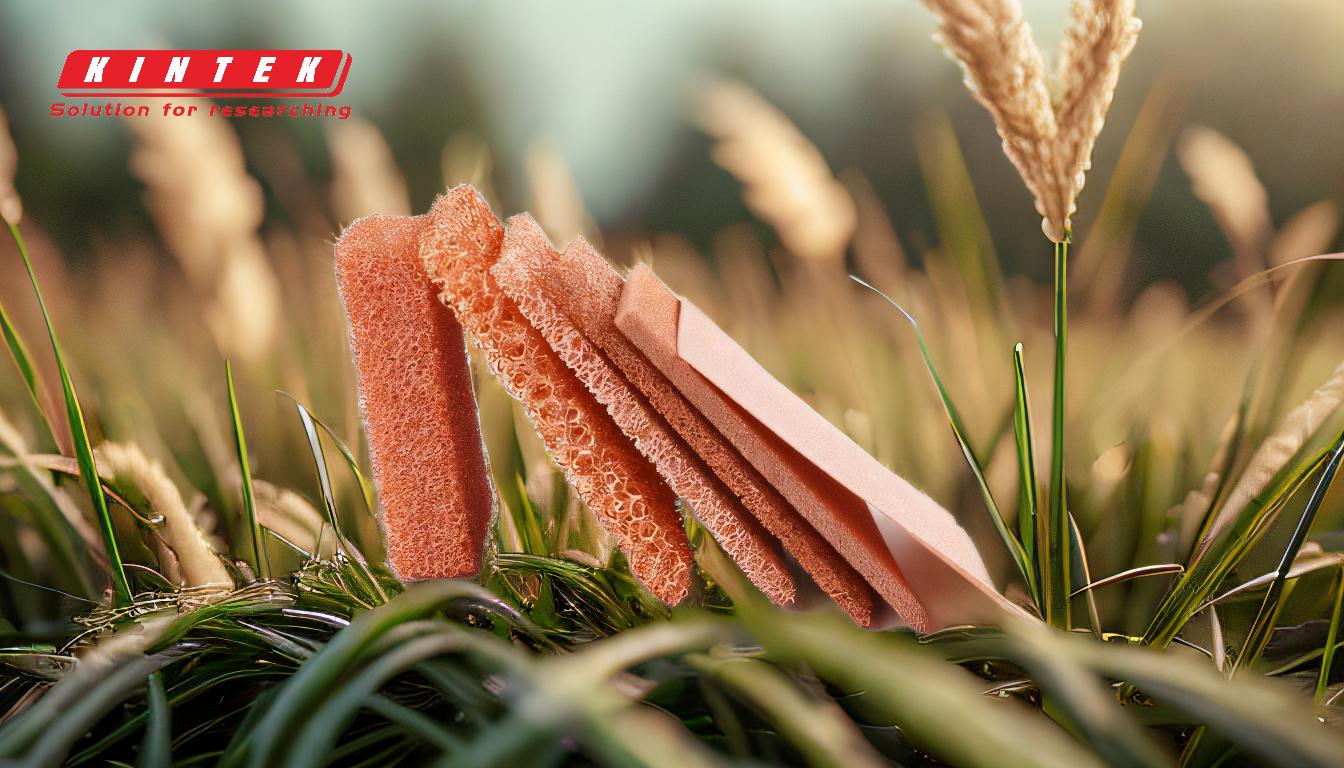
-
Components of an E-Beam Evaporation System:
- Vacuum Chamber: The process occurs in a vacuum to minimize contamination and ensure high-purity coatings.
- Electron Beam Source: Typically made of tungsten, this component generates electrons when heated to over 2,000°C. Magnets focus the electrons into a beam.
- Crucible: Holds the source material and is water-cooled to prevent melting and contamination.
- Substrate: Positioned above the source material, it receives the evaporated particles to form the thin film.
-
Process Steps:
- Electron Beam Generation: The electron beam source heats up and emits electrons, which are focused into a beam.
- Material Heating: The electron beam is directed at the crucible, heating the source material to its evaporation point.
- Evaporation: The source material vaporizes due to the intense heat, and the vapor flows upward in the vacuum chamber.
- Deposition: The vaporized material condenses onto the substrate, forming a thin, uniform coating.
-
Advantages of E-Beam Evaporation:
- High Purity: The vacuum environment and water-cooled crucible minimize contamination, resulting in high-purity films.
- High Deposition Rates: The process can achieve rapid vapor deposition rates, ranging from 0.1 μm/min to 100 μm/min.
- Versatility: Compatible with a wide range of materials, including high-temperature metals and metal oxides.
- Multi-Layer Deposition: Allows for the deposition of multiple layers without venting the chamber.
- Directionality and Uniformity: The process offers good directionality and excellent uniformity, especially when using masks and planetary systems.
-
Applications:
- Semiconductors: Used for depositing thin films in semiconductor manufacturing.
- Optics: Ideal for creating high-performance optical coatings.
- Aerospace: Applied in the production of coatings for aerospace components requiring high durability and performance.
-
Material Considerations:
- The source material must be able to withstand high temperatures and have a vapor pressure suitable for evaporation under vacuum conditions.
- Common materials include metals (e.g., aluminum, gold) and metal oxides (e.g., titanium dioxide).
-
Challenges and Solutions:
- Contamination Risk: The water-cooled crucible and vacuum environment significantly reduce the risk of contamination.
- Material Utilization Efficiency: The process is highly efficient, with minimal material waste.
- Complexity: Requires precise control of the electron beam and vacuum conditions, which can be technically challenging but is managed through advanced system design.
By understanding these key points, equipment and consumable purchasers can make informed decisions about implementing e-beam evaporation in their processes, ensuring high-quality, high-performance coatings for their applications.
Summary Table:
Aspect | Details |
---|---|
Components | Vacuum chamber, electron beam source, crucible, substrate |
Process Steps | Electron beam generation, material heating, evaporation, deposition |
Advantages | High purity, high deposition rates, versatility, multi-layer capability |
Applications | Semiconductors, optics, aerospace |
Material Considerations | High-temperature metals, metal oxides (e.g., aluminum, gold, titanium dioxide) |
Challenges | Contamination risk, material utilization efficiency, system complexity |
Discover how e-beam evaporation can enhance your processes—contact our experts today for more information!