The process of forging press involves shaping metal using compressive forces applied through different types of presses. The three main types of forging presses—mechanical, hydraulic, and screw—each operate with distinct mechanisms to achieve the desired metal deformation. Understanding these processes is crucial for selecting the right equipment for specific forging applications.
Key Points Explained:
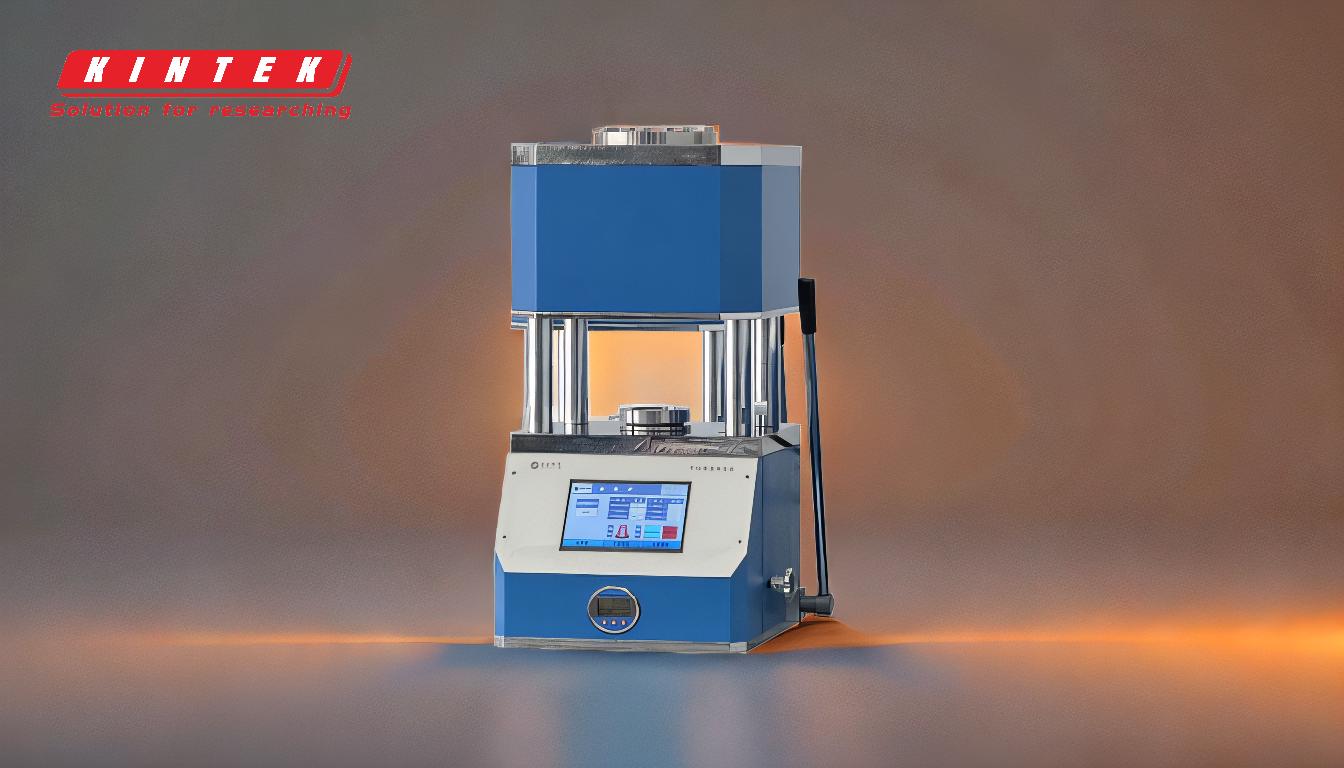
-
Mechanical Press Forging
- Mechanism: A mechanical press converts the rotational motion of a motor into the linear motion of a ram. This is typically achieved through a crank or eccentric mechanism.
- Operation: The motor drives a flywheel, which stores energy. This energy is then transferred to the ram, which moves downward to apply force to the workpiece.
-
Advantages:
- High speed and efficiency, making it suitable for mass production.
- Consistent force application, ensuring uniform deformation of the metal.
- Applications: Commonly used in industries requiring high-volume production, such as automotive and aerospace.
-
Hydraulic Press Forging
- Mechanism: A hydraulic press uses hydraulic fluid to move a piston, which in turn moves the ram. The force is generated by the pressure of the hydraulic fluid.
- Operation: The hydraulic system allows for precise control over the speed and force of the ram. The operator can adjust the pressure to achieve the desired deformation.
-
Advantages:
- High force capability, suitable for forging large or complex parts.
- Versatility in terms of force and speed control, allowing for a wide range of applications.
- Applications: Ideal for forging large components, such as those used in heavy machinery and construction equipment.
-
Screw Press Forging
- Mechanism: A screw press uses a screw mechanism to actuate the ram. The rotation of the screw is converted into linear motion, driving the ram downward.
- Operation: The screw mechanism can be driven by a motor or manually. The energy is stored in the flywheel and released through the screw to the ram.
-
Advantages:
- High energy efficiency, as the flywheel stores and releases energy effectively.
- Suitable for forging operations requiring high precision and control.
- Applications: Often used in the production of precision components, such as gears and shafts, where accuracy is critical.
-
General Forging Process Steps
- Heating: The metal workpiece is heated to a temperature that makes it malleable but not molten. This temperature varies depending on the type of metal.
- Positioning: The heated workpiece is placed on the die or anvil of the press.
- Deformation: The press applies force to the workpiece, causing it to deform and take the shape of the die.
- Cooling: After forging, the workpiece is allowed to cool, either naturally or through controlled cooling processes, to achieve the desired material properties.
- Finishing: The forged part may undergo additional processes, such as trimming, machining, or heat treatment, to achieve the final specifications.
-
Selection Criteria for Forging Presses
- Material Type: Different metals require different forging temperatures and forces. The choice of press should align with the material properties.
- Part Complexity: Complex parts may require presses with higher precision and control, such as hydraulic or screw presses.
- Production Volume: High-volume production may benefit from the speed and efficiency of mechanical presses.
- Cost Considerations: The initial investment and operational costs of the press should be considered in relation to the production requirements.
Understanding the process of forging press and the different types of presses available is essential for optimizing production efficiency and achieving high-quality forged components. Each type of press offers unique advantages, making them suitable for specific applications and production needs.
Summary Table:
Type of Press | Mechanism | Advantages | Applications |
---|---|---|---|
Mechanical Press | Converts rotational motion to linear motion via crank/eccentric mechanism | High speed, efficiency, consistent force | Automotive, aerospace (high-volume production) |
Hydraulic Press | Uses hydraulic fluid to move piston and ram | High force capability, precise control | Heavy machinery, construction (large/complex parts) |
Screw Press | Uses screw mechanism to actuate ram | High energy efficiency, precision | Gears, shafts (precision components) |
Ready to optimize your forging process? Contact us today for expert guidance!