Hot isostatic pressing (HIP) is a critical process in the fabrication of ceramic matrix composites, combining high temperature and pressure to achieve densification and eliminate internal defects. This method is particularly effective for creating complex 3D shapes with uniform material properties. The process involves placing powdered materials into molds, applying uniform pressure from all directions, and heating to high temperatures to sinter or densify the material. This ensures high compact densities and uniform physical parameters, making it ideal for high-performance applications in industries such as aerospace and energy.
Key Points Explained:
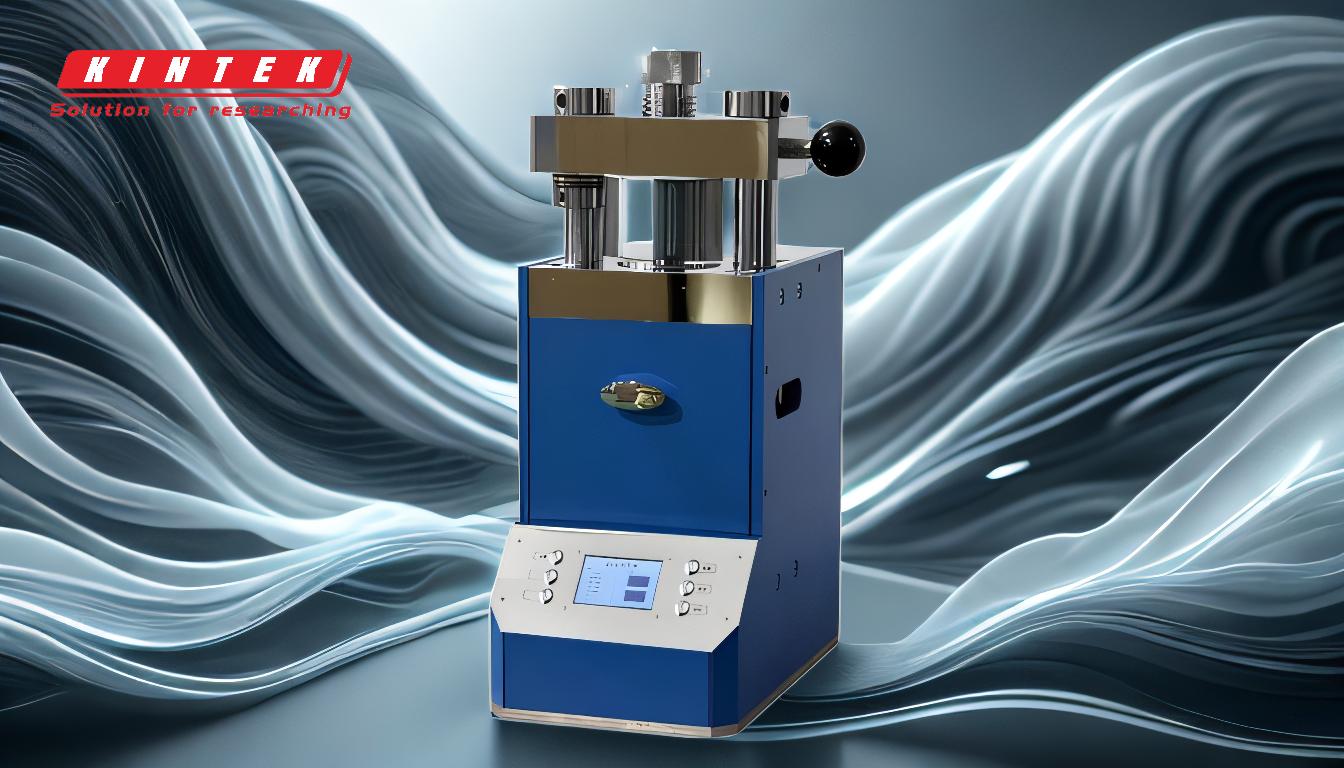
-
Introduction to Hot Isostatic Pressing (HIP):
- HIP is a sintering variant used for 3D shapes, where external pressure and high temperature are applied simultaneously to achieve densification.
- This process is essential for producing materials with uniform properties and eliminating internal defects, such as porosity, which can compromise material performance.
-
Process Overview:
- Powder Preparation: The ceramic matrix composite powder is prepared and poured into a flexible mold.
- Mold Sealing: The mold is sealed to prevent contamination and ensure uniform pressure application.
- Loading into HIP Chamber: The sealed mold is placed into a warm isostatic press chamber.
- Application of Pressure and Heat: High pressure (100–200 MPa) and high temperature (1000–2200°C) are applied uniformly from all directions.
- Densification: The combination of heat and pressure sinters the powder, resulting in a dense, defect-free material.
- Cooling and Removal: After the process, the material is cooled, and the compacted product is removed from the mold.
-
Key Advantages of HIP:
- Uniform Density: The application of equal pressure from all directions ensures uniform density and material properties.
- Complex Shapes: HIP allows for the creation of complex shapes that cannot be achieved with traditional uniaxial pressing methods.
- Defect Elimination: Internal defects, such as porosity and uneven cooling rates, are eliminated, improving the material's mechanical properties.
-
Applications of HIP in Ceramic Matrix Composites:
- HIP is widely used in industries requiring high-performance materials, such as aerospace, energy, and automotive.
- It is particularly effective for densifying castings made from materials like aluminum, titanium, and high-temperature alloys.
-
Equipment and Capacities:
- HIP equipment comes in various sizes, including small, medium, and large capacities, to accommodate different production needs.
- The choice of equipment depends on the size and complexity of the parts being produced.
-
Comparison with Other Processes:
- Unlike uniaxial pressing, HIP applies pressure uniformly, resulting in materials with fewer defects and better mechanical properties.
- HIP is more suitable for complex shapes and high-performance applications compared to traditional sintering methods.
-
Challenges and Considerations:
- Cost: HIP equipment and processes can be expensive, making it less suitable for low-cost applications.
- Material Compatibility: Not all materials are suitable for HIP, and careful selection is required to ensure optimal results.
- Process Control: Precise control of temperature and pressure is essential to achieve the desired material properties.
By understanding the detailed steps and advantages of hot isostatic pressing, manufacturers can make informed decisions about using this process for producing high-quality ceramic matrix composites. The ability to create complex shapes with uniform properties makes HIP an invaluable tool in advanced material fabrication.
Summary Table:
Step | Description |
---|---|
Powder Preparation | Ceramic matrix composite powder is prepared and poured into a flexible mold. |
Mold Sealing | The mold is sealed to prevent contamination and ensure uniform pressure application. |
Loading into HIP | The sealed mold is placed into a warm isostatic press chamber. |
Pressure & Heat | High pressure (100–200 MPa) and high temperature (1000–2200°C) are applied uniformly. |
Densification | The powder sinters into a dense, defect-free material. |
Cooling & Removal | The material is cooled, and the compacted product is removed from the mold. |
Learn how HIP can elevate your material fabrication—contact our experts today for tailored solutions!