Hot-pressing sintering is a specialized manufacturing process that combines high temperature and pressure to compact and bond powdered materials into a dense, solid structure. This process is particularly useful for materials with high melting points, such as ceramics and certain metals, where traditional melting methods are impractical. The process involves several stages, including powder preparation, compaction, heating under pressure, and cooling. The result is a material with reduced porosity, enhanced mechanical properties, and improved durability. This method is widely used in industries requiring high-performance materials, such as aerospace, electronics, and tool manufacturing.
Key Points Explained:
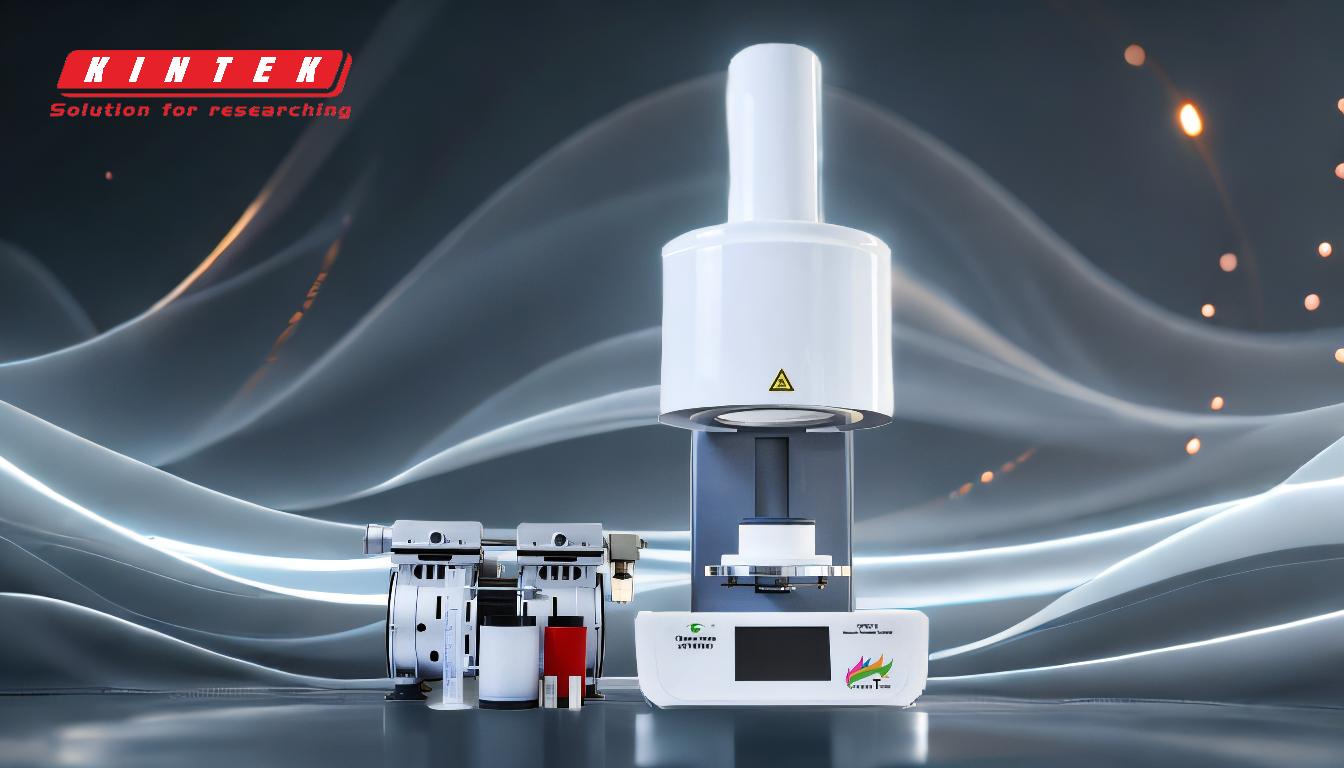
-
Powder Preparation:
- The process begins with the preparation of the raw material in powder form. This involves mixing the primary materials with any necessary coupling agents to ensure uniformity. The powder must be finely ground to facilitate better compaction and bonding during the sintering process.
-
Compaction:
- The powder is then compacted into a specific shape using high pressure. This step is crucial for eliminating voids and ensuring the material has a uniform density. The compaction process can be done using various methods, such as uniaxial pressing or isostatic pressing, depending on the desired shape and properties of the final product.
-
Heating Under Pressure:
- The compacted material is placed in a hot-pressing sintering furnace, where it is subjected to both high temperature and high pressure. The temperature is carefully controlled to be below the material’s melting point, allowing the particles to bond through diffusion without liquefying. The pressure helps to further reduce porosity and enhance the material’s density.
-
Cooling:
- After the heating phase, the material is allowed to cool gradually. This cooling process is critical for the material to solidify into a rigid and cohesive structure. Rapid cooling can lead to internal stresses and defects, so controlled cooling is essential to achieve the desired mechanical properties.
-
Equipment Used:
- The hot-pressing sintering furnace is a key piece of equipment in this process. It typically consists of a furnace body, a heating element, a pressure system, and a vacuum system. The furnace must be capable of maintaining high temperatures and pressures in a controlled environment to ensure the quality of the sintered product.
-
Applications:
- Hot-pressing sintering is used in various industries to produce high-performance materials. For example, it is used in the aerospace industry to create components that can withstand extreme temperatures and stresses. In the electronics industry, it is used to produce substrates and insulators with high thermal conductivity and electrical insulation properties. The process is also used in the manufacturing of cutting tools and wear-resistant components.
By following these steps, hot-pressing sintering allows for the production of materials with superior mechanical properties, making it an essential process in advanced manufacturing.
Summary Table:
Stage | Description |
---|---|
Powder Preparation | Raw materials are ground into fine powder and mixed with coupling agents for uniformity. |
Compaction | Powder is compacted into a specific shape under high pressure to eliminate voids. |
Heating Under Pressure | Compacted material is heated below melting point under high pressure to bond particles. |
Cooling | Material is cooled gradually to solidify into a dense, cohesive structure. |
Equipment | Hot-pressing sintering furnace with heating, pressure, and vacuum systems. |
Applications | Aerospace, electronics, and tool manufacturing for high-performance components. |
Discover how hot-pressing sintering can elevate your material production—contact our experts today!