The process of isostatic graphite involves several key steps, starting from powder preparation to the final machining and shipment of the product. The process can be broadly categorized into two main methods: hot isostatic pressing (HIP) and cold isostatic pressing (CIP). Both methods involve the application of uniform pressure to the material, but they differ in terms of temperature and the medium used for pressure application. The final product undergoes machining, purification, and surface treatment before being shipped to the customer.
Key Points Explained:
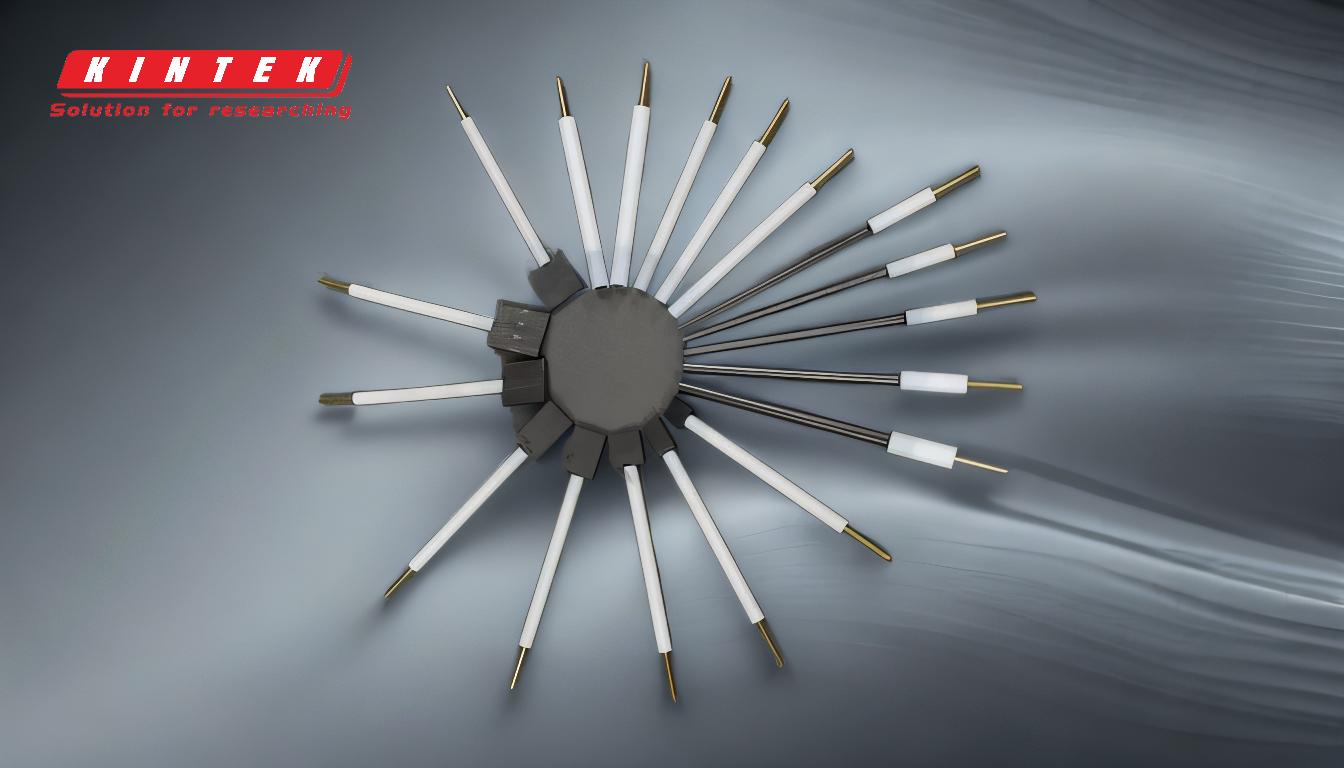
-
Powder Preparation:
- The process begins with the preparation of graphite powder. This powder is typically made from high-purity carbon sources and is carefully processed to ensure uniformity in particle size and composition. The quality of the powder is crucial as it directly affects the properties of the final product.
-
Cladding Design and Manufacturing:
- In the case of hot isostatic pressing, a cladding (or container) is designed and manufactured to hold the graphite powder. The cladding must be able to withstand high temperatures and pressures without contaminating the graphite. It is usually made from materials like stainless steel or other high-temperature alloys.
-
Powder Filling and Degassing Sealing:
- The prepared graphite powder is then filled into the cladding. Before sealing, the powder is degassed to remove any trapped air or moisture, which could otherwise cause defects in the final product. The cladding is then sealed to create a vacuum or inert atmosphere inside.
-
Hot Isostatic Pressing (HIP):
- The sealed cladding is placed into a hot isostatic press. The chamber is filled with inert argon gas, and the temperature is raised to the desired level. The pressure is applied uniformly from all directions, which helps in achieving a dense and homogeneous structure. The temperature, pressure, and duration of the process are closely monitored and controlled to ensure the desired properties are achieved. After the pressing, the chamber is depressurized and cooled down before the parts are removed.
-
Cold Isostatic Pressing (CIP):
- In cold isostatic pressing, the graphite powder is placed into a flexible mold, which is then submerged in a pressurized fluid (usually water with a corrosion inhibitor). The pressure is applied uniformly from all directions, compacting the powder into a green body. CIP is typically used for simpler shapes and does not involve high temperatures, making it suitable for materials that are sensitive to heat.
-
Removal of the Cladding:
- After the isostatic pressing process, the cladding is removed from the pressed graphite. This step requires precision to avoid damaging the graphite. The removal process may involve mechanical or chemical methods, depending on the type of cladding used.
-
Subsequent Processing Operations:
- The pressed graphite undergoes additional processing steps, such as machining to achieve the desired dimensions and surface finish. If required, the graphite may also undergo purification to remove any impurities. Surface treatments, such as coating or polishing, may be applied to enhance the properties of the graphite.
-
Final Machining and Shipment:
- The final step involves machining the graphite according to the customer's specifications. This may include cutting, drilling, or grinding to achieve the precise dimensions required. After machining, the graphite is inspected for quality and then shipped to the customer.
The process of isostatic molding is critical in producing high-quality isostatic graphite, which is widely used in various industries, including semiconductor manufacturing, aerospace, and energy. The uniform pressure application ensures that the graphite has consistent properties throughout, making it suitable for demanding applications.
Summary Table:
Step | Description |
---|---|
1. Powder Preparation | High-purity graphite powder is prepared for uniformity in particle size and composition. |
2. Cladding Design | A cladding is designed to withstand high temperatures and pressures for HIP. |
3. Powder Filling | Graphite powder is filled into the cladding and degassed to remove air/moisture. |
4. Hot Isostatic Pressing | Uniform pressure and high temperature are applied using inert argon gas. |
5. Cold Isostatic Pressing | Uniform pressure is applied using a pressurized fluid for simpler shapes. |
6. Cladding Removal | The cladding is removed without damaging the graphite. |
7. Subsequent Processing | Machining, purification, and surface treatments are applied. |
8. Final Machining | Graphite is machined to customer specifications and shipped. |
Need high-quality isostatic graphite for your industry? Contact our experts today to learn more!