The manufacturing of semiconductors is a highly complex and precise process that involves multiple steps to create integrated circuits (ICs) on silicon wafers. The process begins with the formation of layers, such as ammonia and interlayer insulators, followed by photolithography to create patterns. Etching is then used to shape the layers according to the pattern, and doping is performed to modify the electrical properties of specific regions. The final steps involve removing the photoresist and ensuring the semiconductor device meets the required specifications. This process is repeated multiple times to build up the intricate layers and structures needed for modern semiconductor devices.
Key Points Explained:
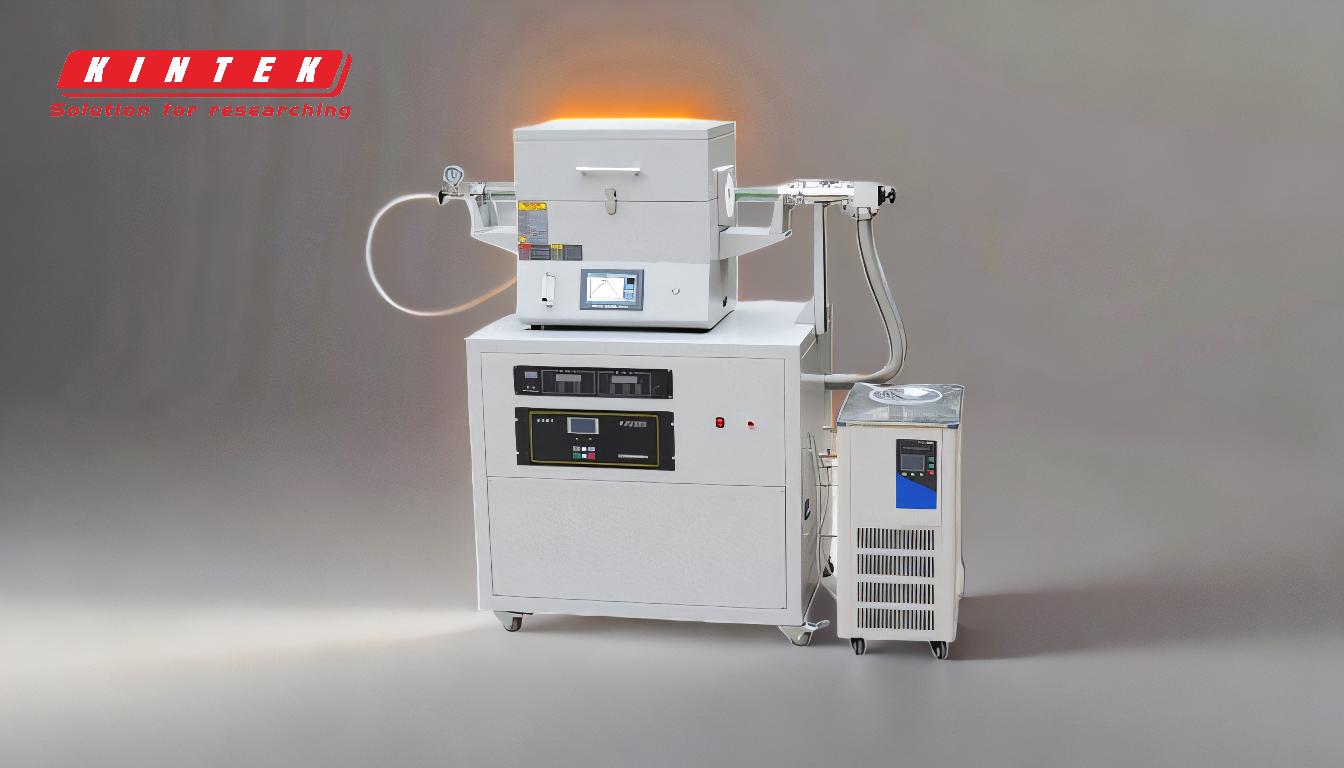
-
Formation of Layers:
- The process starts with the formation of an ammonia layer on the interlayer insulator. This layer is crucial for creating a stable base for subsequent steps.
- The interlayer insulator is typically made of materials like silicon dioxide (SiO₂) and serves as a barrier between different conductive layers in the semiconductor device.
-
Photolithography:
- A light-resistant layer, known as photoresist, is applied over the ammonia layer. This layer is sensitive to ultraviolet (UV) light and is used to create patterns on the wafer.
- A photomask, which contains the desired circuit pattern, is placed over the photoresist. The wafer is then exposed to UV light, which hardens the photoresist in the exposed areas.
-
Development of Photoresist Pattern:
- After exposure, the wafer is developed, which involves washing away the unexposed (soft) areas of the photoresist. This leaves behind a patterned photoresist layer that matches the circuit design.
- The pattern serves as a mask for the subsequent etching process.
-
Etching:
- The etching process removes the ammonia layer and interlayer insulator in the areas not protected by the photoresist pattern. This can be done using wet chemical etching or dry plasma etching, depending on the materials and precision required.
- The result is a precise replication of the circuit pattern on the wafer.
-
Removal of Photoresist:
- Once the etching is complete, the remaining photoresist is removed through a process called photoresist stripping. This is typically done using chemical solvents or plasma ashing.
- The wafer is now ready for the next set of processes, which may include additional layering, patterning, and etching.
-
Doping:
- Doping is a critical step where specific regions of the semiconductor are treated with impurities (dopants) to alter their electrical properties. This is done to create n-type (electron-rich) or p-type (hole-rich) regions within the semiconductor.
- Doping can be achieved through techniques like ion implantation or diffusion, where dopant atoms are introduced into the semiconductor material.
-
Repeating the Process:
- The entire process is repeated multiple times to build up the complex layers and structures required for modern semiconductor devices. Each iteration adds a new layer of circuitry, with precise alignment (lithography alignment) ensuring that each layer is correctly positioned relative to the others.
-
Final Inspection and Testing:
- After all the layers and structures are formed, the wafer undergoes rigorous inspection and testing to ensure that the semiconductor devices meet the required specifications.
- Defective devices are identified and either repaired or discarded, while functional devices are prepared for packaging and integration into electronic products.
This step-by-step process, though simplified here, involves advanced technologies and meticulous attention to detail to produce the high-performance semiconductors that power today's electronic devices.
Summary Table:
Step | Description |
---|---|
Formation of Layers | Ammonia and interlayer insulator layers are formed to create a stable base. |
Photolithography | A photoresist layer is applied and exposed to UV light to create circuit patterns. |
Development of Photoresist | Unexposed photoresist is washed away, leaving a patterned mask for etching. |
Etching | Layers are etched to replicate the circuit pattern on the wafer. |
Removal of Photoresist | Remaining photoresist is stripped, preparing the wafer for further processing. |
Doping | Impurities are introduced to alter electrical properties in specific regions. |
Repeating the Process | Steps are repeated to build complex layers and structures. |
Final Inspection | Wafers are tested to ensure devices meet specifications before packaging. |
Learn more about semiconductor manufacturing and how it impacts modern technology—contact our experts today!